Continuous oscillatory baffled reactors (COBRs) may be baffling to many, but for Victor Sans and his team at the University of Nottingham, the equipment is vital to their work. The complex structure of the reactors, which are used to crystallize solids from continuous flow reactions, makes them superior to simpler tubular flow reactors in that it reduces solid deposition and improves reagent mixing. Unfortunately, that complex structure also means that they’re very difficult and time-consuming to fabricate – they’re made from blown glass and require high-powered pumps that typical research labs don’t have.
Sans and his team decided to see if there was a simpler way to manufacture COBRs – and of course there was, in the form of 3D printing. In a study entitled “Advanced reactor engineering with 3D printing for the continuous-flow synthesis of silver nanoparticles,” Sans’ group documents how they created a COBR for silver nanoparticle synthesis. Customizing the design for their specific study, they 3D printed a COBR using an SLA printer for no more than the cost of resin – about £8 worth. Not only did 3D printing the reactors reduce cost and time – each one took about five hours to print – it allowed the lab to create COBRs at a much smaller scale for more precise work.
3D printing the COBRs also means that the lab can create as many as they want, accelerating their work by running multiple reactors at the same time. According to Sans, the flow dynamics of the miniaturized COBRs, or mCOBRs, allow for suspensions of nanoparticles that are much smaller and more regular than those produced by a tubular reactor of similar channel width, which is quickly fouled up by silver deposits. Later, tubular reactors.“This scale is unprecedented,” says Sans. “It bridges the gap between what would be a microfluidic device and a mesoscale reactor…[There is] nothing stopping us from using our imaginations to come up with completely new geometries [for reactors].”
“Residence time distribution experiments have been employed to demonstrate that these small scale reactors offer improved mixing conditions at a millimetre scale, when compared to tubular reactors,” the research paper states. “Nearly monodisperse silver nanoparticles have been synthesised employing mCOBR, showing higher temporal stability and superior control over particle size distribution than tubular flow reactors.”
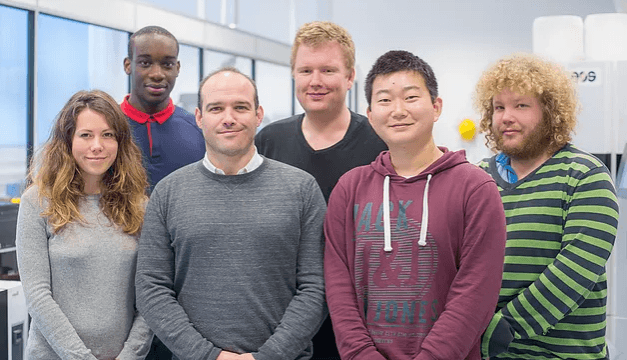
Victor Sans (front row, second from left) with members of his research group. [Photo: Sans Research Group]
Additional authors of the mCOBR study include Obinna Okafor, Andreas Weilhard, Jesum A. Fernandes, Erno Karjalainen, and Ruth Goodridge. You can access the full study here. Discuss in the Lab Equipment forum at 3DPB.com.
[Source: Chemistry World]
Subscribe to Our Email Newsletter
Stay up-to-date on all the latest news from the 3D printing industry and receive information and offers from third party vendors.
Print Services
Upload your 3D Models and get them printed quickly and efficiently.
You May Also Like
U.S. Navy Lab Uses 3D Printing to Reduce Tooling Lead Time By Over 90%
The F-35 Lightning II Joint Program Office (JPO), responsible for life-cycle management of the key fifth-generation joint strike fighter (JSF) system used by the U.S., its allies, and its partners,...
Etsy Design Rule Change Reduces Selection of 3D Printed Goods
Online marketplace Etsy has implemented a rule change requiring all 3D printed goods on the site to be original designs. The update to the site’s Creativity Standards states, ¨Items produced using...
Honeywell Qualifies 6K Additive’s Nickel 718 for 3D Printed Aerospace & Defense Parts
6K Additive is renowned for manufacturing sustainable additive manufacturing (AM) powder, and offers a wide portfolio of premium metal and alloy powders that include titanium, copper, stainless steel, and nickel,...
MetalWorm Sells WAAM Systems to Research Institutes in Brazil and Malaysia
Turkish WAAM firm MetalWorm has sold a system in Malaysia and another in Brazil. This is an excellent example of a few emerging trends in additive. Firstly, WAAM was experimented...