Stepping into the heart of Boston’s innovation landscape, I found myself at Fluent Metal’s headquarters in Cambridge. From the moment I walked through the doors of the startup’s space, the atmosphere was electric with creativity and many prototypes of 3D printers. The air buzzes with innovation, and the founder, Peter Schmitt, embodies the spirit of a modern-day alchemist, turning metal wire into 3D printed components. Fluent Metal’s approach to 3D printing, using liquid metal drops instead of traditional powder, aims to make high-quality metal parts more accessible and affordable, according to Schmitt.

Fluent Metal Co-Founder Peter Schmitt working on a prototype of the metal 3D printer. Image courtesy of Fluent Metal/Andy Ryan.
Under Schmitt’s leadership, Fluent Metal is breaking away from conventional metal additive manufacturing (AM) methods that rely heavily on powder. Schmitt, a former engineer at Desktop Metal from 2015 to 2020, realized the limitations and high costs associated with powder-based metal printing. He envisioned a more efficient, cost-effective solution to democratize metal AM and eliminate the need for expensive clean rooms and explosion-proof facilities. This led to the development of a liquid metal printing process that uses metal wire as thin as human hair, which is melted and jetted in precise droplets to form complex parts.
As I learned during my visit, Fluent Metal’s process involves heating a thin metal wire to create a droplet of molten metal in milliseconds, which is then ejected to form the desired part. Similar to an inkjet printer for metals, “it allows precise placement of metal droplets exactly where needed,” explains Schmitt.
“We wanted to get away from metal powder,” Schmitt remarked, “because we saw a need for a more affordable and user-friendly solution. This drop-on-demand technology ensures that only the required amount of metal is used, drastically cutting down on material waste and energy consumption. By eliminating the need for powder, Fluent Metal’s technology bypasses many safety and regulatory hurdles that plague traditional metal additive manufacturing.”
Schmitt described how his company’s approach offers a clean-room effect without a clean room. Using an inert environment, typically nitrogen, to prevent oxidation, his team can achieve high-quality metal parts in a standard workshop setting. According to the founder, this innovation opens up metal 3D printing to a broader audience, from small businesses to large-scale manufacturers.
Fluent Metal’s technology has vast applications, from aerospace and automotive to jewelry. “The jewelry industry has shown significant interest in our process,” Schmitt noted. They appreciate the cost savings and the ability to create intricate designs without the limitations of powder-based methods.”
Roadmap and Vision
Economic uncertainties are hitting the 3D printing industry hard, slowing investments and creating a cautious market. It feels like a tough time for AM again. 2024 is a make-or-break year for many players in the space. Especially as the pressure to show tangible revenue and solid performance metrics builds up. Those who can adapt and leverage new technologies well will likely become leaders.
Amid these challenges, Schmitt’s enthusiasm for the technology is contagious. Fluent Metal, which came out of stealth mode this year, is still developing its product but has a roadmap that includes scaling this technology to print larger volumes and incorporating multiple metals into a single print. “Our goal is to have a pilot machine ready for customer testing within a year or a year and a half,” Peter mentioned.

Fluent Metal Process Engineering Lead Shashank H R at the startup’s headquarters. Image courtesy of Fluent Metal/Andy Ryan.
The Printer in Action
During my visit, I had the chance to see the firm’s latest printer in action. Schmitt walked me through the Quartz printer, an internal prototype capable of printing a two-inch cube of metal. The simplicity and efficiency of the machine were evident. Fluent Metal’s technology simplifies the manufacturing process and allows for multi-metal printing, a feature that is not very accessible in the broader market. It’s clear how this capability is desirable to industries like jewelry, where precision and material variety are crucial.
One of the standout features of Fluent Metal’s technology is its ability to operate in environments that would typically be unsuitable for traditional metal 3D printing. By avoiding metal powders, which require explosion-proof facilities and strict environmental controls, Fluent Metal can operate in standard settings with minimal safety concerns. This makes the technology not only more affordable but also more accessible to a wider range of industries.
