In 3D Printing News Briefs today, Formlabs’ Chief Product Officer addresses the safety concerns of low-cost 3D printing resins. UltiMaker achieved two important ISO certifications, and ABB Robotics has launched an Energy Efficiency Service. Finally, could 3D printed bricks made out of recycled glass be the next big innovation in additive construction?
Formlabs Discusses Safety Concerns with ACMO in Low-Cost Resins
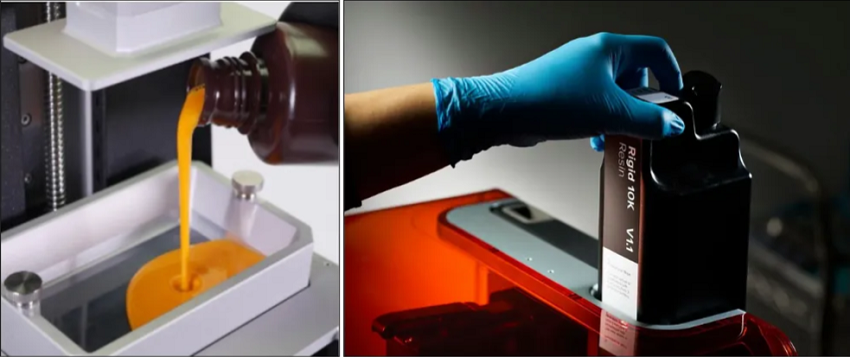
Left: Low cost printers require users to manually pour resin. Right: The Formlabs ecosystem utilizes auto-dispensing resin cartridges, minimizing potential resin exposure.
Thanks to lower-cost resin 3D printers, the technology is more accessible than ever. But cheap, highly reactive chemicals are often used in resin-making to increase print speed and cut costs, and a lack of safety information from some resin manufacturers has resulted in injuries, misinformation, and uncertainty. The EPA recently issued a Significant New Use Regulation (SNUR) for 4-Acryloylmorpholine (ACMO)—one of the most common chemicals in cheaper resins—because of the dangerous effects of skin contact and breathing in its vapors. Plus, many resins containing ACMO are advertised as being washable in water, and misleading marketing has shown 3D printed parts being washed in regular household sinks, which can contaminate water supplies. Manufacturers are now required to report the contents of ACMO on their Safety Data Sheets (SDS), and list several warnings, such as “may cause an allergic skin reaction” and “may cause reproductive effects.” You can find a list of resins that contain this chemical here; its CAS Registry Number is 5117-12-4. If you must print with ACMO-containing resins, you should use a respirator and ventilation.
David Lakatos, Chief Product Officer at Formlabs, says the company is “deeply committed” to making resin 3D printing safe and accessible, and as such does not use ACMO in its resins. But, as he explained in an article for Medium, accessibility is “also about intentionally creating an ecosystem that enables safe operation in a variety of environments with a large range of users.” In order to ensure a safe, well-documented resin printing ecosystem, Formlabs has made many specific design decisions over the years, such as owning and operating its own U.S. resin production facility, engineering resins that don’t require fume hoods or respirators, and publishing every SDS and Technical Data Sheet (TDS) in an easy-to-find location. The company also designed its 3D printer ecosystem to minimize user contact with IPA and resin, with solutions like auto-dispensing resin cartridges, and released the print settings for its General Purpose V5 and Tough 2000 V1.1 resins.
UltiMaker Achieves Recertification for ISO 9001 & ISO 14001
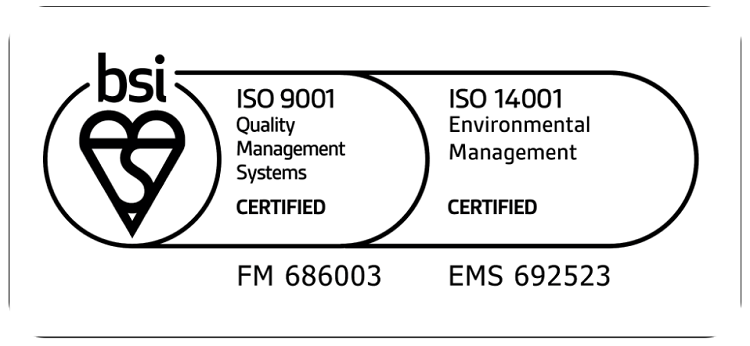
Certifications highlight the company’s adherence to global quality and environmental management standards.
UltiMaker announced that it has successfully been recertified for ISO 9001 Quality Management Systems and ISO 14001 Environmental Management Systems, which highlights the company’s commitment to manufacturing excellence and high standards in quality and sustainability practices. Global standards organization BSI (British Standards Institution) Group, a founding member of the ISO (International Organization for Standardization), completed a thorough audit of UltiMaker’s operations and 3D printing solutions production at its Dutch research and manufacturing facilities. ISO 9001:2015 certification means that the company is committed to maintaining high quality management standards, while ISO 14001:2015 affirms that it follows internationally recognized standards to minimize its environmental impact. The independent audit found that UltiMaker’s management systems meet the standard requirements for quality assurance and environmental measures.
