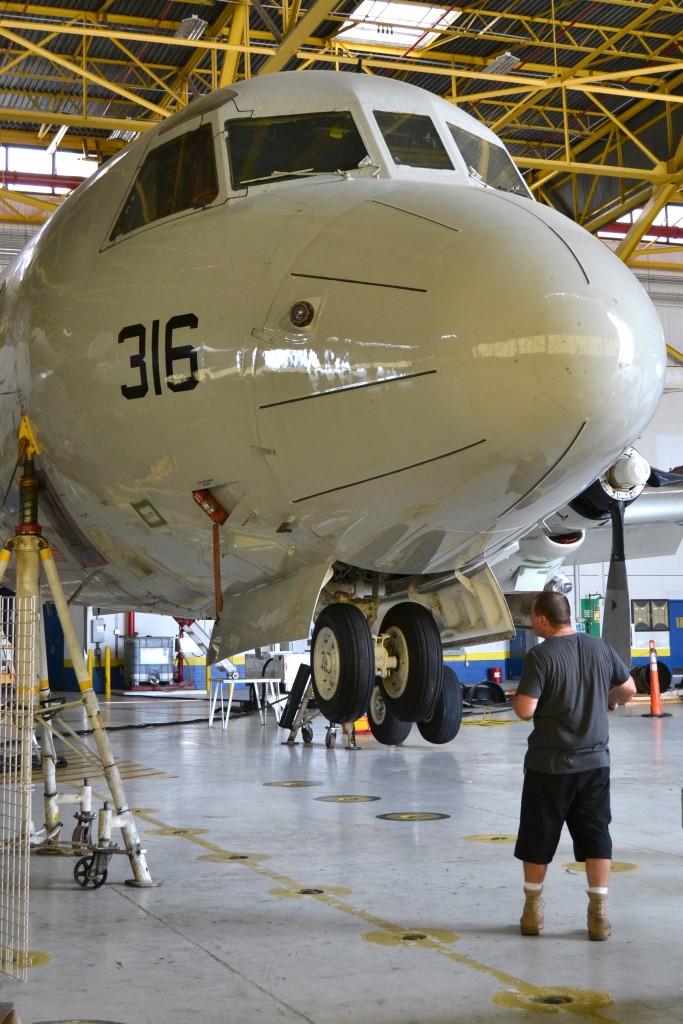
Fleet Readiness Center Southeast (FRCSE) Artisans test the functionality of a P-3 Orion’s landing gear at Hangar 1000 May 15. A team of tool designers, artisans and engineers from FRCSE used additive manufacturing to repair the Orion’s wheel-well truss. (U. S. Navy photo by Yari Miranda/Released)
When the P-3 Orion arrived in October, its wheel-well truss was in need of repair. This was no trivial project as the truss, a structural support mechanism, was for the nose landing gear of the 50-ton airplane. As if this weren’t a large enough undertaking already, the runway at Jacksonville was scheduled to close this summer. Mechanical engineering technician and tool designer Randall Meeker described the pressures:
“Not only was this a unique and complex repair, we were under a time constraint with the runway scheduled to close this summer. If that bird didn’t leave the air station before June, it would be stuck here for a long time.”
In collaboration with a team from Lockheed Martin, an initial approach to the repair was developed. After several months, a repair fitting was designed to fix the issue. However, the real hero in this story is the 3D printed prototype that allowed the team to troubleshoot quickly and effectively. A colleague of Meeker’s, mechanical engineering technician and tool designer Santiago Alvarez, described what happened:
“They sent us the design of the repair fitting so we could develop tooling to install it. We used additive manufacturing capabilities to print a 3D prototype of the fitting. When we tested it, we noticed some flaws in the design.”
