New Technology Like 3D Printing Emerges—Companies Collaborate, Integrate Traditional With Cutting Edge
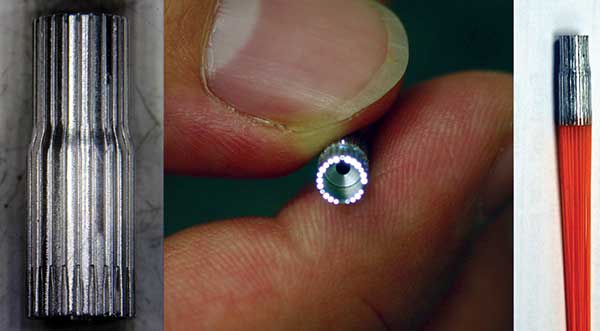
Micromachined fiber guide with optical fibers (left). Completed fiber guide with lighting fiber ends (right). [Courtesy of Kugler GmbH.]
- Spacecraft components
- Next-generation displays and electronic devices to low-cost photovoltaic cells
- Defense and security technologies
Offering significant impact in terms of many of the items being used today for very important uses, a wide range of different technologies are used to achieve the final form of items which for most of their purposes must be perfect in function, and operate at the maximum level of performance. Photonics and laser machining are prevalent, but it’s important today to note how many new processes are considered to be alternatives, emerging as very important for the future, or being used in collaborative methods to achieve design goals. It’s easy to understand that 3D technology and 3D printing would fit in here, along with many other options—and we often see the technology mixed with other very traditional processes.
What’s happening today in technology and machining practices is quite interesting and may cause not only a shift in how technology is used to make products, but it may cause quite a shift in business too: companies with relevant technologies who used to engage in the dog-eat-dog world of competition are now coming forward more and more often to collaborate.
For instance, while 3D printing is offering an enormous amount of innovation to the medical industry, from 3D printed stents offering hope to cancer patients to items like cardiovascular models that are 3D printed and listed as Class 1 medical devices, tradition still prevails, while seemingly calling in for help more and more from the ever evolving cutting edge.
Micromachining—often with the use of the laser–is seen as important to applications in the medical field for items like stents, cutting holes and making other features in items like catheters and fluid delivery devices, as well as making permanent counterfeit-proof marks for plastic products like syringes or vials.
“Laser micromachining offers the potential for removal or transformation of material with incredible spatial selectivity and three-dimensional flexibility. It is therefore a superior tool for creating small features, and features and edges with smooth surfaces,” said Joris van Nunen, product line manager for Industrial Ultrafast Lasers at Coherent Inc. “It’s also useful for processing very thin materials, and materials that are delicate or thermally sensitive.”
Cool cutting is used with a laser or diamond mill and is found helpful by industries such as microelectronics and solar, as they achieve product goals with cold or athermal ablation. Industrial ultrafast lasers work even better, while femtosecond lasers are known to deliver the best quality available in terms of edges and overall surface.
“At first most of these operated in the picosecond regime, but today laser manufacturers now also offer femtosecond performance in industrial-grade platforms,” said Frank Gaebler, marketing director for materials processing at Coherent Inc. “The use of ultrafast laser pulses enables cutting of novel hole shapes and modalities in catheters, for example, and allows marking inside glass products, such as syringe bodies, with no impact on the surface, material integrity or the contents.”
While this is all extremely helpful, it’s still often very expensive as a technology and both reliability and affordability of the lasers are a serious consideration. It’s hoped by those within the industry that as the technology becomes more mainstream in use that the prices will come down.
Also crucial to the medical industry are optical molds, lenses and fibers. These are today still produced through as milling and diamond turning—with no lasers involved.
“The most important application of precision manufacturing by high precision milling and micromilling in medical technology consists in the manufacture of mold inserts,” said Klaus Baier, R&D project manager at Kugler.
Here too, is another area where 3D printing is emerging as it can be used to great benefit in making complex molds in smaller batch runs for many different industries. In this aspect, micromilling processes are popular though for large production projects making items such as:
- Lab-on-a-chip and microfluidic systems
- Multiwell and microplates
- Cell and tissue culture flasks
- Disposable products for blood, urine and specimen collections
As experts look toward the next new wave of innovations in medicine, they point out microsystems as playing a major role for diagnostics and personalized healthcare. While one would think this should be extremely personalized already, 3D printing will play—and is already playing—a role in offering patient-specific surgical models allowing for procedures not previously possible, as well as a multitude of implants and drug delivery systems that are already in testing. What will ultimately develop from these new technologies will be a result of ultra-precise manufacturing.
And while 3D printing offers a long list of benefits, many still don’t see it as competing with traditional processes—yet. If doesn’t take much experience with 3D printing to understand that speed can in some cases still be a major issue, and often it just is not cost-effective, despite all the benefits once you have an operation running—or are able to look at other exceptional cases.
“At the moment the methods of 3D printing do not yet yield the dimensional accuracy needed for all the parts described above,” Kugler’s Baier said. “Furthermore not all the biocompatible materials are available for 3D printing.”
While many are very excited about 3D printing and ready to eschew everything traditional, it does seem that many are having great success in mixing both traditional and super high-tech innovation. The Coherent team supports the idea of integrating both traditional and new technology, embracing the potential of 3D printing for the future, especially in areas affecting medical cases, similar to ones we often follow where devices like titanium hip implants or 3D printed spinal implants are changing the face of medical treatment for patients–and often seriously changing the quality of life for patients; for example, we followed the case of an Ethiopian patient who received a titanium mandible implant–giving him back his jaw.
“3D scanning followed by 3D printing with a fiber laser enables creation of a perfect replica replacement that is unique and patient-specific,” van Nunen said. “This is a great example of how precision laser machining can improve, rather than simply replace, some existing manufacturing methods.”
With so many new trends and technologies being created and even sometimes within the same facilities, consumers and medical patients have many more options open to them today, offering better quality of life all around. In the case of doctors, they also have better tools for practicing, training others, exploring procedures, and being able to convey information to patients with the use of 3D models.
While 3D printing is certainly a boon to many industries, it’s not quite time to throw out traditional processes—and may never be. Discuss in the 3D Printing & Traditional Processes forum over at 3DPB.com.
[Source: Euro Photonics]
Subscribe to Our Email Newsletter
Stay up-to-date on all the latest news from the 3D printing industry and receive information and offers from third party vendors.
Print Services
Upload your 3D Models and get them printed quickly and efficiently.
You May Also Like
Reinventing Reindustrialization: Why NAVWAR Project Manager Spencer Koroly Invented a Made-in-America 3D Printer
It has become virtually impossible to regularly follow additive manufacturing (AM) industry news and not stumble across the term “defense industrial base” (DIB), a concept encompassing all the many diverse...
Inside The Barnes Global Advisors’ Vision for a Stronger AM Ecosystem
As additive manufacturing (AM) continues to revolutionize the industrial landscape, Pittsburgh-based consultancy The Barnes Global Advisors (TBGA) is helping shape what that future looks like. As the largest independent AM...
Ruggedized: How USMC Innovation Officer Matt Pine Navigates 3D Printing in the Military
Disclaimer: Matt Pine’s views are not the views of the Department of Defense nor the U.S. Marine Corps Throughout this decade thus far, the military’s adoption of additive manufacturing (AM)...
U.S. Congress Calls Out 3D Printing in Proposal for Commercial Reserve Manufacturing Network
Last week, the U.S. House of Representatives’ Appropriations Committee moved the FY 2026 defense bill forward to the House floor. Included in the legislation is a $131 million proposal for...