The Dream of Eliminating Post-Processing is Finally a Reality: Introducing the Rize One Industrial Desktop 3D Printer
Case study after case study shows industrial 3D printing’s ability to make manufacturing faster, cut costs, and reduce material usage. It’s easy to believe, hearing the stories, that the technology is nothing short of magical: a machine spits out a perfect, shiny, ready-to use part, seemingly out of thin air. There may even be a puff of smoke involved. (Note to new users: your 3D printer should not be emitting puffs of smoke. If it is, unplug and call the repair guy.) In reality, there’s still a lot of work involved in getting a 3D printed part ready for use.
Many a manufacturer may consider post-processing the bane of their existence. In industrial 3D printing, most parts require supports, and removing them can take longer than the actual print job. Sanding the part, filing the part, immersing the part in noxious chemicals – it’s messy, tedious, and time-consuming, not to mention stressful, especially when a part is needed right now. Most manufacturers are resigned to it, however, as the trade-off for the other benefits 3D printing offers.
Now, however, there may no longer be a need for that trade-off at all. Woburn, Massachusetts-based Rize Inc. has unveiled a brand new industrial-grade desktop 3D printer that, they say, completely eliminates the need for post-processing. The Rize One, which will be commercially available later this year, promises to slash costs, reduce turnaround time by 50%, eliminate mess and excess materials, and take industrial 3D printing from the lab to the office.
“Post-processing has been 3D printing’s dirty little secret, as engineers and additive manufacturing lab managers wrestled with the reality that post-processing parts after 3D printing often doubled the total process time; added substantial costs; and prevented 3D printers from the desktop,” said Frank Marangell, President and CEO of Rize. “Rize One eliminates those sacrifices, opening a world of possibilities for designers and engineers to deliver prototypes and on-demand finished parts much faster and with stronger material – than before. Whether 3D printing helps you go to market, or create a market, Rize will fundamentally alter your production cycle.”
Rize has been quietly developing the printer for two years, impressively staying below the radar until now. While a new company, Rize is made up of a team of 3D printing veterans with solid expertise, experience, and over 20 patents among them. Marangell was the president of Objet North America prior to their merger with Stratasys. The company was founded in 2012 by Eugene Giller, who developed inkjet 3D printing technology at Z Corporation (now 3D Systems), and Leonid Raiz, who invented nothing less than 3D CAD software and founded Revit, now Autodesk.
“With its experience and pedigree in the industry, Rize has put together a dream team,” said Nilanjana Bhowmik, Partner at Longworth Venture Partners, which is backing the Rize One with a significant amount of seed capital. “This innovation will make a significant impact on the 3D printing industry.”
The key to the Rize One is the company’s patented Augmented Polymer Deposition (APD) technology and Rizium One filament, a watertight engineering- and medical-grade thermoplastic that, according to the team, creates parts that are twice as strong as parts printed with similar technologies. During the printing process (which produces zero harmful emissions), a repelling ink called Release One is jetted between the part and its support structures, so that once the part comes off the print platform, the user can simply snap off the supports as easily as taking apart Legos. The printer also features a “marking ink” that allows for text or images to be printed on the parts.
General specifications include:
- Printer size: 543 x 915 x 150 mm (21.4 x 36 x 25.4 in)
- Build size: 300 x 200 x 150 mm (12 x 8 x 6 in)
- Layer thickness: 0.25mm (250 microns)
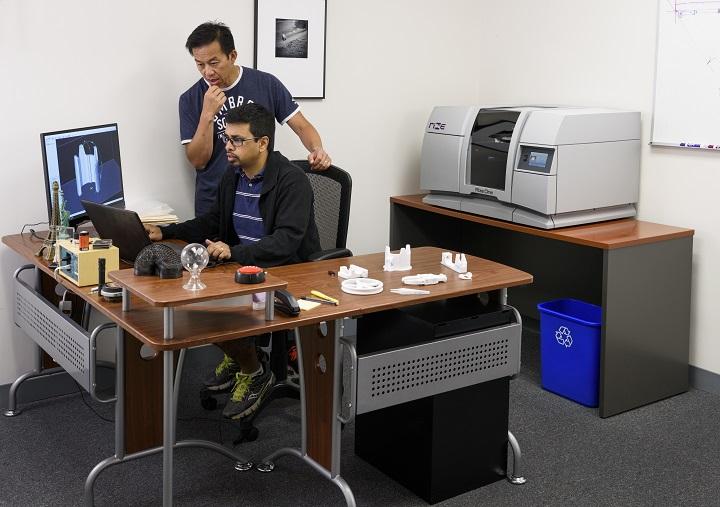
The printer, which is being backed with $4 million in seed funding by Longworth Venture Partners and SB Capital, is currently entering beta with Reebok.
“We run our 3D printers 24/7 to create the parts central to Reebok’s innovation, and, unfortunately, post processing has been a necessary but laborious and time-consuming process,” said Gary Rabinovitz, Reebok’s Additive Manufacturing Lab Manager. “An easy-to-use, zero post-processing 3D printer like Rize would dramatically improve workflow, enabling us to deliver parts as much as 50% faster than similar technologies, while reducing the cost of labor, materials and equipment.”
Discuss your thoughts on this new technology in the Rize One 3D Printer forum over at 3DPB.com.
Learn more about the Rize One below:
https://youtu.be/1F7pGjIKnqM
[Images: Jon Chomitz Photography via Rize Inc.]
Subscribe to Our Email Newsletter
Stay up-to-date on all the latest news from the 3D printing industry and receive information and offers from third party vendors.
Print Services
Upload your 3D Models and get them printed quickly and efficiently.
You May Also Like
Johns Hopkins University Researchers Develop HyFAM Technology
Two scientists from Johns Hopkins University, Nathan C. Brown and Jochen Mueller, have developed a hybrid manufacturing technology they call HyFam, or Hybrid Formative Additive Manufacturing. Their work on this technology...
3D Printing G-Code Gets an Upgrade: T-Code
Good old G-Code still manages many 3D printers, great and small. Just like the STL, it’s a standard that enables collaboration while also holding the additive manufacturing (AM) industry back....
AM Rewind: The Biggest News and Trends of 2024
After a sluggish 2023, driven by persistent inflation and geopolitical tensions, 2024 has seen some recovery. Economic growth climbed from about 2.8 percent in 2023 to a modest 3.2 percent...
Metal Wire 3D Printer OEM ValCUN Announces Plans for 2025 Expansion
ValCUN, a Belgian original equipment manufacturer (OEM) of wire-based metal additive manufacturing (AM) hardware, has announced that the company has entered the next phase of its growth trajectory, making key...