Although learning to knit has always been one of my aspirations, thus far I’ve been a well-known failure in this area amongst my artsy-craftsy friends, who have given up on offering support and just gone silent on the subject. Perhaps I’m just not ready to settle down by the fire and spend hours hunched over yarn (or a machine), but I have numerous friends who make this look awfully enticing—especially when they bound out of the car to winter events sporting matching hats and mittens with their kids, perfectly made in the most perfect colors. While I suspect the idea of wearing matching winter garb with immediate family members would be met with abject horror, it hasn’t seemed to be in the cards anytime soon. The dog spent a day playing in my knitting yarn and then claimed it as a giant dog bed, while my son ran off with the needles, using them as drumming sticks. I’m off the ‘hook’ for now!
That may change eventually though as Disney Research comes to the rescue with automated knitting via industrial 3D printing for apparel and pieces like plush toys. This isn’t a new concept in terms of automation, and we’ve even reporting on other innovations from 3D printed knitting machines to actually 3D scanned and 3D printed knitted designs. While this technology offers a host of benefits in terms of being able to create in a self-sustained fashion, affordably, and most of all—offering ease in customization—these features haven’t really been applicable to knitting, as helpful as that might be. And as the researchers point out, automated knitting needs refinement on both the industrial and domestic front.
Now, the researchers are working to make this an easier process, as well as allowing for knitted items generally considered to be more high level to be made using simple instructions. The team refers to this as a compiler, and it works according to a transfer planning algorithm which is able to perform stitching according to position and length, as well as using shape primitives to make them into items that can be customized. The researchers outline their new machine and exactly what it does in ‘A Compiler for 3D Knitting Machine,’ by James McCann, Lea Albaugh, Vidya Narayanan, April Grow, Wojciech Matusik, Jen Mankoff, and Jessica Hodgins. The researchers are affiliated with Disney Research, UC Santa Cruz, Massachusetts Institute of Technology (MIT), and/or Carnegie Mellon University.
The basic tasks an industrial knitting machine needs to perform are: knit, tuck, split, and transfer. Their compiler is able to accept needle instructions for two primitives: tubes and sheets, and a basic user interface helps with editing information. The user is able to adjust the scheduling of a design to make it knittable, and then the compiler translates everything into instructions.
“At the core of our compiler is a heuristic transfer planning algorithm for knit cycles, which we prove is both sound and complete,” state the researchers in their paper. “This algorithm enables the translation of high-level shaping and scheduling operations into needle-level operations.”
The idea is to move away from traditional knitting machines which allow only for a ‘fixed palette’ of objects with customization rarely available in any form. Motivated to create more flexibility in automated knitting, the research team has created a way for their users not only to ‘create at a high level,’ but also to change:
- Knitting order
- Needle location
- Shape
- Scale
The user is also able to discern which needles are being used in case they need to adjust—all possible without interrupting the shape they are currently working with.
The research team states that the main benefits of using their compiler are:
- High-level schedule and structure manipulation
- Knitting assembly language that formalizes low-level operations
- A compiler with transfer-planning heuristic for cycles
Numerous customizations and edits can be made, for example: stitch widths can be decreased or widths can be increased. Splits can be used instead of tucks, and shapes can be changed with short rows when making items like socks, and rounding out the heels.
“The focus of our compiler is to make it easier to create knit structures; however, many knit objects also use various combinations of stitches to create interesting surface textures,” state the researchers.
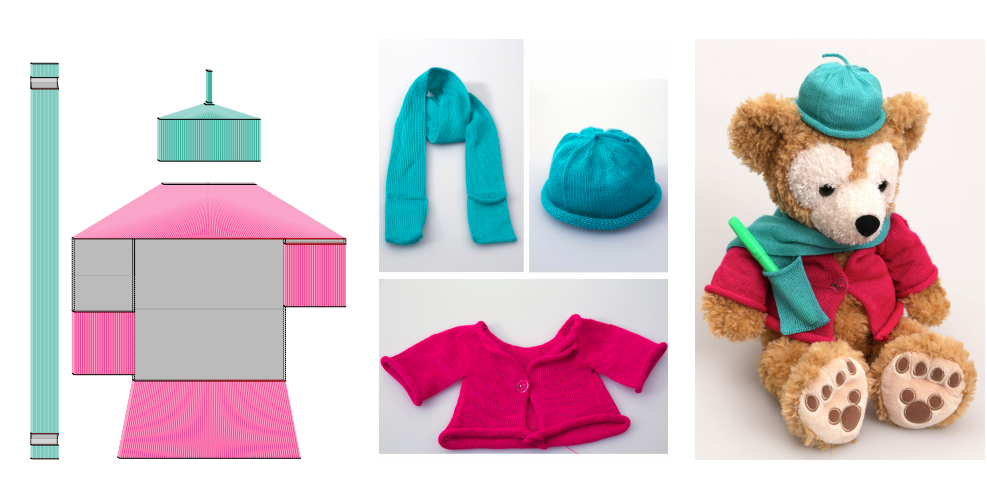
“Partially-knit rows can be used to bend shapes, as in the heel of this sock, and create bulges, as in this whimsical hat.”
As they continue this work, the team plans to work on support surface texturing with additional local programs, as well as focusing on creating ‘optimization passes’ for the compiler that will facilitate creativity in making objects on home-knitting machines too, which they describe as ‘severely restricted machines’ that have not been updated in decades.
“We believe that 3D machine knitting should join 3D printing in the pantheon of end-user-accessible additive fabrication, and that getting it there will require new tools, algorithms, and data exchange formats, of which our compiler, transfer planning algorithm, and knitting assembly languages are first examples,” state the researchers in conclusion.
Disney Research clearly recognizes the limitations that currently need to be overcome in automated knitting as they address more industrial needs. Hopefully interest will continue in this vein as we watch them do their magic for novice users like myself as well, allowing for the more ‘knitting challenged’ to have a chance at easily making personalized Christmas sweaters and matching socks for the whole family to enjoy (wink!). What do you think about 3D Printed Knitting? Let’s discuss this topic over in the 3D Knitting Compiler forum at 3DPB.com.
[Source: Inverse / Images: Disney Research/Gipy, Disney Research Hub]Subscribe to Our Email Newsletter
Stay up-to-date on all the latest news from the 3D printing industry and receive information and offers from third party vendors.
Print Services
Upload your 3D Models and get them printed quickly and efficiently.
You May Also Like
Making Space: Stratasys Global Director of Aerospace & Defense Conrad Smith Discusses the Space Supply Chain Council
Of all the many verticals that have been significant additive manufacturing (AM) adopters, few have been more deeply influenced by the incorporation of AM into their workflows than the space...
EOS in India: AM’s Rising Star
EOS is doubling down on India. With a growing base of aerospace startups, new government policies, and a massive engineering workforce, India is quickly becoming one of the most important...
PostProcess CEO on Why the “Dirty Little Secret” of 3D Printing Can’t Be Ignored Anymore
If you’ve ever peeked behind the scenes of a 3D printing lab, you might have caught a glimpse of the post-processing room; maybe it’s messy, maybe hidden behind a mysterious...
Stratasys & Automation Intelligence Open North American Tooling Center in Flint
Stratasys has opened the North American Stratasys Tooling Center (NASTC) in Flint, Michigan, together with automation integrator and software firm Automation Intelligence. Stratasys wants the new center to help reduce...