We’re kicking things off with business in today’s 3D Printing News Briefs, as Mintek, South Africa’s national mineral research organization, has acquired an AMAZEMET machine. Then we move on to three additive construction stories, before moving on to sustainable resin research, and then research about tiny sensors that can detect flow and environmental changes. Finally, we look at 3D printing in microgravity, and a 3D printed commercial delivery van.
Mintek Acquires AMAZEMET Machine to Support AM in South Africa
After a procurement process that lasted several years, South Africa’s national mineral research organization, Mintek, has finally acquired the rePOWDER ultrasonic atomization and alloy development machine from AMAZEMET, which will be used to support and strengthen the country’s minerals-based and 3D printing industries. Mintek is also in the process of acquiring a metal 3D printer to complement the rePOWDER, and together they will make and test button castings and powders, the former of which can help verify the experimental modeling of novel metal alloys. The machine can process nearly any feedstock material into spherical, homogenous powder particles with excellent flowability. Plus, unlike gas atomizers, this ultrasonic one can manufacture castings, and use small quantities of metals, which is important for R&D efforts that require precious metal resources. Dr. Hein Moller, Mintek’s chief engineer, coordinates South Africa’s precious materials development network, and says that a major challenge is sourcing the material for experimental work, because the metals are so expensive. The rePOWDER can even be used to recycle incorrectly 3D printed parts, re-atomizing them back into a powder.
“We have a very active metal 3D printing community in South Africa, but we don’t have the infrastructure to produce the powders,” Dr. Holler said, noting that it’s important for South Africa not to fall behind in its AM efforts. The AMAZEMET rePOWDER machine will definitely help in this aspect.
3D Concrete Printing & Traditional Architecture Combine in Hexastone
Revealed at Northern Europe’s Nordbau 2023 construction trade exhibit in Germany, the Hexastone project combines traditional architecture with 3D concrete printing (3DCP). The project was a collaboration between Professors Herrmann and Spaeth of the Technische Hochschule Lübeck and additive construction (AC) companies Vertico, and Sika, and the Hexastone dome is made up of 102 interlocking stones, each with a 4.5 meter diameter. A computational form-finding procedure using simulations helped to determine the structural configuration of the shell structure. Its geometry was tessellated into square, hexagonal modules, and the connections between each stone were streamlined using the tessellation method as well. Conventional brickwork creates curvature between bricks with tapered mortar joints, but the hexa-shell does so using an inclined perimeter for each stone, which produces parallel crevices in between them. Vertico said it only took two days of 3D printing to fabricate each of the unique stones with the digitized process.
“Breaking away from the conventional “build and demolish” approach, this pavilion is engineered with the future in mind,” Vertico said in a statement. “After being showcased at the Nordbau 2023, the structure will be disassembled and then reassembled at a location that is yet to be announced. This commitment to “Design for Disassembly” not only reduces waste but also demonstrates a sustainable approach to construction. Since the seams between the stones are only subject to compression forces, the mortar is only used to compensate for tolerances. Therefore, the contact surfaces of the stones are coated with a non-adhesive agent to eliminate the potential transfer of tensile forces and to allow for easier disassembly.”
College Architecture Students Build Inexpensive 3D Printed Home
On the Burbank campus of Woodbury University, you can now find a trendy, environmentally-friendly, and affordable 3D printed home, created by a group of architecture students. The 425-square-foot, open plan property, called the Solar Futures Home, is powered by renewable energy, and was built using sustainable materials. Plus, while the average home in Burbank costs around $1.2 million, this house is less than a quarter of that price, as it only cost the students $250,000 to build it. The house, which was created as part of a national collegiate competition from the Department of Energy, took 24 students about 15 months to build.
Recent graduate Jade Royer said, “I think it looks really nice. I’m glad that we kept it raw concrete… we didn’t add any paints or anything like this on top of it so we can see all of the different layers and the actual material.”
“I also enjoy the kitchen because it uses a lot of sustainable materials as well,” said fellow graduate Jessica Gomez. “The dining chairs and the table are made from recyclable paper, so we try to think sustainably from the building but also with how we wanted to furnish it.”
