3D Printed Noses, Ears & Joints May be Coming Soon – New Hydrogel Discovery Points in That Direction
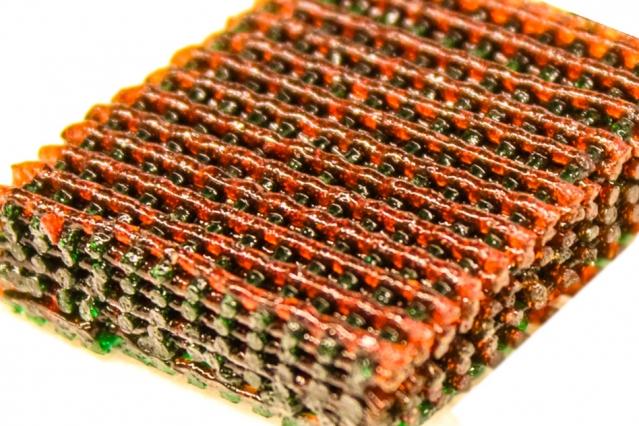
The open lattice of 3D printed material, with materials having different characteristics of strength and flexibility indicated by different colors.
When it come to medical technology, soft robotics and drug delivery systems, hydrogels are well on their way to providing further innovation. Researchers are discovering new technologies, new mixtures, and new chemical processes each and every day. For those of you unfamiliar with what a hydrogel is, it is a soft, wet biocompatible material, defined by water molecules which are encased in rubbery polymer networks that provided it with structure and shape. Typically synthetic hydrogels are usually weak and brittle in nature, but that appears to be about to change.
In a new research report, detailed in the Journal of Advanced Materials, researchers have discover a way of creating hydrogels that are “extremely tough and robust”, while also being compatible with the encapsulation of cells within the structure itself.
So why is this so significant?
Because the materials are so tough and strong, the multitude of potential uses greatly increases. Most significantly, these materials are capable of being 3D printed, meaning that they could conceivably be fabricated in high detail, on a one-to-one basis. These hydrogels would make for the perfect solution to creating actuators for soft robotic systems, as well as drug delivery agents and 3D printable artificial cartilage. Most interesting is the idea of using these materials, to 3D print replacement joints as well as nose and ear cartilage for humans.
“The innovation is really about the material — a new ink for 3-D printing of biocompatible tough hydrogel,” explained Xuanhe Zhao, MIT associate professor of mechanical engineering and one of the co-authors of the paper, titled 3D Printing of Highly Stretchable and Tough Hydrogels into Complex, Cellularized Structures. “Specifically, a composite of two different biopolymers. Each [material] individually is very weak and brittle, but once you put them together, it becomes very tough and strong. It’s like steel-reinforced concrete.”
These hydrogels have properties very similar, yet far superior to real human cartilage. For example, they can be 3D printed in a variety of different shapes, such as pyramids, “twisted bundles”, multilayer meshes, hollow cubes, and more. They can be printed in the shape of a human nose or ear, as well as that of cartilage within human joints. A 3D printed hydrogel pyramid is capable of being compressed almost 99 percent, yet when let go, it will quickly and easily bounce right back to its original shape. At the same time, the material, which has a viscosity that can be easily modified so that it can be printed out of a 3D printer, also can be stretched to five times its original size. It also is much stronger than typical human cartilage, meaning as a substitute it may actually perform better at withstanding the everyday wear and tear that human joints face.
These new hydrogels are capable of being filled with cells, such as stem cells, without any damage being done. The potential is there for plenty of medical applications that we should hopefully see brought to fruition in the years to come.
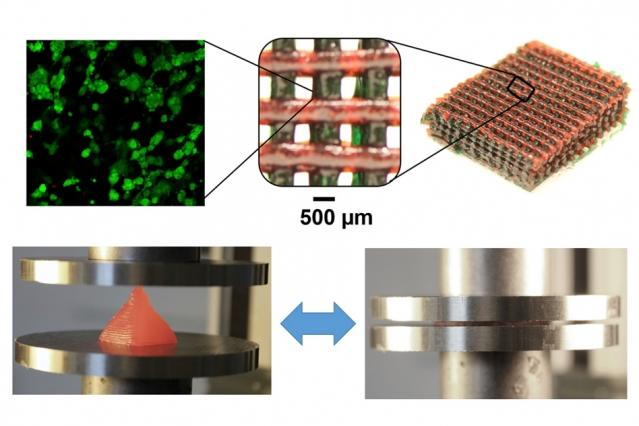
The structure of the hydrogel material is shown at different scales, down to the molecular level (top). Material 3D printed using this method is so flexible that it can be squeezed flat, and then spring back to its full original shape (bottom)
One polymer within the mixture for this 3D printable material, provides for extreme elasticity, while another polymer allows for the dissipation of energy while under deformation without breaking apart like other brittle hydrogels do. To these two polymers, a biocompatible “nanoclay” is added, allowing researchers and scientists to modify the viscosity in order to precisely control the flow of the hydrogel out of a 3D printer’s nozzle.
“This is really beautiful work that demonstrates major advances in the utilization of tough hydrogels,” explains David Mooney, a professor of bioengineering at Harvard University. “This builds off earlier work using other polymer systems, with some of this earlier work done by Dr. Zhao, but the demonstration that one can achieve similar mechanical performance with a common biomedical polymer is a substantial advance. It is also quite exciting that these new tough gels can be used for 3-D printing, as this is new for these gels, to my knowledge.”
Currently researchers are working to perfect the methods of 3D printing this material. The current 3D printer that they have been using is capable of printing in detail down to 500 micrometers, but that will soon improve quite a bit with further innovation.
Will this lead to us seeing 3D printed cartilage replacement within the human body? How about plastic surgeons using the technology to create new noses and ears for their patients? It seems as though, if all goes as planned, this could be a reality sometime soon.
What do you think? Discuss in the 3D Printed Cartilage and Tough Hydrogel forum thread on 3DPB.com. Check out the video of these hydrogels being 3D printed below.
Subscribe to Our Email Newsletter
Stay up-to-date on all the latest news from the 3D printing industry and receive information and offers from third party vendors.
You May Also Like
Profiling a Construction 3D Printing Pioneer: US Army Corps of Engineers’ Megan Kreiger
The world of construction 3D printing is still so new that the true experts can probably be counted on two hands. Among them is Megan Kreiger, Portfolio Manager of Additive...
US Army Corps of Engineers Taps Lincoln Electric & Eaton for Largest 3D Printed US Civil Works Part
The Soo Locks sit on the US-Canadian border, enabling maritime travel between Lake Superior and Lake Huron, from which ships can reach the rest of the Great Lakes. Crafts carrying...
Construction 3D Printing CEO Reflects on Being Female in Construction
Natalie Wadley, CEO of ChangeMaker3D, could hear the words of her daughter sitting next to her resounding in her head. “Mum, MUM, you’ve won!” Wadley had just won the prestigious...
1Print to Commercialize 3D Printed Coastal Resilience Solutions
1Print, a company that specializes in deploying additive construction (AC) for infrastructure projects, has entered an agreement with the University of Miami (UM) to accelerate commercialization of the SEAHIVE shoreline...