SAIT Polytechnic Design Team Reverse Engineers & 3D Prints Daft Punk Helmet in Teachable Moments Program
Luckily for 3D printing enthusiasts of late, the Daft Punk duo graduated from wearing trash bags on their heads quite some time ago. These French Grammy winning musicians have made themselves known not only by their now ubiquitous dance tunes but also by their futuristic head gear, which lately seems to be quite inspiring at the 3D printer.
Meant not only just to hide their faces so that they aren’t constantly barraged by fans, the French duo, made up of Thomas Bangalter and Guy-Manuel de Homem-Christo, also employ the helmets and overall robot costumes as a somewhat philosophical way to mix fictional and real personas.
Now, taking a look at the Daft Punk helmets and the reality of how difficult they might be to fabricate, the Design, Fabrication and Testing research team at SAIT Polytechnic tried their hand at reverse engineering the headpiece worn by Guy-Manuel. Giving cred to the Daft Punk design team–they found that this certainly was no easy feat–over a two-month stretch.
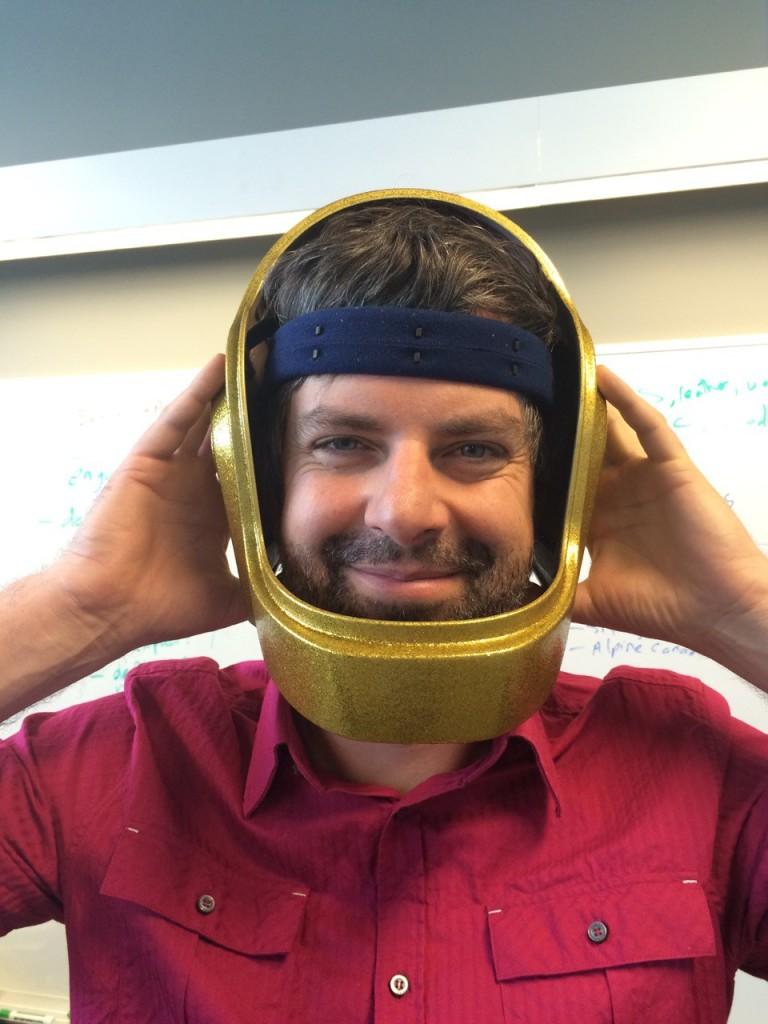
Researcher Emerson Burns trying on the helmet after it was painted. (Photo credit: SAIT Polytechnic)
While producing pop star paraphernalia was certainly part of the end goal, this project was meant to enhance the team’s skill set in terms of 3D printing, rapid prototyping, and surface modeling. And that it did. They had to be very resourceful just to get the correct initial design going, duly challenged from square one.
“The helmet was difficult to model. When we reverse engineer something, we usually have a physical part to work from. Since we didn’t have a helmet, we looked on the Internet for high-resolution pictures and videos,” explained researcher Emerson Burns. “We imported the best front and side photos into SOLIDWORKS and built our model from there, referencing other photos for accuracy. Once complete, we broke the model into pieces for 3D printing.”
If you compare the visors between Thomas Bangalter and Guy-Manuel, you will see that the team definitely chose the more difficult visor to create, as it encompasses so much more of the helmet with open space. The design team was forced to get extra creative in that area too in terms of other materials, as they were using ABS for the 3D printing mold. The visor, however, had to be vacuumed formed, which meant they needed to heat, stretch, and use a vacuum on the plastic.
“We initially wanted to use 2-mm Polycarbonate, but the forming temperatures were too high. We ended up using 1.5-mm PETG (pop bottle) plastic. It still had to be heated to 135 degrees celsius, more than three times the maximum recommended working temperature of the ABS plastic. If the buck heats above 60 degrees it will start to warp,” explained Burns. “After about six seconds we were in the 60-degree celsius range which prevented warping.”
In dissecting the elements involved in making the helmet, the team found the experience to be ‘invaluable’ and helped their expertise to grow. They did also add some fun extras like LED lights.
“We are now capable of printing tools to manufacture parts that can’t be 3D printed,” said Burns. “Industry clients often ask us to improve on products they already have. This involves taking the product apart, 3D scanning it, rebuilding the product using computer aided design, altering the desired parts and then 3D printing each element for testing.”
This project certainly came from a different angle as compared to another helmet our own Scott Grunewald recently covered from the popular Adafruit team. Known for incredible 3D printing savvy and the ability to jazz up even the most basic of items and gadgets, the Ruiz brothers also chose Guy-Manuel’s helmet with the goal of taking it above and beyond its current state, making it more wearable and adding extra bling with complex, programmable LEDs.
While the folks over at Adafruit may be 3D printing rockstars, we’re counting on teams like those at SAIT Polytechnic and their Applied Research and Innovation Services (ARIS), which works to take on projects uniting the needs of industry with the knowledge and skills of faculty and students to bring innovations closer to market. Discuss this story in the Daft Punk 3D print Forum on 3DPB.com.
ARIS has four research divisions: Environmental Technologies, Sports and Wellness Engineering Technologies, the RFID Application Development Lab and Green Building Technologies. They also work with numerous other teams in research.
Subscribe to Our Email Newsletter
Stay up-to-date on all the latest news from the 3D printing industry and receive information and offers from third party vendors.
Print Services
Upload your 3D Models and get them printed quickly and efficiently.
You May Also Like
Could 3D Printing for Biocomputing Make Wetware Aware?
As an AI arms race consumes ever more electricity, and every ChatGPT search query costs $0.36, the search for new ways of computing has intensified. One answer could be in better...
Bambu Lab Launches Software to Manage 3D Printer Fleets—No Cloud Needed
Bambu Lab has introduced a new software tool, Bambu Farm Manager, designed to help users manage large fleets of 3D printers over a local network, without relying on the cloud....
Consolidation in AM: How 2025 Is Shaping the Industry’s New Normal
The first half of 2025 has been marked by a clear shift in the additive manufacturing (AM) industry. Companies are no longer just focused on developing new tech by themselves....
3D Printing News Briefs, July 2, 2025: Copper Alloys, Defense Manufacturing, & More
We’re starting off with metals in today’s 3D Printing News Briefs, as Farsoon has unveiled a large-scale AM solution for copper alloys, and Meltio used its wire-laser metal solution to...