First 3D Printed Social Housing Project in Europe
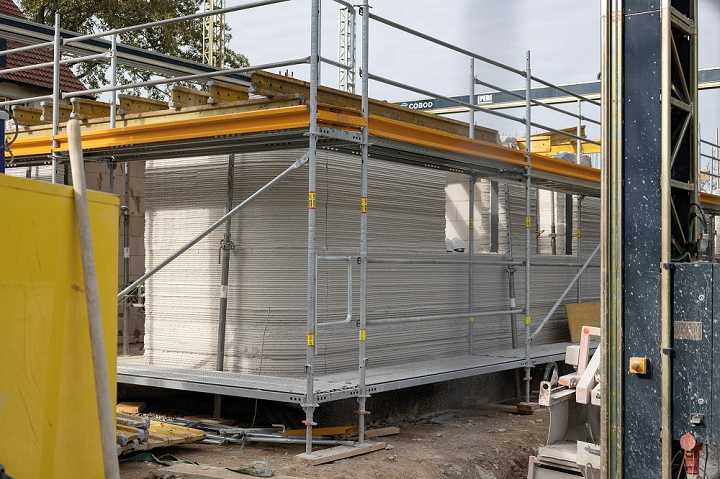
PERI 3D Construction in Germany uses COBOD’s 3D construction printer for the first publicly funded multi-family house.
The first publicly funded multi-family house to be 3D printed in Europe is underway. This social housing project, located in the former coal mining center of Lünen, Germany, combines 3D concrete printing (3DCP) with public housing subsidies to build a three-story apartment building. Each floor will have two units, ranging from 670-890 square feet, for a total of six apartments, and while the first two floors will be 3D printed, the top floor is being built with a timber hybrid construction method. Additionally, conventional construction methods will be used to build the foundation, base, and filigree slabs for the building, and the top floor will be cladded using façade panels. This is the third larger-scale construction project in Germany this year alone that PERI 3D Construction has worked on with COBOD International‘s printers.
“This project continues the trend that we have seen the last coupe of years, where the technology has made some remarkable leaps forward, moving away from just being used for small houses on one floor to also being used for larger and larger projects with multiple floors also outside the residential market,” said Henrik Lund-Nielsen, Founder and General Manager of COBOD International.
“PERI’s German projects in 2023 including the data centre, football clubhouse and now an apartment building are a testament to this trend.”
Penn State Developing Plant-Derived Materials to Replace AM Plastics
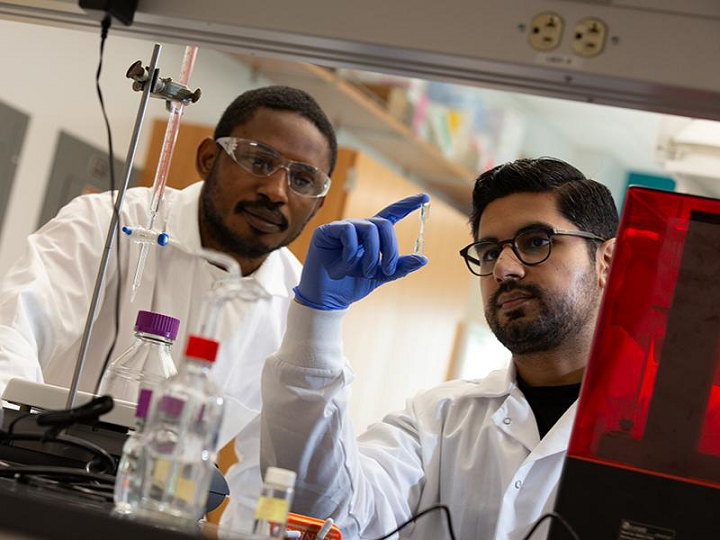
Doctoral degree candidates James Godwin, left, and Kassem Bokhari inspect a 3D-printed tensile-testing specimen. Credit: Michael Houtz/Penn State. All Rights Reserved.
A team of agricultural and biological engineers from Penn State received a three-year, $650,000 grant from the U.S. Department of Agriculture’s National Institute of Food and Agriculture (USDA NIFA) to develop a sustainable, plant-derived material that could replace the plastics often used in large-format stereolithography, or SLA 3D printing. They’ll work to develop chemical transformations of the plant-derived biomaterials nanocellulose and lignin for the creation of renewable SLA resins that also contain soybean oil. Then, these materials can hopefully be used as a substitute for costly, highly-engineered resins that are mixed from petrochemical components.
