Firestorm Labs just landed a $100 million contract with the U.S. Air Force to develop 3D printed drones. The San Diego startup, known for its modular unmanned aerial systems (UAS), will use the funding to speed up drone production and integration for military operations.
This deal is a five-year Indefinite Delivery, Indefinite Quantity (IDIQ) agreement, allowing the Air Force to place multiple orders over time and adapt to changing needs. The goal is to create modular, cost-effective drones that can be 3D printed and deployed anywhere, giving the military more flexibility in high-stakes environments.
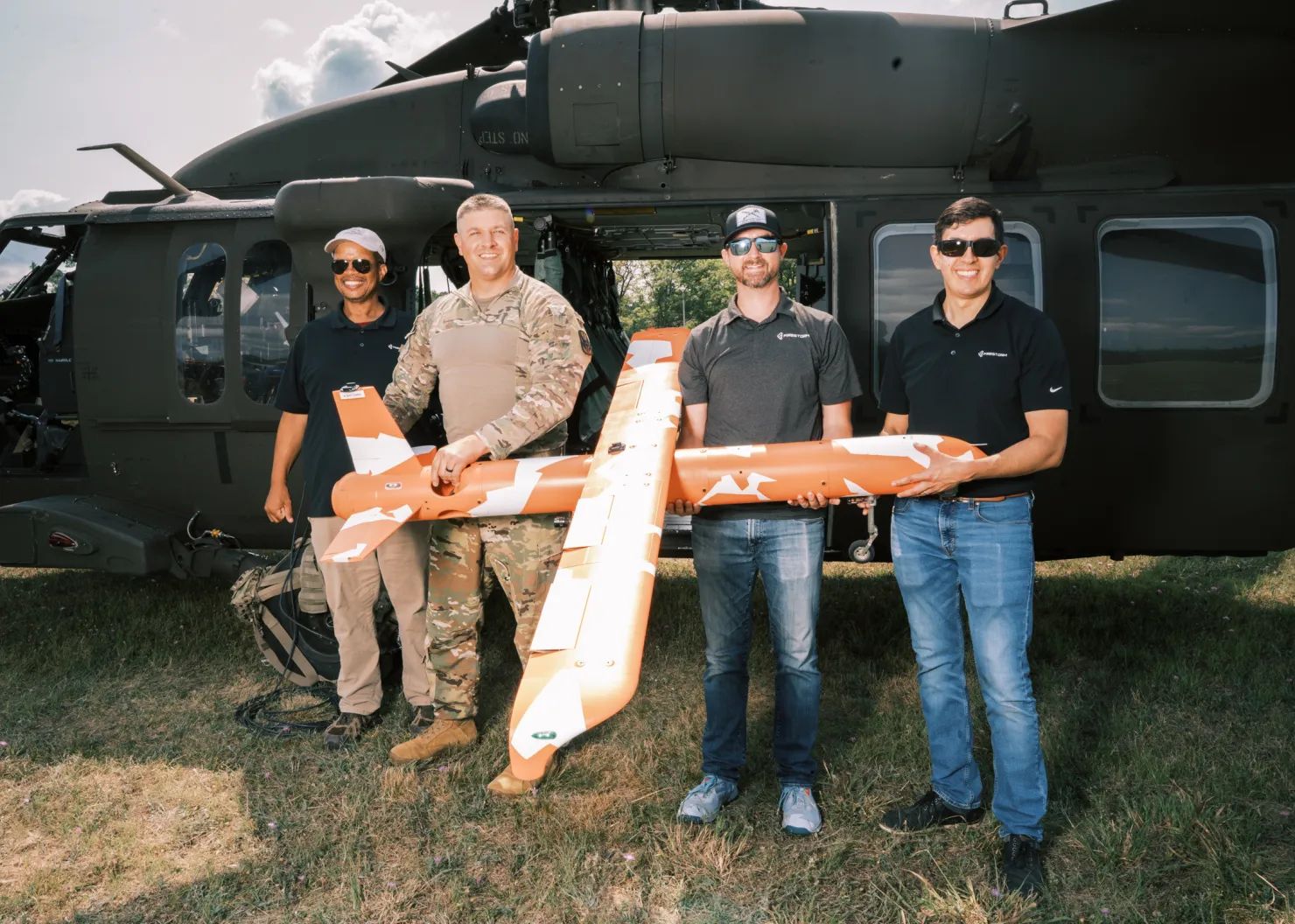
Firestorm participates in Northern Strike 24-2, one of the DoD’s largest reserve component readiness exercises. Image courtesy of Firestorm via LinkedIn.
3D Printing Meets the Battlefield
Firestorm leverages additive manufacturing (AM) to build highly customizable, rapidly deployable UAS. Instead of relying on massive factories and traditional supply chains, the startup’s approach allows drones to be printed and assembled in the field—wherever and whenever needed.