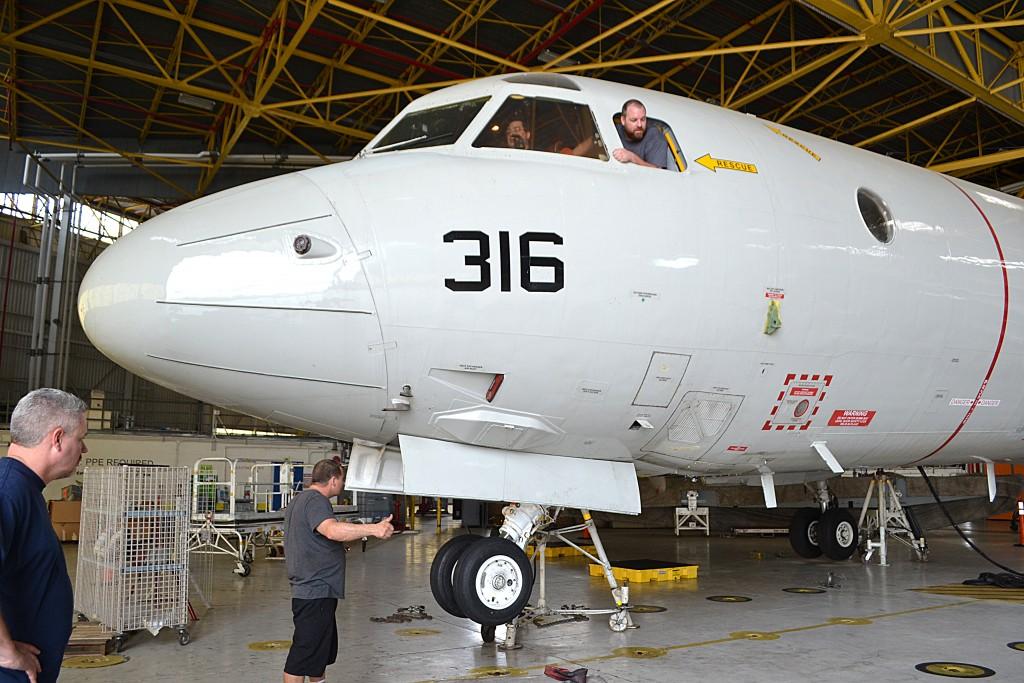
FRCSE Artisans test the functionality of a P-3 Orion’s landing gear at Hangar 1000 May 15. (U. S. Navy photo by J. L. Wright Jr./Released)
Had the prototype been made using traditional manufacturing technologies, there is no possibility that the flaws could have been detected so quickly and the Orion would have gone from a project to an emergency.
“It would have taken at least a month-and-a-half for Lockheed Martin to manufacture that fitting before they could ship it to us,” Meeker said, describing the value of the 3D printing prototyping process. “If we had received the part as originally designed, we would’ve missed our deadline.”
All this was avoided by using 3D print technology and about $300 worth of what is known as LEGO plastic, more technically called acrylonitrile butadiene styrene (ABS). As a result of the rapid feedback, Lockheed Martin was able to correct the design at the same time that the tooling was being created by military depot personnel. Rosa Cafasso, FRCSE Aerospace Engineer, said this unique situation was resolved satisfactorily thanks to 3D printing.
“This is the first time in history we have had to make this repair on a P3,” noted Cafasso. “We worked on this project for months and it was very tedious. Thanks to everyone’s effort and our 3D printing capability, we were able to come up with the proper fitting to repair it.”
