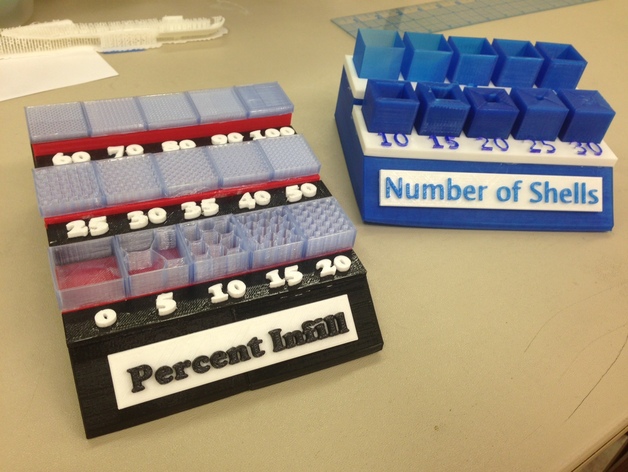
Infill Percent Display by Thingiverse user duncan916
There’s so much more that goes into a 3D print than many people realize. To those unfamiliar with how the process works, it looks like simple magic – but there are a lot of factors that go into the process of turning a design into a physical 3D object, and a lot of decisions to be made. For example, what kind of infill should be used in a particular print? Infill percentage and pattern affect a lot more than just the weight and strength of a print, as studies have shown, and determining the optimal parameters can be tricky.
There are a lot of infill patterns one can choose from, including everything from standard honeycombs and triangles to cats and sharks, courtesy of MakerBot. One of the tricky aspects of infill optimization is trying to strike a good balance between strength and weight – it can be tough to design a strong, solid part without it ending up as heavy as a doorstop. But now a group of researchers from the Technical University of Denmark, Delft University of Technology, and the Technical University of Munich have developed a new type of infill that imparts durable strength without weighing an object down.
Like so many of the most effective human inventions, the researchers’ infill design was inspired by naturally occurring structures – in this case, bone.
“The so-called infill optimization automatically generates an porous infill structure for 3D printing,” Dr. Jun Wu, Assistant Professor of Advanced Manufacturing at TU Delft, told 3DPrint.com. “The numerically optimized structure is very similar to the trabecular bone, which is lightweight and mechanically strong. It gives valuable insight for linking engineering infill and nature infill.”
Trabecular bone, also known as cancellous or spongy bone, is less dense than cortical bone, the other type of bone tissue found in the human body. Composed of tiny lattice structures, trabecular bone is lightweight and flexible, making up the interior of bone structures, particularly near joints and in the ribs, skull and vertebrae. It may possess less strength than the exterior cortical bone, but it’s still plenty strong, especially for its light weight. Those are the properties that inspired the research team, and in a paper entitled “Infill Optimization for Additive Manufacturing — Approaching Bone-like Porous Structures,” they detail how they worked to translate those properties from nature to 3D printing.
According to the team, their methodology built on voxel-wise topology optimization.
“In particular, for the purpose of generating sparse yet stable structures distributed in the interior of a given shape, we propose upper bounds on the localized material volume in the proximity of each voxel in the design domain,” the paper states. “We then aggregate the local per-voxel constraints by their p-norm into an equivalent global constraint, in order to facilitate an efficient optimization process. Implemented on a high-resolution topology optimization framework, our results demonstrate mechanically optimized, detailed porous structures which mimic those found in nature.”
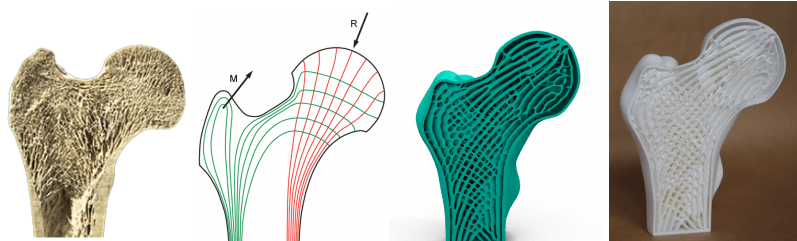
From left to right: Cross-section of a human femur showing cortical structures on the shell and trabecular structures in the interior; illustration of principle stress directions under major mechanical loads; cross-section of the optimized porous infill in a 3D bone model; the 3D printed bone model
A complex mathematical algorithm was designed to generate an infill that resembled the porous structure of bone. The study details the multiple variables and sub-structures the researchers tested. In the end, the porous, trabecular bone-like structure was concluded to be highly promising for 3D printing – particularly large, lightweight parts. There’s still work to be done to further optimize the technique, but the printed structures held up well in testing for strength and robustness.
“We have presented a structural optimization method for obtaining stiffness optimized porous structures,” the paper concludes. “These numerically optimized structures visually resemble trabecular bone, which is lightweight and robust with respect to material deficiency and force variations. This makes the optimized interior structures an ideal candidate for application-specific infill in additive manufacturing.”
Dr. Wu is the first author of the paper; additional contributors include Niels Aage, Rüdiger Westermann, and Ole Sigmund. Discuss in the Bone Infill forum at 3DPB.com.
Subscribe to Our Email Newsletter
Stay up-to-date on all the latest news from the 3D printing industry and receive information and offers from third party vendors.
Print Services
Upload your 3D Models and get them printed quickly and efficiently.
You May Also Like
Making 3D Printing Personal: How Faraz Faruqi Is Rethinking Digital Design at MIT CSAIL
What if your 3D printer could think more like an intelligent assistant, able to reason through a design idea, ask questions, and deliver something that works exactly the way the...
Reinventing Reindustrialization: Why NAVWAR Project Manager Spencer Koroly Invented a Made-in-America 3D Printer
It has become virtually impossible to regularly follow additive manufacturing (AM) industry news and not stumble across the term “defense industrial base” (DIB), a concept encompassing all the many diverse...
Heating Up: 3D Systems’ Scott Green Discusses 3D Printing’s Potential in the Data Center Industry
The relentless rise of NVIDIA, the steadily increasing pledges of major private and public investments in national infrastructure projects around the world, and the general cultural obsession with AI have...
Formlabs Teams Up with DMG MORI in Japan
In late June, Nick Graham, Chief Revenue Officer at Formlabs, announced on LinkedIn that the company had partnered with DMG MORI, one of the world’s leading machine tool companies, to...