biotINK: Student Team Creates Scaffold-Free Bioprinting Technology with a Hacked Ultimaker 3D Printer
3D printed, transplantable, functional human organs are getting closer and closer to becoming a reality, as unbelievable as that seems. While bioprinting technology hasn’t quite gotten to the point of being able to actually 3D print a kidney or liver and implant it into a living human being, it’s only a matter of time as multiple universities, biotechnology companies, and research institutions race to be the first to do so. It’s a fascinating race to watch, not just for the obvious reasons, but because everyone’s technology is a little bit different.
Most 3D printed tissue is created by depositing cells onto a scaffold, where they ideally grow into layers of living tissue to be used for research, pharmacological testing, or, ultimately, regenerative medicine. It’s an incredibly tricky process that often fails due to a variety of reasons: the scaffold is too soft and collapses, it degrades too quickly, or it damages or kills the delicate cells. The scaffold also needs to be removed somehow once the tissue has matured, or else to biodegrade safely on its own.
Scaffold-free bioprinting is a goal that many researchers have their eyes on, but most bioprinting materials, or bio-inks, aren’t strong enough to hold their structures without support. A team formed from students at Ludwig-Maximilian University of Munich and the Technical University of Munich, however, has developed what they hope will be a breakthrough in bioprinting. Team biotINK, formed for the International Genetically Engineered Machine Competition (iGEM), didn’t even require special machinery for their biotINK printing process – just a simple Ultimaker 2+ 3D printer.
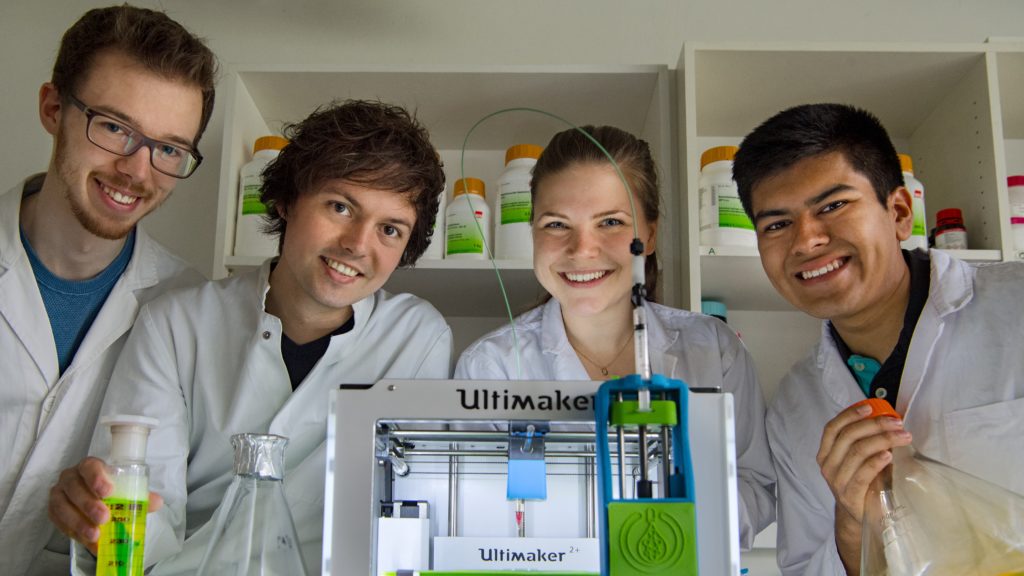
(L to R) Julian Hofmann, Christoph Gruber, Luisa Krumwiede and Javier Luna Mazari of the biotINK team [Image: Andreas Heddergott]
“We are able to create three-dimensional cellular structures easily, quickly and at low cost by immediately cross-linking cells into a protein-cell-matrix upon printing,” the biotINK team explains. “The interactions between cells with each other and the protein matrix are hereby mediated by the strongest non-covalent interaction found in nature – the biotin-streptavidin interaction. By using a two-component system of genetically engineered cells and proteins, we create a kind of molecular superglue that allows precise positioning of cells via bioprinting while locking them in position, allowing the formation of three-dimensional intercellular contacts and physiological microenvironments.”
The idea is for the streptavidin and biotin to polymerize and form a 3D cellular structure without the need for a scaffold of any kind. Eliminating the scaffold, not to mention being able to use a standard desktop printer to extrude the material, could make 3D bioprinting dramatically less expensive than it is now, as well as faster and simpler.
Of course, no form of 3D bioprinting is exactly simple, but the students have carried out a number of experiments with their Ultimaker-turned-bioprinter and biotin/streptavidin ink, and have gotten some very promising results. One discovery they made was that the viability of cells printed with their technology was close to 100%, as opposed to about 85% with standard inkjet bioprinters and 40-80% with microextrusion bioprinters.After the iGEM competition, which culminates today in a massive showcase of the work of over 300 teams, the biotINK team hopes to meet with investors to discuss a possible new business venture. Armed with a functional prototype and a business plan, the team believes that they could make a real impact on the pharmaceutical industry. Discuss in the biotINK forum at 3DPB.com.
Updated to add: at the iGEM competition, the team won awards for Best Manufacturing and Best Software Tool, and was the Overgrad Grand Prize Winner, as reported on the project’s Twitter page.
Subscribe to Our Email Newsletter
Stay up-to-date on all the latest news from the 3D printing industry and receive information and offers from third party vendors.
Print Services
Upload your 3D Models and get them printed quickly and efficiently.
You May Also Like
Making Space: Stratasys Global Director of Aerospace & Defense Conrad Smith Discusses the Space Supply Chain Council
Of all the many verticals that have been significant additive manufacturing (AM) adopters, few have been more deeply influenced by the incorporation of AM into their workflows than the space...
EOS in India: AM’s Rising Star
EOS is doubling down on India. With a growing base of aerospace startups, new government policies, and a massive engineering workforce, India is quickly becoming one of the most important...
PostProcess CEO on Why the “Dirty Little Secret” of 3D Printing Can’t Be Ignored Anymore
If you’ve ever peeked behind the scenes of a 3D printing lab, you might have caught a glimpse of the post-processing room; maybe it’s messy, maybe hidden behind a mysterious...
Stratasys & Automation Intelligence Open North American Tooling Center in Flint
Stratasys has opened the North American Stratasys Tooling Center (NASTC) in Flint, Michigan, together with automation integrator and software firm Automation Intelligence. Stratasys wants the new center to help reduce...