The latest in a string of successful 3D printed engine part tests was just recently completed by NASA, adding more proof that metal 3D printing is becoming a viable and revolutionary manufacturing process. While the automotive industry has been using 3D printed parts for years, the aerospace industry has been taking great care in experimenting and testing to ensure that any 3D printed parts will be just as strong and dependable as traditionally manufactured parts. Perfecting metal 3D printing is a necessity for advancing rocket engine development, as many of the next-generation designs include components with geometries far too complex to be made traditionally.
The latest test was of a 3D printed gas generator component designed for a modern update of the classic F-1 rocket engine. The generator is responsible for supplying power to a pump that will deliver enough propellant into the engine to allow the rocket to break Earth’s gravitational pull. The data being accumulated from testing the 3D printed F-1 gas generator will hopefully help NASA and the aerospace industry produce complex and advanced engine parts for their new Space Launch System. The SLS is the successor to the recently cancelled Space Shuttle program and hopefully the next phase in the United States’ manned space flight programs.
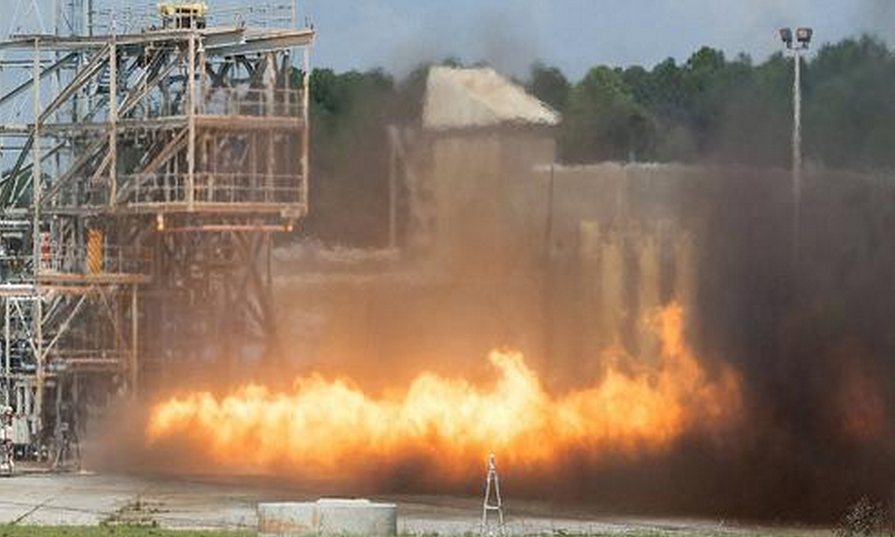
The successful test conducted at NASA’s Marshall Space Flight Center in Huntsville, Alabama [Photo: NASA]
“This test gave NASA the rare opportunity to test a 3D-printed rocket engine part, an engine part for which we have lots of data, including a test done three years ago with modern instrumentation. This adds to the database we are creating by testing injectors, turbo pumps and other 3D-printed rocket engine parts of interest to both Nasa and industry,” said NASA Marshall Space Flight Center test requestor Chris Protz.
The test series was conducted by NASA at the request of Dynetics and Aerojet Rocketdyne, which designed and manufactured the 3D printed gas generator. NASA often works closely with members of the aerospace industry on rocket development and has a vested interest in working to identify, test and ultimately develop new technologies that could enhance their own future propulsion system designs and applications.
“NASA is exploring many technologies to enhance the Space Launch System as it evolves for use in a variety of missions. If it proves to be a viable option, additive manufacturing may help us build future propulsion systems,” explained NASA’s SLS advanced development task lead Sam Stephens.
The first advanced engine being developed for the SLS project will be the Block 1 rocket and it is being designed to enable NASA to launch up to 70 metric tons into low-Earth orbit. Once successful NASA intends to move on to the second iteration called the Block 1B and is expected be capable of lifting more than 105mt into orbit. You can find out more about the new Space Launch System program over on the NASA website.
Let’s hear your thoughts on NASA’s recent tests. Discuss in the NASA 3D Printed F-1 forum thread on 3DPB.com.
Subscribe to Our Email Newsletter
Stay up-to-date on all the latest news from the 3D printing industry and receive information and offers from third party vendors.
Print Services
Upload your 3D Models and get them printed quickly and efficiently.
You May Also Like
Making 3D Printing Personal: How Faraz Faruqi Is Rethinking Digital Design at MIT CSAIL
What if your 3D printer could think more like an intelligent assistant, able to reason through a design idea, ask questions, and deliver something that works exactly the way the...
Reinventing Reindustrialization: Why NAVWAR Project Manager Spencer Koroly Invented a Made-in-America 3D Printer
It has become virtually impossible to regularly follow additive manufacturing (AM) industry news and not stumble across the term “defense industrial base” (DIB), a concept encompassing all the many diverse...
Heating Up: 3D Systems’ Scott Green Discusses 3D Printing’s Potential in the Data Center Industry
The relentless rise of NVIDIA, the steadily increasing pledges of major private and public investments in national infrastructure projects around the world, and the general cultural obsession with AI have...
Formlabs Teams Up with DMG MORI in Japan
In late June, Nick Graham, Chief Revenue Officer at Formlabs, announced on LinkedIn that the company had partnered with DMG MORI, one of the world’s leading machine tool companies, to...