In the past few years we have seen 3D printing used to create some amazing things that most of us probably couldn’t have dreamed of happening in our lifetime. The technology has been used to 3D print cars, entire houses, food, custom medications, consumer products and soon they will even be 3D printing living tissue. What is truly amazing about 3D printing is the vast applications that it has been used to create, and each one of them required its own technology and research to perfect and get right. What is even more incredible is the sheer number of uses for 3D printing that are still being developed and perfected.
While we’ve seen plenty of 3D printed clothing, for the most part there have been little to no practical applications yet. That doesn’t mean that there hasn’t been a ton of amazing research into wearable 3D printed clothing and fabrics, but there are still some kinks to work out of the process. Primarily 3D printed fabrics and textiles are printed using a selective laser sintering process because it offers the highest level of detail needed to produce movable materials that can be turned into clothing. Unfortunately the detail still isn’t fine enough to make practical clothing, but the research has produced some innovative and smart geometries that could eventually be scaled down into lightweight and wearable 3D printed fabrics.
A new joint research project from the UK’s Loughborough University and global textile and garment manufacturer Yeh Group is looking to take 3D printed textiles from concept to wearable. Product and Industrial Design Senior Lecturer Dr. Guy Bingham is the head of the new project and is hoping their research can ultimately change the way that we design, manufacture and wear clothing. The 18-month project is called 3D Fashion and the goal is to produce finished, ready-to-wear clothing directly from raw materials in a single manufacturing operation. The ultimate goal is to create a 3D printing process that can be commercialized and used to manufacture customized clothing using polymer materials.
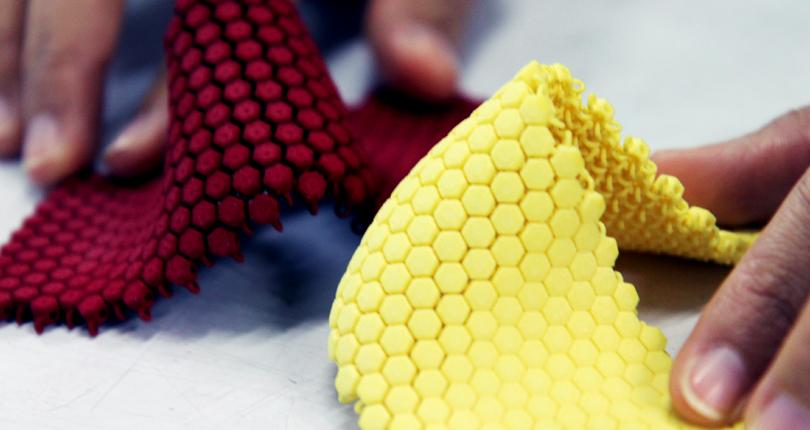
3D printed textiles can be printed in any color, which virtually eliminates the pollution and waste caused by traditional dyeing.
“[3D printing] allows us as designers to innovate faster and create personalised, ready-to-wear fashion in a digital world with no geometrical constraints and almost zero waste material. We envisage that with further development of the technology, we could 3D print a garment within 24 hours. Printing clothes using AM will revolutionise the fashion industry worldwide by opening up digital manufacturing to the masses via online retail, bringing a much needed update to 19th century techniques and processes. This modern approach to clothing production helps meet the growing demand for personalised apparel and footwear which through 3D printing can be produced in a sustainable and ethical way,” said Dr Bingham.
Traditional clothing manufacturing is incredibly wasteful and environmentally damaging. China still produces most of the world’s textiles, and in 2010 alone it processed more than 41 millions tons of fibers. Unfortunately, that year they also produced three billions tons of air pollution, millions of tons of wasted fabric material and each individual mill used an average of 200 tons of water for each ton of fabric that was dyed, producing more than two and a half billion tons of waste water. But 3D printing can virtually eliminate all of that pollution, while also encouraging more localized clothing manufacturing and production.
“3D Fashion supports the Yeh Group vision of direct polymer to garment manufacture. The Yeh Group is always striving to cut out unnecessary waste and resource use, and support the industry’s goals of faster to market, creating a manufacturing technology that brands and retailers can install closer to their customers. This is all with no compromise to performance,” explained Yeh Group Managing Director David Yeh.
Not only can 3D printed clothing dramatically reduce waste, pollution, labor costs and CO2 emissions, but it can also be used to produce completely personalized garments, without adding any additional costs to the process. Because it doesn’t cost any more to 3D print objects with varying geometries, new clothing manufacturers could use modern, 3D scanning technology to create customized clothing that is made specifically for the wearers body. You can read more about the 3D Fashion project here. Do you think 3D Printed Clothing will be popular in the future? Discuss in the 3D Printed Textiles & Clothes forum over at 3DPB.com.
[Source/Images: 3D Fashion / Source: The Engineer]
Here is a video about the 3D Fashion Project:
Subscribe to Our Email Newsletter
Stay up-to-date on all the latest news from the 3D printing industry and receive information and offers from third party vendors.
Print Services
Upload your 3D Models and get them printed quickly and efficiently.
You May Also Like
Making 3D Printing Personal: How Faraz Faruqi Is Rethinking Digital Design at MIT CSAIL
What if your 3D printer could think more like an intelligent assistant, able to reason through a design idea, ask questions, and deliver something that works exactly the way the...
Reinventing Reindustrialization: Why NAVWAR Project Manager Spencer Koroly Invented a Made-in-America 3D Printer
It has become virtually impossible to regularly follow additive manufacturing (AM) industry news and not stumble across the term “defense industrial base” (DIB), a concept encompassing all the many diverse...
Heating Up: 3D Systems’ Scott Green Discusses 3D Printing’s Potential in the Data Center Industry
The relentless rise of NVIDIA, the steadily increasing pledges of major private and public investments in national infrastructure projects around the world, and the general cultural obsession with AI have...
Formlabs Teams Up with DMG MORI in Japan
In late June, Nick Graham, Chief Revenue Officer at Formlabs, announced on LinkedIn that the company had partnered with DMG MORI, one of the world’s leading machine tool companies, to...