“Fluent Metal’s printers, internally nicknamed after gemstones like Quartz, Ruby, and Emerald, are designed to process a wide range of metals, including precious ones like silver and gold. Switching between different metals easily and even printing with multiple metals simultaneously offers great flexibility,” points out Schmitt.
With a team of six full-time employees and five patents, Fluent Metal says it has more patents in the pipeline and expects to reach 15 to 20 patents once international filings are complete. The core patent focuses on creating and controlling liquid metal droplets, a process borrowed and adapted from the semiconductor industry. This approach is designed to overcome common issues in metal printing, such as the degradation of materials due to chemical reactions and other technical challenges associated with traditional systems.
Schmitt’s vision is clear: to provide a metal AM solution that is accessible and scalable, allowing customers to experiment and innovate without the prohibitive costs associated with powder-based systems. This approach gives Fluent Metal a unique edge in the market.
Fluent Metal’s major competitor is ADDiTEC, which acquired Xerox’s metal additive division. However, Fluent Metal’s unique wire-based approach sets it apart, providing greater flexibility and cost savings.
Innovative Minds at the Helm
Fluent Metal’s team includes recognized industry experts like John Hart, the newly appointed head of MIT’s Department of Mechanical Engineering and co-founder of VulcanForms, and Chris Bangle, a renowned automotive designer formerly with BMW. Schmitt says they “provide invaluable guidance and support. Their collective experience and insights are helping shape Fluent Metal’s path forward, ensuring that the company remains at the forefront of metal additive manufacturing innovation.”
Additionally, they are lucky to have Zach Vader as an advisor. Vader, known for his groundbreaking work in liquid metal 3D printing, co-founded Vader Systems and developed the first commercial liquid metal jet 3D printer, the MK1, which went on to become the basis for Xerox’s metal 3D printing technology. His expertise has been crucial in developing Fluent Metal’s technology, from creating liquid metal droplets to producing high-quality metal parts efficiently.
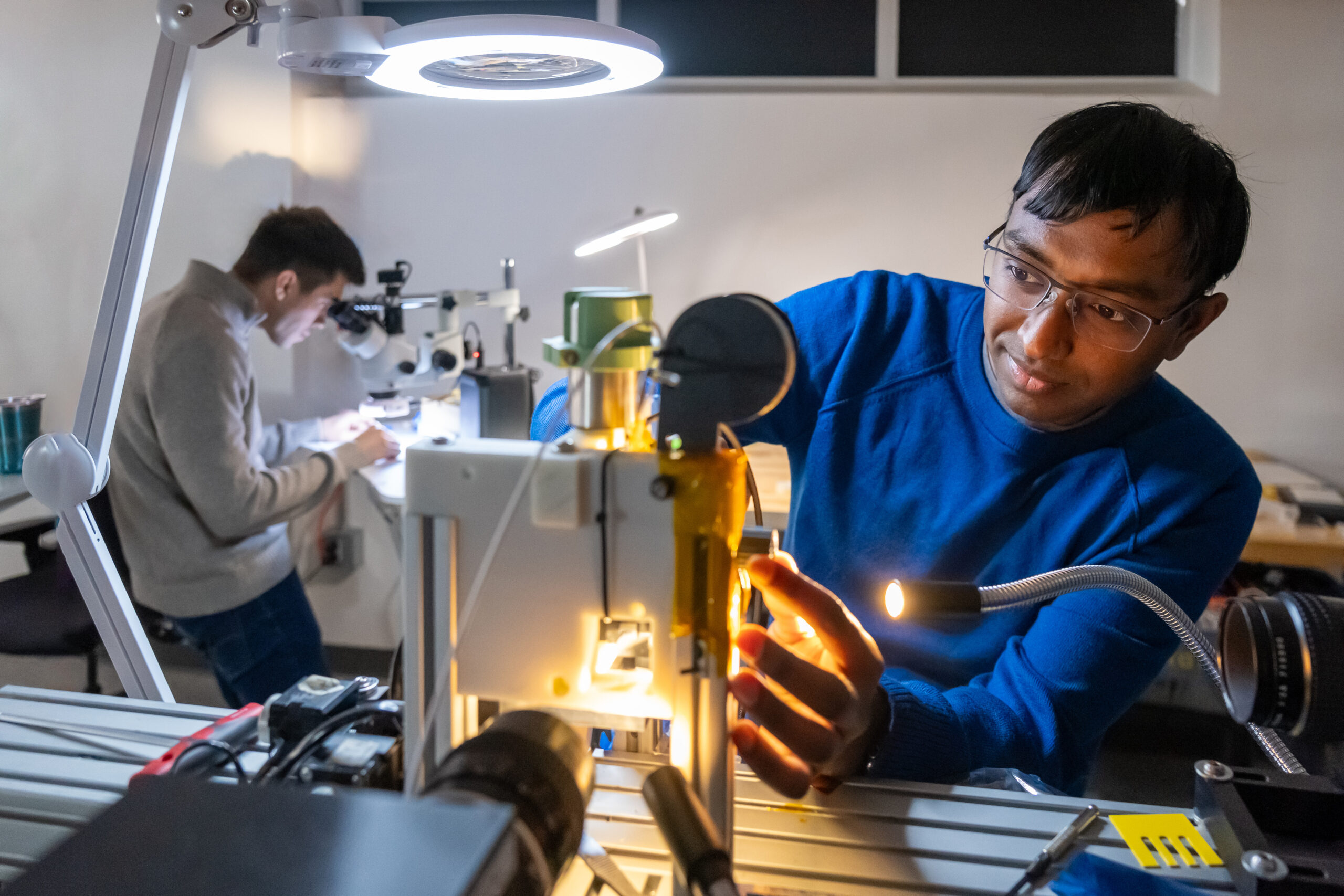
