As a kid, I loved going to the Disney Store at the local mall, usually with my grandma. At the back of those iconic stores was a bin of stuffed toys of beloved characters, and I wanted to hug all of them. Eeyore and Sorcerer Mickey were my particular favorites, and eventually the happy days came when I was able to take each of them home. It probably would have blown my young mind if anyone had even suggested that thanks to Disney research, the day might come when I would be able to 3D print my own soft toys and other soft items.
A new paper from Disney Research, “A Layered Fabric 3D Printer for Soft Interactive Objects-Paper,” penned by Huaishu Peng (of Disney Research Pittsburgh and Cornell University), Jen Mankoff (of Carnegie Mellon University), Scott E. Hudson (of Disney Research Pittsburgh and Carnegie Mellon University), and James McCann (of Disney Research Pittsburgh), details a whole new kind of 3D printer.
Unlike the FFF, FDM, SLS, and SLA 3D printers we’ve already become used to seeing, the new machine out of this lab prints with an all new technique. The trick of it lies in the material; rather than using plastic, metal, or even paper or food, this 3D printer uses fabric.
Picture a desktop 3D printer, and the filament spool is probably a prominent feature in this image. Now, replace that image of the filament spool with a roll of fabric. That’s the best way to imagine this new machine. And coming from Disney Research, this seems almost as magical as Cinderella’s birds and mice coming by to help her with her fabric needs.
The Disney Research 3D printer works in a layer-by-layer fashion, laying down thin fabric one piece at a time. Each layer of fabric is trimmed by a laser cutter, bound by a pressure sensitive adhesive to the previous layer, and heated to activate the adhesive. Once the process is completed, the finished product is a not-immediately-impressive fabric cube. Just like many other 3D printed objects, though, the supports have to be removed–in this case, that’s the spare fabric that fills out the cube. With this extra fabric peeled away (the bright side of fabric as the print material: no tools required!), the inner object is revealed.
According to the paper, the machine operates in just a few steps:
- Turn on vacuum to hold fabric to cutting table
- Cut 2D layer shape(s) and bounding box in fabric
- Raise bonding platform to touch cut fabric
- Release cut fabric by turning vacuum off
- Lower bonding platform and advance fabric
- Heat bond new layer to print
While initially, this machine might seem as though it has little practical application outside of making lovable squishy friends for kids, the team at Disney Research noted that these models can be enhanced through the addition of conductive fabrics, electronics, even a wireless near-field communication (NFC) device that can light an LED on a smartphone case. The 3D printer is able to use two fabrics in one print job, allowing for the integration of such conductive materials, such as wiring, into one of the fabric sheets.
A full list of specs is not yet available (nor is any information about potentially bringing this prototype printer to market), but the paper’s authors worked on a 10″ x 10″ x 10″ build volume, noting that “printers of larger sizes could be easily constructed using this same design.”
“The primary physical structure of the printer is constructed with off-the-shelf aluminum extrusion,” they write. “Following the design of a number of current consumer 3D printers, motion is actuated with stepper motors and timing belts for the X and Y axes, and with a paired set of stepper motors and lead screws for the Z axis.”
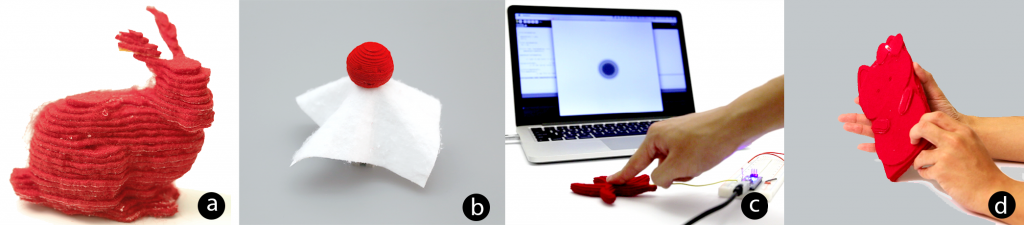
3D printed objects from Disney Research’s layered fabric 3D printer: (a) printed fabric Stanford bunny, (b) printed Japanese sunny doll with two materials, (c) printed touch sensor, (d) printed cellphone case with an embedded conductive fabric coil for wireless power reception.
With Disney stepping into the arena, another major global company is dipping its toes into the 3D printing industry–which could have a major impact. Disney’s researchers and famous teams of imagineers are well-known for bringing innovative concepts into reality, and their creativity could go a long way in the field of 3D printing.
Let us know what you think about this fabric 3D printer–does an idea like this have the potential to bring something new to market? Is this an idea you hope to see further developed? Join the discussion in the Disney Researchers Develop Fabric 3D Printer forum thread over at 3DPB.com. Check out the video below from Disney Research demonstrating the printer in action–and the full paper from Disney Research for full details.
Subscribe to Our Email Newsletter
Stay up-to-date on all the latest news from the 3D printing industry and receive information and offers from third party vendors.
Print Services
Upload your 3D Models and get them printed quickly and efficiently.
You May Also Like
Reinventing Reindustrialization: Why NAVWAR Project Manager Spencer Koroly Invented a Made-in-America 3D Printer
It has become virtually impossible to regularly follow additive manufacturing (AM) industry news and not stumble across the term “defense industrial base” (DIB), a concept encompassing all the many diverse...
Inside The Barnes Global Advisors’ Vision for a Stronger AM Ecosystem
As additive manufacturing (AM) continues to revolutionize the industrial landscape, Pittsburgh-based consultancy The Barnes Global Advisors (TBGA) is helping shape what that future looks like. As the largest independent AM...
Ruggedized: How USMC Innovation Officer Matt Pine Navigates 3D Printing in the Military
Disclaimer: Matt Pine’s views are not the views of the Department of Defense nor the U.S. Marine Corps Throughout this decade thus far, the military’s adoption of additive manufacturing (AM)...
U.S. Congress Calls Out 3D Printing in Proposal for Commercial Reserve Manufacturing Network
Last week, the U.S. House of Representatives’ Appropriations Committee moved the FY 2026 defense bill forward to the House floor. Included in the legislation is a $131 million proposal for...