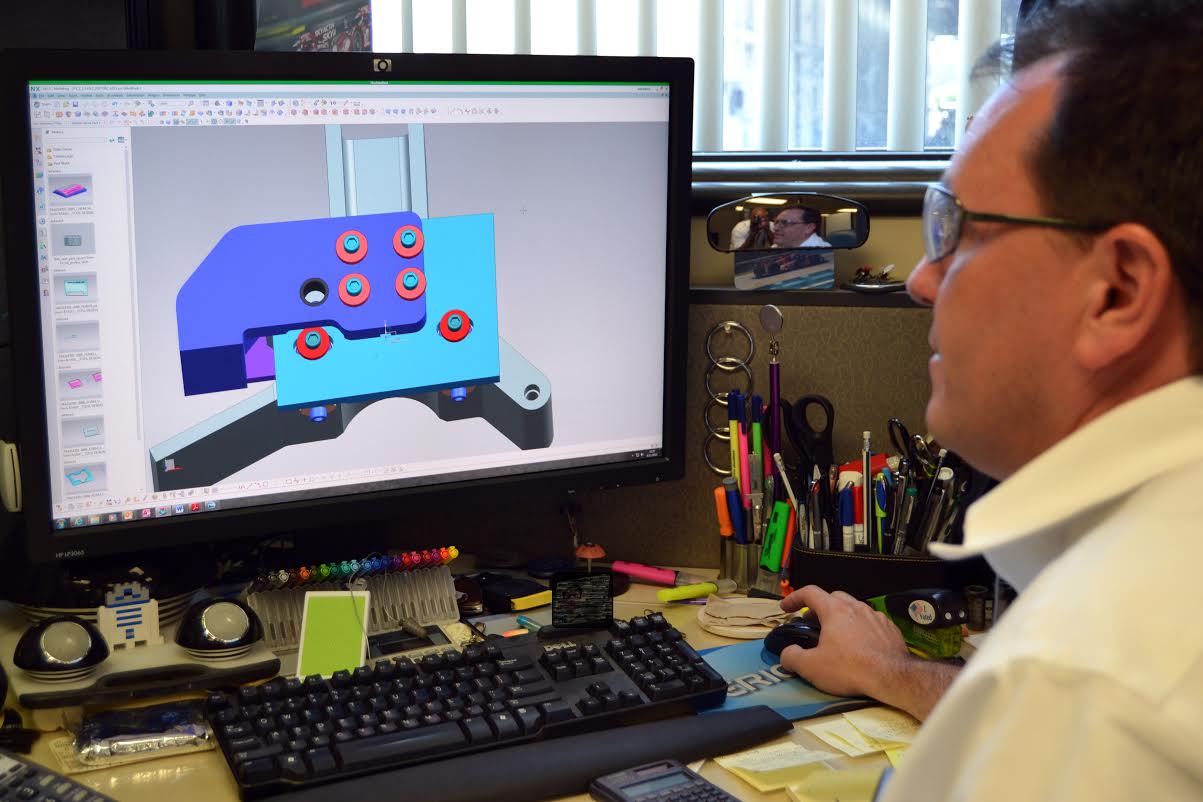
JACKSONVILLE, Fla. – Randall Meeker uses a 3-D computer software program to analyze a tooling design at Fleet Readiness Center Southeast (FRCSE) May 12. Meeker and his colleagues used additive manufacturing to print a 3-D prototype of a repair fitting to fix a P-3 Orion. By printing the prototype, FRCSE personnel identified a design flaw and prevented the fitting from being manufactured incorrectly. Meeker is a mechanical engineering technician and tool designer. (U. S. Navy photo by J. L. Wright Jr./Released)
What do you think about the use of ABS on getting this airplane back into the sky? Discuss in the P-3 Orion forum thread on 3DPB.com.
Subscribe to Our Email Newsletter
Stay up-to-date on all the latest news from the 3D printing industry and receive information and offers from third party vendors.
Print Services
Upload your 3D Models and get them printed quickly and efficiently.
You May Also Like
The Dental Additive Manufacturing Market Could Nearly Double by 2033, According to AM Research
According to an AM Research report from 2024, the medical device industry, specifically in dentistry, prosthetics, and audiology, is expected to see significant growth as these segments continue to benefit from...
Heating Up: 3D Systems’ Scott Green Discusses 3D Printing’s Potential in the Data Center Industry
The relentless rise of NVIDIA, the steadily increasing pledges of major private and public investments in national infrastructure projects around the world, and the general cultural obsession with AI have...
AM Research Webinar Explores Continuum’s Sustainable Metal Additive Manufacturing Powders
Metal additive manufacturing (AM) powder supplier Continuum Powders is working to develop solutions that empower industries to reduce waste and optimize their resources. An independent life cycle assessment (LCA) of...
3D Printed Footwear Startup Koobz Lands $7.2M in Seed Round
California-based Koobz is focused on reshoring the U.S. footwear supply chain with advanced manufacturing processes, including 3D printing. The startup just announced that it has added $6 million to its...