Swanson School of Engineering & Aerotech Partner to Refine Metal Additive Manufacturing with Fast Computational Modeling
3D printing, now available to anyone who is able save up at least a few hundred bucks and enjoy a minor learning curve, has indeed begun to infiltrate the mainstream. And while printing from the desktop can engage us all for hours, allowing us to make any number of items, from basic jewelry to complex car transmissions and even jet engines, for those using the technology in serious lab and industrial settings, all that magic is sometimes accompanied by incredible challenge and plenty of time given over to trial and error—especially in manufacturing with metal to produce complex parts. That level of difficulty sometimes arising is also part of what keeps so many scientists and engineers completely engaged, whether it be in the fabrication and optimization of titanium spinal implants or luxury car parts, with some of the strongest innovators of our time working diligently to make strides for manufacturing—and also, mankind. But let’s face it, while learning from our mistakes is great, no one enjoys wasting time.
Some of the problems that need to be dealt with in this still fledgling technology are basic issues dealing with hardware, software, and the fabrication of complex structures that offer great potential when perfected. We’ve gotten this far, but now it’s time to do some refining to move forward with further success, and as 3D printing in metal becomes a crucial factor for numerous progressive industries, the area is receiving considerable attention.
Now the University of Pittsburgh’s Swanson School of Engineering and Pittsburgh’s Aerotech, Inc. are coming together, charged with the task of creating new, fast computational methods for better additive manufacturing. Their collaboration was made possible thanks to a recently received $350,000 grant from the National Science Foundation, earmarked for solving problems that will mitigate distortion and stress.
The proposal for this project was outlined completely in ‘Novel Computational Approaches to Address Key Design Optimization Issues for Metal Additive Manufacturing,’ intended to be a three-year Grant Opportunities for Academic Liaison with Industry grant offered by the Division of Civil, Mechanical and Manufacturing Innovation (acting as an extension of previous funding from the Research for Advanced Manufacturing in Pennsylvania program).
“This Grant Opportunity for Academic Liaison with Industry (GOALI) research project aims at establishing a robust topology optimization technology capable of accounting for residual distortion, residual stress, and post-machining requirements for additive manufactured (AM) components,” states the proposal. “The technology developed will significantly shorten the design phase during new AM product development, which will potentially lead to wider adoption of AM by the manufacturing base in the US.”
“The first approach is an ultra-fast computational method based on the inherent strain theory for predicting residual stress and distortion in an AM part. The second approach is a level set feature-based topology optimization method capable of generating designs with both freeform surfaces and machining-friendly surfaces.”
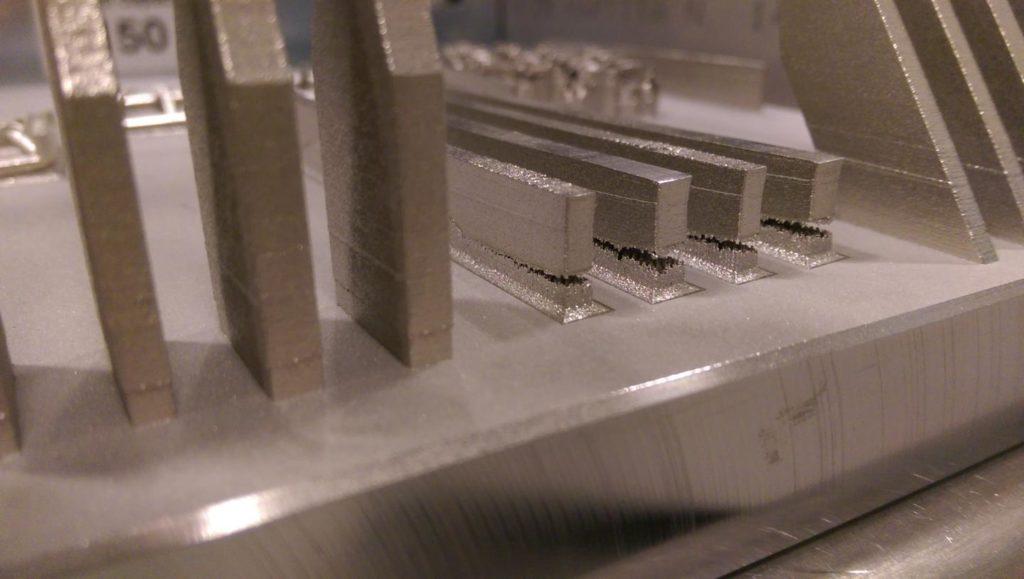
Here, stress buildup shows the collapse of four metal bars created through additive manufacturing. [Photo Credit: Albert To / University of Pittsburgh’s Swanson School of Engineering]
“The ability to create geometrically complex shapes through additive manufacturing is both a tremendous benefit and a significant challenge,” Dr. To said. “Optimizing the design to compensate for residual distortion, residual stress, and post-machining requirements can take days or even months for these parts.”
