The process of developing new technological solutions is fraught with many perils and, aside from the hurdles to overcome on the way to a better tomorrow, the day comes when the developers must demonstrate the New Way Forward for the assembled members of the press.
Those demonstrations and press conferences don’t always go as planned.
The latest victims of the Press Conference Finagle’s Corollary to Murphy’s Law moment are a group of second-year engineering students at Carleton University who called a presser to demonstrate the awesome that was their 3D printed bicycle.
So it was that, at the appointed hour, James Nugent, Michael Mackay-MacLaren, and Gabriel Wong stood before the local press to show off their high-tech bicycle constructed of parts built on a 3D printer.
If you’re unfamiliar with Finagle’s Corollary, it’s essentially “Anything that can go wrong, will – at the worst possible moment,” and the Carlton students discovered that to their horror and the mirth of the Fourth Estate.
The plan involved having Wong mount the cutting edge bike and give it a bit of a spin around the room. He would then accept the kudos due to him and his team once the ride had sufficiently stunned the press on hand. But it seems one element of the product development process for the bike had been overlooked; a test ride, and that led to what can only be called an “awkward moment” for the trio — and disaster for their bicycle.
As Wong strapped on a helmet and took the saddle in preparation for his historic and locomotive victory lap, the bike snapped at the head tube. And a bicycle needs a head tube. It needs one very much.
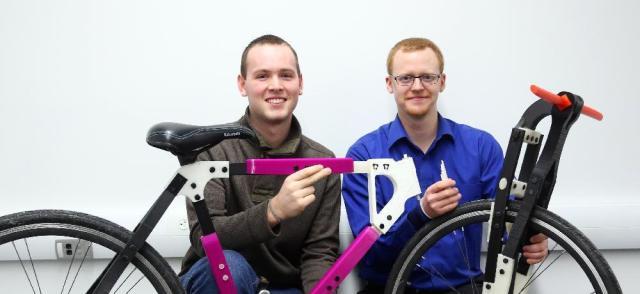
Photo courtesy The Ottawa Citizen
Nugent and Mackay-MacLaren were, for the most part, undeterred by the event and went on to tell the press that a relatively critical part had been printed hollow and not solid as planned, and that proved unfortunate.
“We performed a weight test in which subjected the frame to a large deformation. Nonetheless, the bike was able to withstand 120 lbs of force. The front wheel was the main cause of the frame deformation as it moved forward a few inches during the weight test,” Nugent and Mackay-MacLaren now say of their moment under the lights. “With the frame being tested we now had to examine the wreckage to identify the failure methods. As engineers we take failure as the optimal change to refine and redesign any flaws we find in our original design. In the near future we will be testing again with the hope of finishing before the looping makes us too dizzy to think.”
Now that the Carleton team has returned to the drawing board, which will presumably include a tick box clearly marked “Test Ride Bicycle” this time around, all will turn out well in the end.
“Once we had attached wheels and a seat, we were ready to sit on the final product to see if it could withstand the weight of a person,” they say. “Ignoring the known weaknesses, like the part where the printer had run out of plastic and not finished the print or the one with a small crack, we decided to go for it.”
Have you ever experienced a moment like this in your time as a product designer or student? Let us know in the 3D Printed Bike forum thread on 3DPB.com. Check out the video below from the press event and watch the 3D printed bike snap with your own eyes..
[Source: Ottawa Citizen]Subscribe to Our Email Newsletter
Stay up-to-date on all the latest news from the 3D printing industry and receive information and offers from third party vendors.
Print Services
Upload your 3D Models and get them printed quickly and efficiently.
You May Also Like
The Dental Additive Manufacturing Market Could Nearly Double by 2033, According to AM Research
According to an AM Research report from 2024, the medical device industry, specifically in dentistry, prosthetics, and audiology, is expected to see significant growth as these segments continue to benefit from...
Heating Up: 3D Systems’ Scott Green Discusses 3D Printing’s Potential in the Data Center Industry
The relentless rise of NVIDIA, the steadily increasing pledges of major private and public investments in national infrastructure projects around the world, and the general cultural obsession with AI have...
AM Research Webinar Explores Continuum’s Sustainable Metal Additive Manufacturing Powders
Metal additive manufacturing (AM) powder supplier Continuum Powders is working to develop solutions that empower industries to reduce waste and optimize their resources. An independent life cycle assessment (LCA) of...
3D Printed Footwear Startup Koobz Lands $7.2M in Seed Round
California-based Koobz is focused on reshoring the U.S. footwear supply chain with advanced manufacturing processes, including 3D printing. The startup just announced that it has added $6 million to its...