We’re starting with new materials in today’s 3D Printing News Briefs. Then, we’ll move on to a partnership for aerospace 3D printing, then biomedical 3D printing, and finally a three-story 3D printed structure. Read on for all the details!
Axtra3D Adds Two Functional 3D Systems Materials to Portfolio
Advanced additive manufacturing company Axtra 3D, Inc. has announced the qualification and availability of two functional 3D Systems materials. These are for its Axtra Solutions portfolio and the Lumia X1 printer, powered by the fast HPS print process. First is the Figure 4 PRO-BLK 10, a rigid, production-grade resin with long-term environmental stability and mechanical properties like that of thermoplastic. It features 12% elongation at break and UL94 HB flammability, making it good for tool-less production of connectors, snap-fits, motor housings, and automotive interiors. The second is high-temperature Figure 4 MED-WHT 10, a rigid material that can be sterilized by autoclave. It’s been used by customers for medical devices likes bone-fracture models and surgical drill guides, which require sterilization, thermal resistance, and biocompatibility. Both these materials come with fully dialed process profiles.
“Expanding partnerships with companies like 3D Systems allows us to create a robust material ecosystem, offering the best options in each category for our customers,” said Axtra3D’s Chief Strategy Officer Rajeev Kulkarni. “The Lumia X1 stands out as a highly differentiated and versatile choice, thanks to its innovative hardware and superior materials. This supports both our Axtra Solutions™ and Axtra OpenAccess™ business models, the former provides fully optimized solutions, while the latter caters to customers experimenting with new materials and applications.”
Eplus3D & Paradigm 3D Collaborate for High-Tech Aerospace 3D Printing
Paradigm 3D, the first 3D printing company in the Middle East to obtain Part 21G Certification from the European Union Aviation Safety Agency (EASA) for aerospace part production, is collaborating with Eplus3D and making a strategic investment in its metal AM. Paradigm 3D wanted to gain stronger footing in the market, and realized it needed three things in order to do so: smooth operation, ease of start-up, and compatibility with many metal materials. So they chose Eplus3D’s mid-size EP-M300, which offers a print speed of up to 95 cm³/h and supports a range of materials, including copper, nickel, titanium, and aluminum alloys, cobalt chrome, stainless steel, and more. The printer enabled Paradigm 3D to print a labyrinth cage—in just one piece—in less than one week. This shows the company is committed to meeting the demands of high-tech industries, like aerospace and oil & gas, that require high-quality, reliable spare parts in an efficient timeframe.
“Before we designed the labyrinth cage for control valves in oil and gas industry, it took around six months to produce, and it was very expensive. The design was so complex that the parts had to be made in small strips, which were then stacked and weld together to form the cage,” said Balaj Hassan, the Engineering Manager at Paradigm 3D.
“Internal testing has shown that the results are comparable to the original, as anticipated.”
Spanish Research Center Installs Meltio 3D Printer Prototype
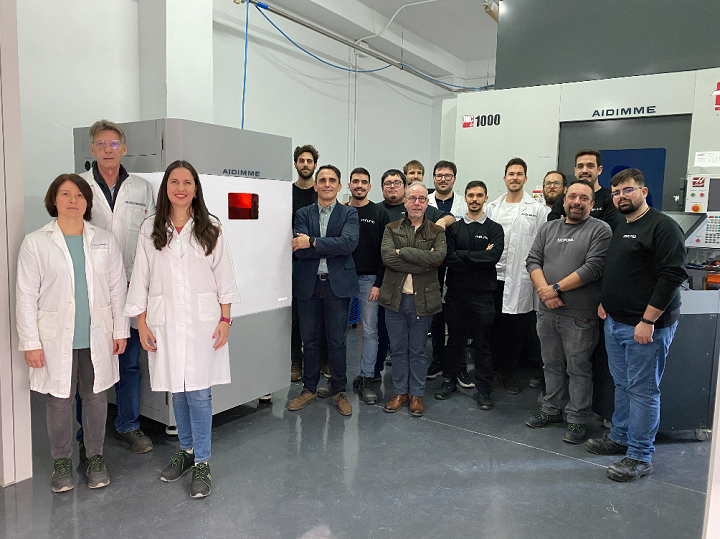
ATILA project members at the installation of the ATILA prototype, technical and research staff from AIDIMME, MELTIO and SICNOVA.