As they work to create greater speed as well as better quality in the AM industry, Dr. To and his research team are making a thermomechanics model to help serve as a predictor of the noted issues in parts. Once they’ve completed that phase, the group plans to set to work in making a ‘topology optimization method.’ With this they will then endeavor to make up for the complexities and ‘organic nature’ of additively manufactured parts as they are able to print models with both free-form surfaces and machining-friendly surfaces. Residual stress and distortion should be prevented with their new approach, to be further assessed with the use of ‘real parts and design requirements’ provided by industrial partner Aerotech.
While some of the greatest benefits attributed to 3D printing are both speed and the opportunity to create complex, high quality prototypes and components, the processes need to be better, and obviously that begins in the lab.
“…the tools developed through this collaboration will allow us to produce the complex parts enabled by additive manufacturing with a minimum of trial-and-error and rework,” said Stephen Ludwick of Aerotech. “This in turn allows us to design stiff and lightweight components in our high-speed motion systems which are also used by other companies engaged in advanced manufacturing.”
Aerotech, founded in 1970, can certainly be considered experts in their field, working for industrial customers, government, and research institutions worldwide. Specializing in motion control and positioning systems, they provide important applications in fields such as electronics manufacturing, military and aerospace, medical devices and life sciences, automotive, photonics, and more. With an emphasis on precision and solutions, for the context of this project they were able to work with the research team in testing new ways to use additive manufacturing that will help them in making new parts, offering better quality for clients around the globe.
“By utilizing advanced mechanic theory, we hope to reduce design optimization of additive manufactured parts to minutes, thereby reducing the time of design life cycle,” Dr. To said. “This would lead to wider adoption of AM by the U.S. manufacturing base and further improve the economic sustainability of the additive manufacturing process.”
Discuss further over in the Research Grant to Improve Metal 3D Printing forum at 3DPB.com.
[Source: EurekAlert]Subscribe to Our Email Newsletter
Stay up-to-date on all the latest news from the 3D printing industry and receive information and offers from third party vendors.
Print Services
Upload your 3D Models and get them printed quickly and efficiently.
You May Also Like
The Dental Additive Manufacturing Market Could Nearly Double by 2033, According to AM Research
According to an AM Research report from 2024, the medical device industry, specifically in dentistry, prosthetics, and audiology, is expected to see significant growth as these segments continue to benefit from...
Heating Up: 3D Systems’ Scott Green Discusses 3D Printing’s Potential in the Data Center Industry
The relentless rise of NVIDIA, the steadily increasing pledges of major private and public investments in national infrastructure projects around the world, and the general cultural obsession with AI have...
AM Research Webinar Explores Continuum’s Sustainable Metal Additive Manufacturing Powders
Metal additive manufacturing (AM) powder supplier Continuum Powders is working to develop solutions that empower industries to reduce waste and optimize their resources. An independent life cycle assessment (LCA) of...
3D Printed Footwear Startup Koobz Lands $7.2M in Seed Round
California-based Koobz is focused on reshoring the U.S. footwear supply chain with advanced manufacturing processes, including 3D printing. The startup just announced that it has added $6 million to its...