Kevin Kassekert’s appointment as CEO of VulcanForms marks a bold change for the company. A seasoned leader, Kassekert has worked in some of the most transformative industries of our time—from early work in semiconductors to scaling innovations at Tesla and Redwood Materials. His strong expertise and focus on people-first leadership are the cornerstones of his vision for VulcanForms.
In a recent interview with 3DPrint.com, Kassekert shared his plans to lead VulcanForms as he steps into his new role: “Throughout my career, I learned the value of a strong team. This is the foundation of any successful company, and this philosophy is already in motion at VulcanForms. The leadership that preceded me, Martin Feldman and John Hart, have developed a team with tremendous talent and some of the best additive manufacturing technology in the industry.”
Kassekert’s leadership style revolves around “people-centric, servant leadership,” a principle he emphasized during the interview. He views his role as supporting the team, not the other way around.
“My job as a leader is to support that team and align our vision to accelerate innovation. At Tesla and Redwood, I learned the value of being able to fail and learn from mistakes. We will foster a culture at VulcanForms where it’s okay to try, fail, and ultimately learn to push the boundaries in a meaningful way.”
Powering Up
With a background in high-tech manufacturing, Kassekert is no stranger to challenges. His time at Tesla gave him a clear understanding of how to build an innovative, efficient, and scalable operation. As VulcanForms pushes the boundaries of digital manufacturing, Kassekert sees scaling as the next critical step.
He outlined how they are working to grow: “We’re advancing a distributed digital foundry and manufacturing model, leveraging our technology and equipment to deliver great products for our customers.”
Moreover, Kassekert emphasized VulcanForms’ distributed digital foundry model, which integrates the entire manufacturing process—from sourcing materials to post-processing and finishing. Inspired by lessons from the Tesla Gigafactory, this approach focuses on localized manufacturing to reduce logistics costs and carbon emissions while improving efficiency and sustainability.
VulcanForms is tackling an impressive range of industries, from medical and aerospace to defense and consumer goods. Kassekert explained how AM opens doors to materials and designs that were previously inaccessible.
“It’s about understanding the right markets to focus on and where we can make the biggest impact. Some areas are saturated, while others—like certain materials and applications—are still untapped opportunities.”
VulcanForms is targeting key verticals where lightweight, high-strength parts are essential. Kassekert highlighted opportunities in implantables, orthopedics, and consumer products requiring high-strength alloys and lower-cost materials for demanding conditions.
In addition, the executive pointed to the company’s ability to design with sustainability and efficiency at the forefront. Kassekert’s deep concern for sustainability stems not just from his career in electric vehicles and battery manufacturing but from a personal belief.
“I’m a father, I’m a husband. I have a family for whom I want to make sure we leave a good world. I believe it’s my job to leave this world better than I found it,” he said. By placing manufacturing hubs closer to customers, VulcanForms can reduce the carbon footprint associated with global shipping and create more efficient, localized production.
Shifting Gears
Another key element of Kassekert’s plan for VulcanForms is scaling through volume. Drawing from his experience at Tesla, he described how the cost of car batteries was driven down through sheer scale, a principle he believes will apply to VulcanForms as they grow.
“One of the main ways to drive cost down is through volume, and that’s where we’re focused—driving the world’s most competitive cost through scale and volume,” says the CEO.
This focus on scaling is crucial as VulcanForms navigates the challenges of competing in an industry where many 3D printing companies are struggling financially, being acquired, or even going bankrupt. In a time when several competitors are getting delisted or merging to survive, VulcanForms aims to stay independent, competitive, and strong.
“It’s about balancing those three things: understanding where the market is heading, continuing to invent, and driving down costs. By innovating not just in additive manufacturing but also in supply chain management and post-processing, VulcanForms is working to stay ahead of the curve.”
Kassekert says his bigger plan for VulcanForms has similarities with his time in the semiconductor industry, where he spent 13 years early in his career. In those early days, semiconductor companies were scrambling to build their own fabrication plants, or fabs, which are specialized facilities for manufacturing semiconductor devices. These fabs were incredibly expensive to build and operate, making it difficult for smaller companies to compete. The executive also explains that seeing the semiconductor industry in its earliest stages, just as it began to take off, gave him a unique perspective on how industries mature and consolidate over time.
He sees a similar path for AM: “The industry winners will be those who can produce at high volume. Our trajectory is to develop new technology that doesn’t necessarily exist today with higher laser count, higher power, faster scan times, lower production costs, and scale production to deliver specialized parts for a whole plethora of customers.”
This insight comes from his experience in semiconductors, where only the largest players with the capacity to scale production survived. In fact, Kassekert makes a direct comparison between VulcanForms and the Taiwan Semiconductor Manufacturing Company (TSMC) foundry model, one of the largest and most well-known semiconductor pure-play foundries in the world where high-volume manufacturing became the key to success.
Much like TSMC serves various customers with its massive production capabilities, Kassekert has a vision of VulcanForms becoming the manufacturing foundation for specialized parts across industries. By leveraging its unique position as both an equipment developer and a manufacturer to deliver high-quality, low-cost products at scale, VulcanForms will seek to innovate continuously, similar to TSMC’s role in the semiconductor world.
