After its launch earlier this year, Auto Additive has begun shipping its 3D printed products for auto repair. Specifically, the 3D printing and engineering services company has sent the first order for weldable headlight tabs to one of its founding partners, Headlights.com, as it begins initiating its go-to-market strategy for later in the year.
The Chicago-based company has engineered these tabs in collaboration with Headlights.com, using advanced polypropylene material compatible with OEM requirements. This material meets GM’s GMW18647 worldwide standards, ensuring the tabs are not only durable but also fully compatible with existing repair techniques, offering a viable alternative to traditional methods like two-part epoxy, shaping putty, and industrial-grade welding rods.
The news is part of Auto Additive’s broader strategy to harness 3D printing for automotive repairs, a move supported by the company’s foundational role in the 3D Printing in Auto Repair Task Force. This initiative, endorsed by industry experts and corporate partnerships, including HP and Forecast 3D, aims to integrate additive manufacturing into everyday automotive repair jobs effectively. The move also highlights the practical applications of 3D printing technologies in providing innovative repair solutions, significantly impacting maintenance, repair, and overhaul (MRO) operations within the industry.
Auto Additive’s initiative is a direct response to the industry’s slow adoption of 3D printing for end part production and MRO tasks. Despite the technology’s potential, its application in auto repair has been limited. The recent introduction of these 3D printed parts is expected to change this narrative by providing more efficient, cost-effective solutions that reduce waste and enhance repair quality.
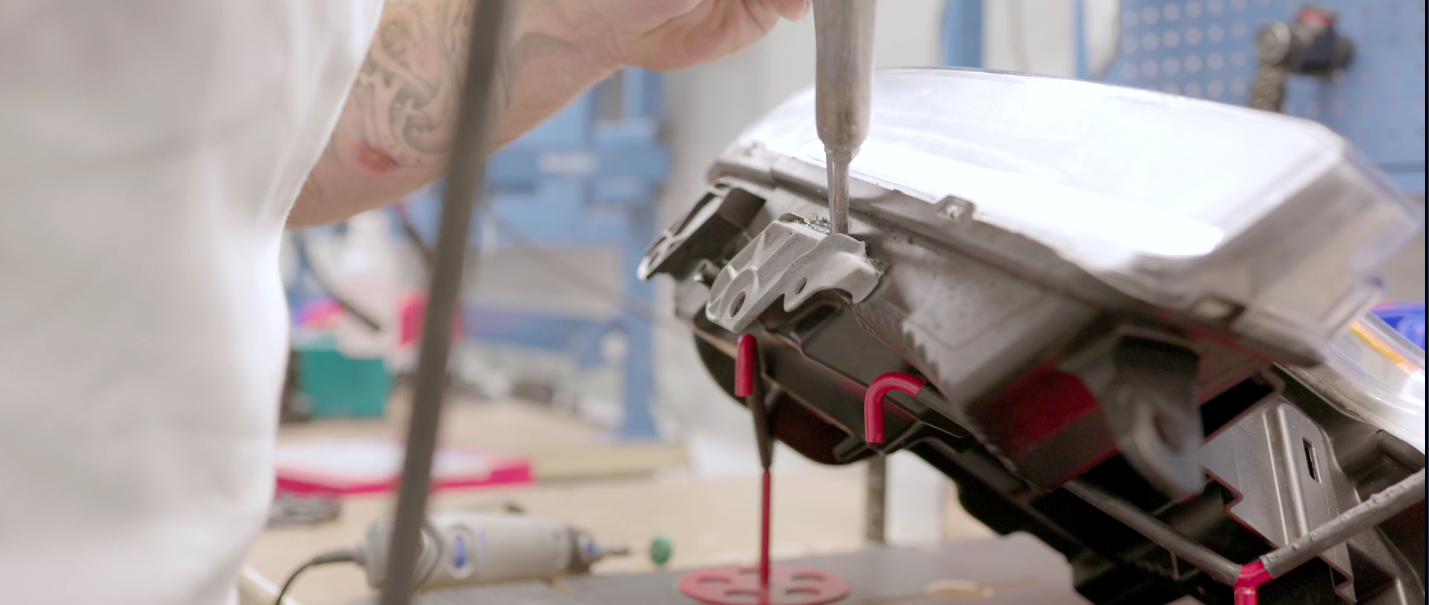
3D printed headlight tabs
The company’s efforts align with the industry’s move towards more sustainable and innovative repair methods, championed by the 3D Printing in Auto Repair Task Force’s recent findings and the strategic direction provided by industry veterans like Harold Sears. This holistic approach towards integrating 3D printing into the automotive sector is not just about innovation but also about setting new standards and practices that could eventually influence global automotive repair techniques. We’ll start to get a sense of exactly how by the end of the year, as Auto Additive is set to launch these parts to a broader market by November 2024.
Mirroring efforts by groups like Mobility | Medical goes Additive, we could ultimately see the use of 3D printing for MRO in automotive complement adoption across just about every vertical. 3D printing’s strength in producing individual parts on demand could parallel the Right to Repair movement at a time when reusing resources overtakes virgin material manufacturing, thus leading to a more circular and sustainable production paradigm.
Subscribe to Our Email Newsletter
Stay up-to-date on all the latest news from the 3D printing industry and receive information and offers from third party vendors.
Print Services
Upload your 3D Models and get them printed quickly and efficiently.
You May Also Like
Reinventing Reindustrialization: Why NAVWAR Project Manager Spencer Koroly Invented a Made-in-America 3D Printer
It has become virtually impossible to regularly follow additive manufacturing (AM) industry news and not stumble across the term “defense industrial base” (DIB), a concept encompassing all the many diverse...
Inside The Barnes Global Advisors’ Vision for a Stronger AM Ecosystem
As additive manufacturing (AM) continues to revolutionize the industrial landscape, Pittsburgh-based consultancy The Barnes Global Advisors (TBGA) is helping shape what that future looks like. As the largest independent AM...
Ruggedized: How USMC Innovation Officer Matt Pine Navigates 3D Printing in the Military
Disclaimer: Matt Pine’s views are not the views of the Department of Defense nor the U.S. Marine Corps Throughout this decade thus far, the military’s adoption of additive manufacturing (AM)...
U.S. Congress Calls Out 3D Printing in Proposal for Commercial Reserve Manufacturing Network
Last week, the U.S. House of Representatives’ Appropriations Committee moved the FY 2026 defense bill forward to the House floor. Included in the legislation is a $131 million proposal for...