Fluent Metal Process Engineering Lead Shashank H R at the startup’s headquarters. Image courtesy of Fluent Metal/Andy Ryan.
Building on this strong foundation, Schmitt brings a unique blend of creativity and technical expertise to Fluent Metal. With a PhD from the MIT Media Lab and a background in fine arts from Germany, he has always been at the forefront of technological innovation. His journey from designing 3D printed robots to founding Fluent Metal shows his dedication to pushing the boundaries of what is possible. The startup’s location in Cambridge, near MIT and other leading tech firms, gives the company access to plenty of talent and resources. They also benefit from partnerships with Northeastern University, which provides great co-op talent.
My visit to Fluent Metal was nothing short of inspiring. It’s always exciting to see the drive and determination of startups. They show a strong commitment to bringing their ideas to life. As Fluent Metal continues to refine its technology, it’s a breath of fresh air to see such enthusiasm and dedication in metal additive manufacturing.
Subscribe to Our Email Newsletter
Stay up-to-date on all the latest news from the 3D printing industry and receive information and offers from third party vendors.
Print Services
Upload your 3D Models and get them printed quickly and efficiently.
You May Also Like
Consolidation in AM: How 2025 Is Shaping the Industry’s New Normal
The first half of 2025 has been marked by a clear shift in the additive manufacturing (AM) industry. Companies are no longer just focused on developing new tech by themselves....
Etsy Design Rule Change Reduces Selection of 3D Printed Goods
Online marketplace Etsy has implemented a rule change requiring all 3D printed goods on the site to be original designs. The update to the site’s Creativity Standards states, ¨Items produced using...
U.S. Congress Calls Out 3D Printing in Proposal for Commercial Reserve Manufacturing Network
Last week, the U.S. House of Representatives’ Appropriations Committee moved the FY 2026 defense bill forward to the House floor. Included in the legislation is a $131 million proposal for...
Transforming From Tourist to Native: Duro CEO Michael Corr Explains Why the Company Rebuilt its PLM Software on AI
In these early innings of the AI boom, many market analysts have expressed concern that AI spend has gotten too far ahead of the technology’s proven ability to deliver significant...