“This achievement highlights our commitment to meeting and even exceeding industry compliance standards. We will continue to ensure that these principles guide our operations and enhance the value we deliver to our customers,” said Roy Janssen, Senior Product Safety, Environment & Compliance Specialist, UltiMaker.
ABB Robotics Introduces New Energy Efficiency Service
To help customers improve sustainability and save on costs, ABB Robotics launched an Energy Efficiency Service, which includes a package of analysis, consultation, and tools to measure and improve the energy efficiency of their robots. According to a Global Energy Efficiency Movement survey, industrial companies count enhanced sustainability and reduced energy costs as key to competitiveness, and ABB pilot studies have found that this new service offers up to 30% energy savings. The suite offers three main energy measurement tools, so users can easily assess and optimize the energy efficiency of their robots. The first is the external measurement tool Standby Energy Optimization: data gathered by this tool is used to generate a report with advice on how to save energy and further fine-tune robot performance. The Program Optimization tool analyzes a robot’s operating program to find areas where energy-saving improvements can be made. Finally, the Energy Monitoring and Benchmarking tool allows users to continuously monitor robot energy consumption and comparison.
“Reducing energy consumption is a priority for manufacturers, with over 93 percent surveyed stating they will invest in energy efficiency improvements in the next three years to reduce costs and demonstrate progress towards more sustainable operations. Our new service will identify ways to achieve these objectives by optimizing robot energy efficiency, including fine-tuning performance and using the latest robot technologies,” said Michael Hose, Managing Director ABB Robotics Customer Service Business Line.
Building Homes with 3D Printed Recycled Glass Bricks
The 3D printed housing market may still be young, but it’s expected to grow rapidly over the next few years, going from $36.8 million in 2022 to over $1 billion by 2030. Most 3D printed homes are made out of concrete, but engineers at the Massachusetts Institute of Technology (MIT) have come up with a way to 3D print construction bricks out of recycled glass. This could help overcome environmental challenges in home design, as manufacturing construction materials make up about 15% of global greenhouse gas emissions; plus, the demolition and construction industry sends over 145 million tons of waste annually to landfills. So Kaitlyn Becker, assistant professor of mechanical engineering at MIT, and former MIT graduate student and researcher Michael Stern, the founder and director of 3D printed glass manufacturer Evenline, turned to circular construction: by making their blocks out of recycled glass, they can help reduce the construction industry’s embodied carbon. Plus, as long as the glass isn’t contaminated, it can be recycled endlessly.
As the team explained in their study, the multilayered glass bricks are interlocking. Using two round pegs, the bricks, which were designed in a figure-8 shape, can be linked together and stacked up to build curved walls. Evenline’s custom glass 3D printing system connects with a furnace, which melts crushed glass bottles into a printable material. To prevent cracks and scratches, an additional material is placed between the bricks. Concrete is the most common additive construction material due to its availability and affordability, and can be formed into complex structures and shapes. So the researchers used an industrial hydraulic press to test their 3D printed glass bricks and see how they compare to concrete. The results were promising: the printed bricks made mostly from glass, with separate interlocking features on the bottom, held up to the highest amount of pressure. These layered blocks were able to hold up under pressures similar to what concrete blocks can withstand. Now, the team plans to scale up their design to build larger structures, like a pavilion, out of their glass bricks.
Subscribe to Our Email Newsletter
Stay up-to-date on all the latest news from the 3D printing industry and receive information and offers from third party vendors.
Print Services
Upload your 3D Models and get them printed quickly and efficiently.
You May Also Like
The Dental Additive Manufacturing Market Could Nearly Double by 2033, According to AM Research
According to an AM Research report from 2024, the medical device industry, specifically in dentistry, prosthetics, and audiology, is expected to see significant growth as these segments continue to benefit from...
Heating Up: 3D Systems’ Scott Green Discusses 3D Printing’s Potential in the Data Center Industry
The relentless rise of NVIDIA, the steadily increasing pledges of major private and public investments in national infrastructure projects around the world, and the general cultural obsession with AI have...
AM Research Webinar Explores Continuum’s Sustainable Metal Additive Manufacturing Powders
Metal additive manufacturing (AM) powder supplier Continuum Powders is working to develop solutions that empower industries to reduce waste and optimize their resources. An independent life cycle assessment (LCA) of...
3D Printed Footwear Startup Koobz Lands $7.2M in Seed Round
California-based Koobz is focused on reshoring the U.S. footwear supply chain with advanced manufacturing processes, including 3D printing. The startup just announced that it has added $6 million to its...