Today, Stratasys announced a new collaboration with Worrell. This relationship between a leading 3D printing company and a design and product development firm will provide the right background to speed up work in the field of 3D printed medical device development.
The two biggest difficulties in bringing new medical devices to market come from regulations and high tooling costs. The FDA tends to keep a very close hold on regulations for medical applications, requiring prototypes and proof of efficacy before giving any new product a green light. In addition to stringent watch, costs tend to be high in terms of both dollars and time.
Traditional tooling for new product development is fairly extensive; new molds are made with each iteration of a prototype prior to final form manufacturing. This process requires potentially long development periods and significant material and other tooling costs.
Recently, Worrell was approached to create a new medical device. Thinking it through, they determined that 3D printing would have benefits to all sides. Using Stratasys’ 3D printing technology would enable them to design the requested system at a significantly lower cost and in a much shorter time.
Kai Worrell, Worrell’s CEO, described the process:
“We were recently approached by medical device startup MedTG to design and engineer a dual-flow needleless blood collection system that reduced the need for multiple injections, thereby increasing patient comfort and hospital efficiency. Utilizing 3D printed injection molds to prototype the device, we were able to reduce the costs associated with traditional tooling by approximately 70%, as well as cutting times by 95%.”
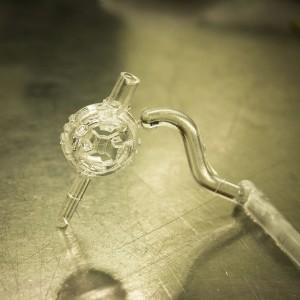
Medical device prototype made from polycarbonate, just as the final device will be, created via 3D printed injection molds
“Using 3D printed injection molds, we are able to create a prototype for a fraction of the cost and in a matter of days compared to the eight-week lead time associated with traditional tooling processes. This revolutionary manufacturing process enabled by Stratasys PolyJet technology is now an integral part of our product development cycle, allowing us to provide better prototypes for care providers, while saving our clients considerable time and money,” continued Mr. Worrell.
Printing up prototypes on the Stratasys Objet500 Connex 3D printer located on their own manufacturing floor, Worrell could keep a close eye on the speedy process. The printer creates injection molding tools and injects the same materials that will ultimately be used in the finished product to produce functional, close-to-final-quality prototypes.
Below is a visual from Stratasys detailing the cost and time savings possible using 3D printed injection molds in prototyping:
What do you think of this new partnership? Discuss in the Stratasys / Worrell Partnership forum thread on 3DPB.com.
Subscribe to Our Email Newsletter
Stay up-to-date on all the latest news from the 3D printing industry and receive information and offers from third party vendors.
You May Also Like
Profiling a Construction 3D Printing Pioneer: US Army Corps of Engineers’ Megan Kreiger
The world of construction 3D printing is still so new that the true experts can probably be counted on two hands. Among them is Megan Kreiger, Portfolio Manager of Additive...
US Army Corps of Engineers Taps Lincoln Electric & Eaton for Largest 3D Printed US Civil Works Part
The Soo Locks sit on the US-Canadian border, enabling maritime travel between Lake Superior and Lake Huron, from which ships can reach the rest of the Great Lakes. Crafts carrying...
Construction 3D Printing CEO Reflects on Being Female in Construction
Natalie Wadley, CEO of ChangeMaker3D, could hear the words of her daughter sitting next to her resounding in her head. “Mum, MUM, you’ve won!” Wadley had just won the prestigious...
1Print to Commercialize 3D Printed Coastal Resilience Solutions
1Print, a company that specializes in deploying additive construction (AC) for infrastructure projects, has entered an agreement with the University of Miami (UM) to accelerate commercialization of the SEAHIVE shoreline...