“This award reflects the Air Force’s confidence in Firestorm’s ability to deliver modular, cost-effective UAS solutions that redefine the boundaries of innovation,” said Firestorm CEO and co-founder Dan Magy. “We are excited to contribute to the modernization of warfighter capabilities, ensuring operational agility and strategic dominance in evolving combat environments.”

Firestorm’s Tempest drones participate in the T-REX 24-2 event. Image courtesy of Firestorm via LinkedIn.
With this contract, Firestorm is working closely with AFWERX—the Air Force’s innovation arm that partners with startups to fast-track new technologies—along with the Air Combat Command (ACC) and the Air Force Special Operations Command (AFSOC) to bring its vision of modular drone technology to life. Unlike conventional military drones that are pre-designed for specific missions, Firestorm’s UAS can be tailored in real time based on mission requirements.
That means Firestorm’s drones can be adapted for different missions instead of being built to a fixed design. Depending on the mission, they can be equipped with different sensors, adjusted for different levels of autonomy, or even reconfigured into entirely new models. And because they’re 3D printed, these changes can be made in days instead of the months or years traditional manufacturing requires.
“We’re not selling a single solution for a niche problem; we are over the bases of the future of warfare,” said Chad McCoy, Firestorm’s Co-founder and Chief Strategy Officer.
Breaking Free from Supply Chain Constraints
One of the biggest challenges in modern warfare is logistics. A 2017 report from the Defense Business Board, Logistics as a Competitive War Fighting Advantage, warned that maintaining supply chains and operational readiness has become increasingly complex for the Department of Defense (DoD), creating risks and opportunities on the battlefield. Getting new drones, replacement parts, or customized systems into operational zones can be a slow, expensive process, often delayed by long production cycles, supply chain bottlenecks, and reliance on overseas manufacturing. What’s more, in conflict zones, supply convoys can be attacked, making it even harder to deliver important equipment where it’s needed.
Firestorm’s answer is the xCell system, a mobile 3D printing unit housed in a shipping container designed to produce and prototype drones directly at the edge of the battlefield. xCell is a semi-automated, expeditionary manufacturing cell that can be operated with limited human-in-the-loop engagement and powered by generators off-the-grid.
“Production for group 1-3 drones anywhere in the world is what we offer,” added McCoy. “Our vision is to enable the production of systems, parts, and prototyping at the edge, agnostic of vendor. xCell is our response to the challenges of an uncertain supply chain, isolated geography, and contested logistics that demand innovation. Working closely with the Air Force has allowed Firestorm to focus on the hardest problems and deliver impactful solutions. We’re not offering a single solution for a niche problem; we are laying the foundation for the future of warfare.”
This means that instead of waiting on shipments from traditional defense contractors, the military could potentially print drones and components on-site, reducing downtime and increasing adaptability in high-stakes situations.
The IDIQ contract will enable Firestorm to test and develop its drone technology in partnership with the Air Force over the next five years. Each order placed under the contract can remain active for up to two years, giving Firestorm time to develop, test, and integrate its drones into Air Force operations.
With $100 million in funding and a direct line to the Air Force, Firestorm has a huge opportunity to shape the future of drone warfare. The next steps will likely include expanding the capabilities of its 3D printed drone systems, conducting real-world tests with Air Force units, integrating advanced AI and sensor technologies into its UAS platforms, and scaling up xCell production for greater deployment flexibility.
If Firestorm delivers on its vision, we could be looking at a new era of warfare where drones are no longer built in far-off factories but printed and assembled right where they’re needed. This contract is also a sign that the U.S. military is embracing the speed and flexibility that startups can offer over traditional defense contractors. With AFWERX’s mission of fast-tracking innovative technology, we could see more agile companies like Firestorm taking center stage in military procurement.
Subscribe to Our Email Newsletter
Stay up-to-date on all the latest news from the 3D printing industry and receive information and offers from third party vendors.
Print Services
Upload your 3D Models and get them printed quickly and efficiently.
You May Also Like
Consolidation in AM: How 2025 Is Shaping the Industry’s New Normal
The first half of 2025 has been marked by a clear shift in the additive manufacturing (AM) industry. Companies are no longer just focused on developing new tech by themselves....
Etsy Design Rule Change Reduces Selection of 3D Printed Goods
Online marketplace Etsy has implemented a rule change requiring all 3D printed goods on the site to be original designs. The update to the site’s Creativity Standards states, ¨Items produced using...
U.S. Congress Calls Out 3D Printing in Proposal for Commercial Reserve Manufacturing Network
Last week, the U.S. House of Representatives’ Appropriations Committee moved the FY 2026 defense bill forward to the House floor. Included in the legislation is a $131 million proposal for...
Transforming From Tourist to Native: Duro CEO Michael Corr Explains Why the Company Rebuilt its PLM Software on AI
In these early innings of the AI boom, many market analysts have expressed concern that AI spend has gotten too far ahead of the technology’s proven ability to deliver significant...