Spanish research center Aidimme installed a Meltio 3D printer prototype as part of the ATILA research project, which is creating biomedical titanium implants using Meltio’s unique wire-LMD technology. The project is formed by a multidisciplinary consortium of different entities, led by Aidimme and including the Hospital General Universitario de Valencia FIHGUV‘s research foundation, the University of Salamanca‘s ALF USAL research group, and Meltio. The goal of ATILA is to investigate various uses and applications of biomedical implants with the Ti64-ELI alloy, 3D printed on the prototype Meltio machine, which uses welding wire. The company says its technology is more efficient than other metal AM processes, and generates less material waste and polluting processes.
According to Meltio, the ATILA project “studies and develops a high protection additive manufacturing process” that’s based on laser wire deposition to process highly reactive metals. Its wire-LMD is a form of DED, and there are advantages to using wire, including lower cost, good deposition rate, high raw material utilization, and lower process contamination than powder bed printing. During melting and deposition of layers in additive manufacturing, oxygen can be “taken up by” metal, like titanium, because of the temperature increase. But the oxygen content can’t exceed the maximum limit listed in the UNE-EN ISO 5832-3:2017 standard for surgical implants made from metallic materials, so the material’s mechanical properties and microstructure must be controlled. So the Meltio prototype installed at Aidimme will enable better control of thermal gradients during printing, so the metallurgy meets the demanding standards that apply to Ti64-ELI.
“First” 3D Printed Three-Story Structure in North America
We’ve seen additive construction companies build 3D printed three-story structures in Germany, India, and Saudi Arabia, but Canadian-based nidus3D claims to have built the first 3D printed three-story structure in North America, using COBOD International technology. Both of these companies have helped to build 3D printed two-story structures in the past as well, so this seems like a logical next step. The 4,500-square-foot townhouse is located in the Toronto area and contains four residential units, along with what might be the world’s first 3D printed basement. At least 50% of residential structures in the U.S. and Canada have two stories, so nidus3D believes it can help meet growing demands during a continuing housing crisis. Plus, 3D printed houses are said to be less expensive, generate less waste and be better for the environment, and even be made to better protect against natural disasters like earthquakes.
Back in 2022, nidus3D founder Hugh Roberts said, “Being able to employ new technology to deliver that housing product more predictably and more economically, at a much higher production rate, is critical to meeting our supply requirements.”
Subscribe to Our Email Newsletter
Stay up-to-date on all the latest news from the 3D printing industry and receive information and offers from third party vendors.
Print Services
Upload your 3D Models and get them printed quickly and efficiently.
You May Also Like
Nikon SLM Solutions Sells SLM 500 to Primary Weapon Systems to Expand Suppressor Production
Primary Weapons Systems (PWS) is a Boise, Idaho-based manufacturer of suppressors, firearms, and related components. A subsidiary of Vigilant Gear and a sister company to aftermarket Glock slide manufacturer Lone...
3DPOD 261: Tooling and Cooling for AM with Jason Murphy, NXC MFG
Jason Murphy´s NXC MFG (Next Chapter Manufacturing) is not a generalist service; instead, the company specializes in making tooling. Using LPBF and binder jet, the company produces some of the...
HP and Firestorm Labs Form Partnership to Use Multi Jet Fusion 3D Printers in Deployable Factories
HP Inc., maker of a range of additive manufacturing (AM) solutions including the Multi Jet Fusion (MJF) ecosystem, has announced a partnership with Firestorm Labs, a developer of containerized, deployable...
3D Printing News Briefs, July 2, 2025: Copper Alloys, Defense Manufacturing, & More
We’re starting off with metals in today’s 3D Printing News Briefs, as Farsoon has unveiled a large-scale AM solution for copper alloys, and Meltio used its wire-laser metal solution to...