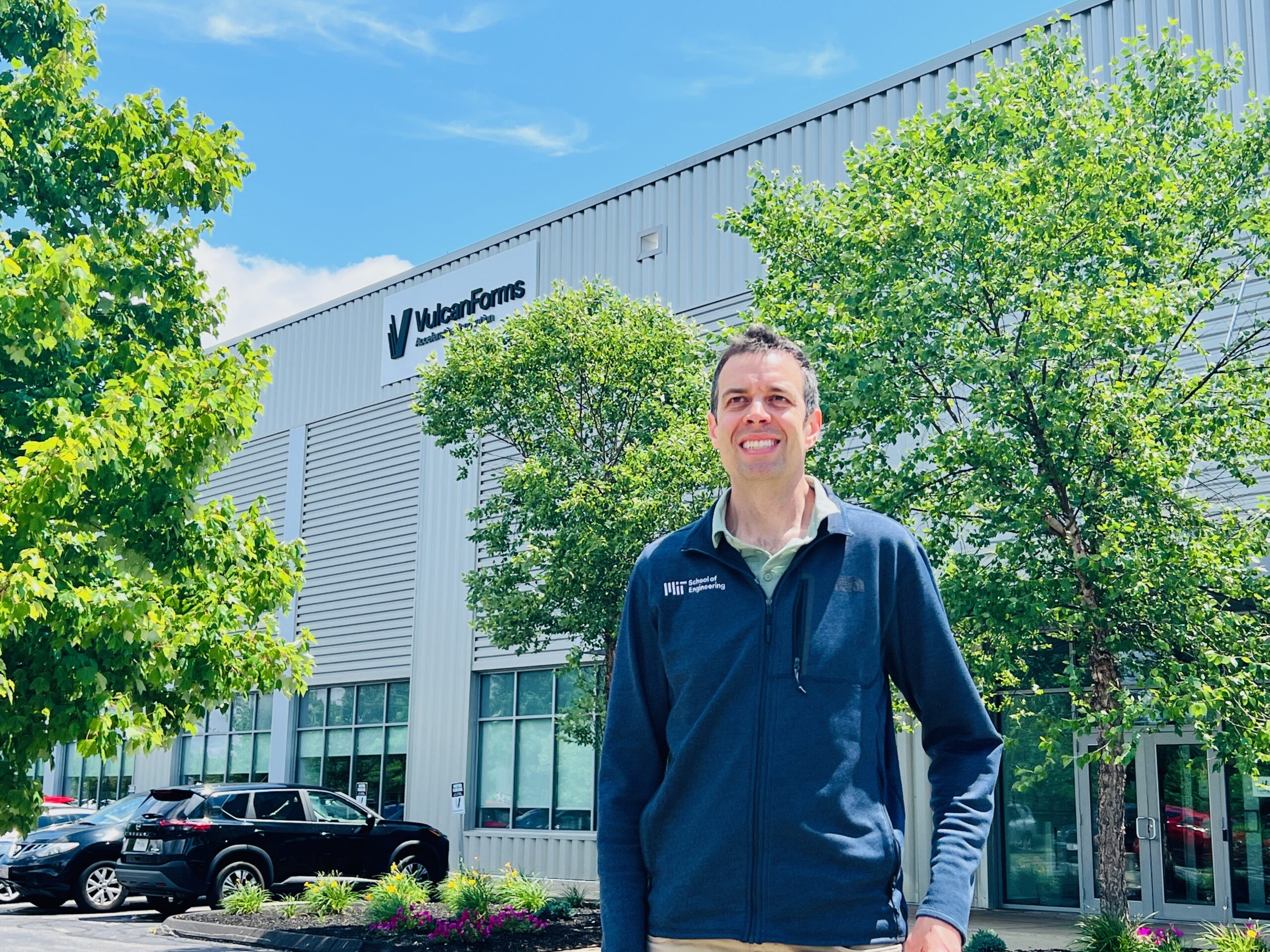
VulcanForms co-founder John Hart at the company headquarters in Massachusetts. Image courtesy of 3DPrint.com/Vanesa Listek.
Building a New Vision
At the core of all these innovations is the team, and Kassekert’s commitment to strengthening that team was clear throughout our conversation. After becoming CEO in September 2024, he spent his early days at VulcanForms, meeting with employees at every level to understand what was working and what could be improved.
During my recent visit to VulcanForms, I saw firsthand the company’s impressive operations at its Devens, Massachusetts, facility. Walking through its 160,000-square-foot headquarters, it was clear that VulcanForms is pushing the boundaries of industrial 3D printing with its advanced laser powder bed fusion (LPBF) technology and AI-driven solutions. As VulcanForms begins this new chapter under Kassekert’s leadership, the company remains focused on its foundational tech, driven to advance manufacturing techniques and production methods.”
“This is an opportunity to change the way the world manufactures parts. There are so many different ways to produce efficiently nowadays, so we plan to push the roadmap of additive manufacturing,” concluded Kassekert.
Subscribe to Our Email Newsletter
Stay up-to-date on all the latest news from the 3D printing industry and receive information and offers from third party vendors.
Print Services
Upload your 3D Models and get them printed quickly and efficiently.
You May Also Like
Consolidation in AM: How 2025 Is Shaping the Industry’s New Normal
The first half of 2025 has been marked by a clear shift in the additive manufacturing (AM) industry. Companies are no longer just focused on developing new tech by themselves....
Etsy Design Rule Change Reduces Selection of 3D Printed Goods
Online marketplace Etsy has implemented a rule change requiring all 3D printed goods on the site to be original designs. The update to the site’s Creativity Standards states, ¨Items produced using...
U.S. Congress Calls Out 3D Printing in Proposal for Commercial Reserve Manufacturing Network
Last week, the U.S. House of Representatives’ Appropriations Committee moved the FY 2026 defense bill forward to the House floor. Included in the legislation is a $131 million proposal for...
Transforming From Tourist to Native: Duro CEO Michael Corr Explains Why the Company Rebuilt its PLM Software on AI
In these early innings of the AI boom, many market analysts have expressed concern that AI spend has gotten too far ahead of the technology’s proven ability to deliver significant...