Blue Origin’s Liquid-Fueled BE-4 Rocket Engine Utilizes Additive Manufacturing to Make Boost Pump Components
We’ve heard about Jeff Bezos before: not only is he the billionaire who founded Amazon, but he also founded his own space venture, Blue Origin, more than 16 years ago. As of October 2016, Blue Origin has conducted five successful test flights of its New Shepard suborbital rocket ship, and the company even threw its hat in the ring back in 2014 to help produce the vitally important RD-180 engine, used to send the Atlas V rocket into space, completely in the US, offering to develop a liquid-fueled version of the engine. Now, according to an article on Yahoo, Bezos recently gave a mass email update about Blue Origin’s process of building this next-generation rocket engine, known as the BE-4, that will be fueled by liquefied natural gas. No surprise here – additive manufacturing plays a part in building the BE-4.
“Store the propellants in low-pressure light tanks, and then pump the propellants up to high pressure just ahead of injection into the main chamber,” Bezos said. “For even more performance, you can add one or more boost pumps ahead of the main pumps. We’ve done that on the oxidizer side of our BE-4 engine. Our Ox Boost Pump (OBP) design leverages 3-D additive manufacturing to make many of the key components. The housing is a single printed aluminum part and all of the stages of the hydraulic turbine are printed from Monel, a nickel alloy. This manufacturing approach allows the integration of complex internal flow passages in the housing that would be much more difficult to make using conventional methods. The turbine nozzle and rotors are also 3-D printed and require minimum machining to achieve the required fits.”
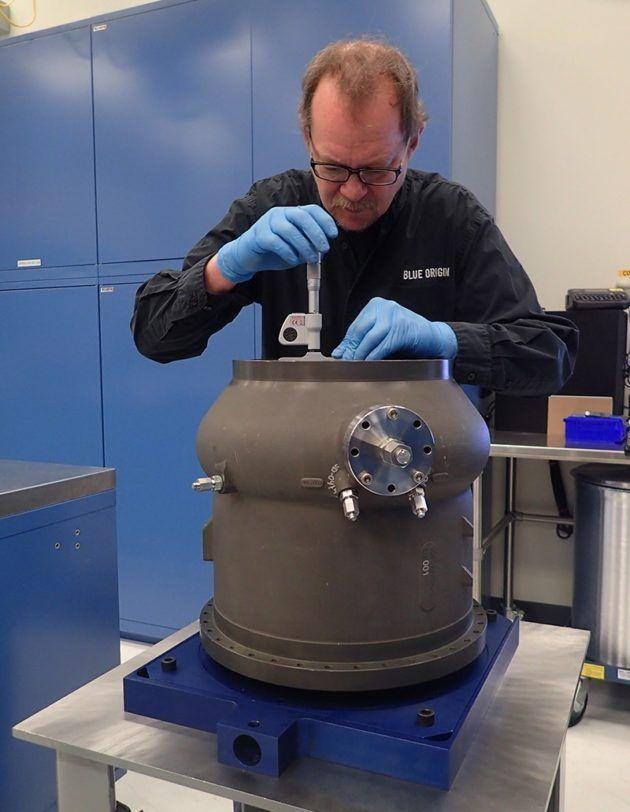
An employee works on the BE-4 Ox Boost Pump prior to engine installation. [Blue Origin Photo via Jeff Bezos]
![[Image: Blue Origin]](https://3dprint.com/wp-content/uploads/2017/02/Blue-Origin-liftoff-closeup-300x200.png)
The New Shepard space vehicle rockets off the West Texas launch pad and accelerates toward its planned test altitude of 307,000 feet. [Image: Blue Origin]
Speaking of launch facilities, the State of Florida is budgeting $17 million from the Department of Transportation for Blue Origin’s future launch pad at the Kennedy Space Center. Launch Complex 36 will be the site of the company’s rocket launches for the reusable New Glenn orbital rockets. Back in September 2015, Bezos announced his plans to use the pad, and has promised that Blue Origin will match the state’s contributions, which takes the refurbishing budget up to $34 million. The company also plans to open a $200 million, 750,000-square-foot factory for the New Glenn rockets at the Kennedy Space Center in 2018; it will employ 330 people.
In his 2015 public announcement of the project, Bezos said, “We’re not just launching here, we’re building here. Our ultimate vision is millions of people living and working in space.”
Blue Origin isn’t the only space agency benefiting from Florida’s announced budget: $19.5 million has also been budgeted for “operations and job creation funding for Space Florida,” which is a public agency inside the state’s Department of Transportation that deals with Cape Canaveral’s local space industry. Discuss in the BE-4 forum at 3DPB.com.
Subscribe to Our Email Newsletter
Stay up-to-date on all the latest news from the 3D printing industry and receive information and offers from third party vendors.
Print Services
Upload your 3D Models and get them printed quickly and efficiently.
You May Also Like
The Market and Industry Potential of Multi-Material 3D and 4D Printing in Additive Electronics
Additive manufacturing leverages computer-based software to create components for products by depositing either dielectric or conductive materials, layer by layer, into different geometric shapes. Since its birth in the 1980s,...
3DPOD 262: Bio-inspired Design for AM with Dhruv Bhate, Arizona State University
Dhruv Bhate is an associate professor at Arizona State University. There, he looks at structures, materials, and design. Previously, he worked at PADT as well as in the semiconductor and...
3DPOD 261: Tooling and Cooling for AM with Jason Murphy, NXC MFG
Jason Murphy´s NXC MFG (Next Chapter Manufacturing) is not a generalist service; instead, the company specializes in making tooling. Using LPBF and binder jet, the company produces some of the...
3DPOD 260: John Hart on VulcanForms, MIT, Desktop Metal and More
John Hart is a Professor at MIT; he´s also the director of the Laboratory for Manufacturing and Productivity as well as the director of the Center for Advanced Production Technologies....