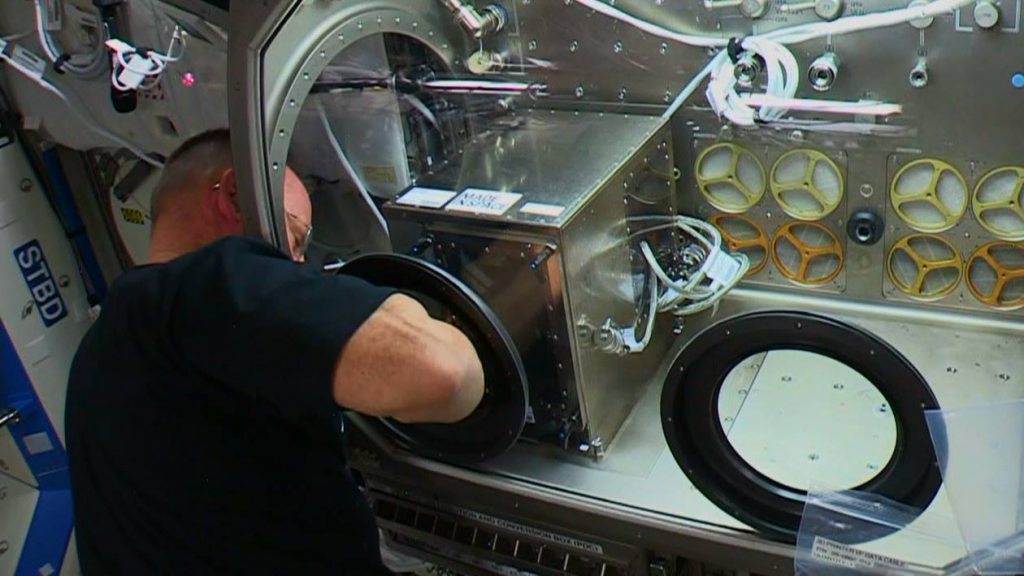
Butch operating 3D printer on ISS (photo credit: NASA)
Butch needed a wrench.
Usually this isn’t a big deal, but Butch couldn’t just drive over to Home Depot and grab a new one. “Butch” is ISS Commander Barry Wilmore, and he is currently orbiting the Earth.
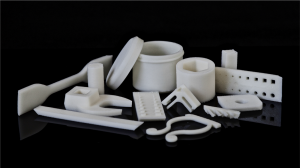
3D printed objects printed both on the Earth and on the ISS
Fortunately for Butch and the team aboard the International Space Station (ISS), they have a 3D printer at their disposal. With the impressive help of Made In Space, astronauts have been 3D printing objects they’ve needed (as well as a few to test the technology) since November. So far, 21 objects have been created via the ISS’ 3D printer. The same objects have also been 3D printed on terra firma, and will be compared to those printed in low-Earth orbit to see the effects, if any, of microgravity on the 3D printing process and pieces.
The first 20 objects were made using design files produced prior to the printer’s launch into orbit; the most recent, though, was made-to-order and was pretty much hardware “emailed” to space.
The team at Made In Space happened to overhear Butch talking about the need for a socket wrench, so they set about designing one in CAD to send up. They started out using Autodesk Inventor, and converted the file into G-code at the Made In Space office in Moffett Field, California, and then sent those files over to NASA, which, in turn, sent the files — via the Huntsville Operations Support Center — to the ISS.
Because files can be sent at the speed of light, the ISS team received the wrench significantly faster than they would have in years past, when they would have needed to wait for the next supply rocket launch. That’s a lot to go through just to get a small hand tool — and that’s a huge part of the entire Made In Space initiative.
Once the CAD files were received on the ISS, they were sent to the 3D printer. The printer, in the Columbus laboratory module’s Microgravity Science Glovebox, then created the ratcheting socket wrench, which Butch pulled out as a ready-to-use tool. Effectively, Made In Space just “emailed” the ISS team the hardware they needed to get the job done, through sending the files that could be turned into a tangible tool.
It looks like the first file made on Earth and sent to space was a resounding success! This opens the door to a bright future for space travel and manned trips. If, for example, humanity does ever colonize Mars or go back to the moon, any broken or needed tools can be produced on an as-needed basis. This lessens costs and time required for resupplying crew members with valuable implements, and can enhance the process of experimentation in space.
I guess that’s official: we live in the future! Let us know your thoughts on this latest advance in the Hardware “Emailed” to ISS forum thread over at 3DPB.com.
Subscribe to Our Email Newsletter
Stay up-to-date on all the latest news from the 3D printing industry and receive information and offers from third party vendors.
Print Services
Upload your 3D Models and get them printed quickly and efficiently.
You May Also Like
U.S. Navy Lab Uses 3D Printing to Reduce Tooling Lead Time By Over 90%
The F-35 Lightning II Joint Program Office (JPO), responsible for life-cycle management of the key fifth-generation joint strike fighter (JSF) system used by the U.S., its allies, and its partners,...
Etsy Design Rule Change Reduces Selection of 3D Printed Goods
Online marketplace Etsy has implemented a rule change requiring all 3D printed goods on the site to be original designs. The update to the site’s Creativity Standards states, ¨Items produced using...
Honeywell Qualifies 6K Additive’s Nickel 718 for 3D Printed Aerospace & Defense Parts
6K Additive is renowned for manufacturing sustainable additive manufacturing (AM) powder, and offers a wide portfolio of premium metal and alloy powders that include titanium, copper, stainless steel, and nickel,...
MetalWorm Sells WAAM Systems to Research Institutes in Brazil and Malaysia
Turkish WAAM firm MetalWorm has sold a system in Malaysia and another in Brazil. This is an excellent example of a few emerging trends in additive. Firstly, WAAM was experimented...