“Our project team’s long-term goal is to develop new and sustainable bioproducts from lignocellulosic biomass — or dry plant matter — that economically enable a low-carbon bioeconomy. The objective of this proposal, which is a step toward our long-term goal, is to create a renewable resin material comprised of agriculturally derived components that will enable large-format 3D printing by stereolithography,” explained team leader Stephen Chmely, assistant professor of agricultural and biological engineering in the College of Agricultural Sciences.
Virginia Commonwealth University Researchers 3D Printing Cilia Sensors
Nanoscience and nanotechnology doctoral candidate Phillip Glass, and his advisor Daeha Joung, PhD, from the Virginia Commonwealth University Department of Physics, were inspired by tiny hair-like cilia, and their ability to boost a person’s senses and detect subtle environmental changes, in their work on mechanosensing: methods the body uses to collect external stimuli, like light, temperature, or movement, and send it to the brain. Mechanoreceptors are the organs or cells performing the sensing, and the duo is applying 3D printing to the idea to create tiny sensors that look like hairs and could be used for applications like minimally-invasive surgical robots, industrial machines that measure air or water flow, and even a robot that can read braille. A customized 3D printer was used to create the sensors out of polycaprolactone (PCL) mixed with conductive graphene, and the flexibility of the technology allows for the easy creation of differently-sized sensors.
“One of the huge selling points of our technology is that we can print different-sized hairs, which can feel the stimulus differently. Really long hairs bend more easily than short ones, so while other types of airflow sensors can only detect a single range of flow, we can print our cilia in different sizes and spacings and make them more sensitive to a wide range of stimuli,” said Glass.
You can learn more in their published research article.
3D Printing in Microgravity to Advance Space Colonization
It’s necessary to manufacture important equipment and materials onsite when you’re on an extended outer space mission, because it’s so time-consuming, heavy, and expensive to transport the items from Earth. The Microgravity Research Team from West Virginia University is exploring how 3D printing in a weightless environment could help advance and support long-term space habitation and exploration. Their recent focus has been how microgravity affects 3D printed titania foam, which has great potential for applications like water purification and blocking ultraviolet (UV) radiation. The work allows them to see the role gravity plays in how the foam is extruded out of the nozzle and spreads onto a substrate, and they also experiment with changing other variables in the print process, such as extrusion pressure and writing speed, to see how all the parameters interact to tune the filament’s shape in a weightless environment.
“Transporting even a kilogram of material in space is expensive and storage is limited, so we’re looking into what is called ‘in-situ resource utilization. We know the moon contains deposits of minerals very similar to the titanium dioxide used to make our foam, so the idea is you don’t have to transport equipment from here to space because we can mine those resources on the moon and print the equipment that’s necessary for a mission,” explained co-author Konstantinos Sierros, associate professor and associate chair for research in the Department of Mechanical and Aerospace Engineering, who’s overseen the Microgravity Research Team’s titania foam studies since 2016.
You can learn more in their published research article.
3D Printed Electric Delivery Van First in Range of Commercial Vehicles
Finally, British sustainable mobility company HELIXX announced its first demonstrator vehicle, which is to be the first in a full range of commercial vehicles. The all-electric delivery van, with an aim to “support sustainable economic development in emerging megacities,” uses 3D printing for all of its cosmetic and structural body parts. According to TopGear, the idea is to build the van in local flat pack “mobility hubs” around the globe, because the body only features five key parts that simply “click and bond” together, without any welding required. HELIXX believes this will simplify the vehicle manufacturing process by up to 50%.
This 3D printed commercial delivery van is a single-seater vehicle with a central driving position, and measures only 3.2 meters long and 1.5 meters wide, but it has a 500 kg payload and 1,200 liters of space in the back; with a 140 cm long load bay and 110 cm wide rear door, a shipping pallet can easily fit inside. Starting with this delivery van, HELIXX is planning to develop a whole range of commercial vehicles, including a pickup truck, closed-body taxi with back seats, and an open-bodied rickshaw vehicle. Production for the van is set to begin in 2024, with a run of 100 vehicles built in the UK.
Subscribe to Our Email Newsletter
Stay up-to-date on all the latest news from the 3D printing industry and receive information and offers from third party vendors.
Print Services
Upload your 3D Models and get them printed quickly and efficiently.
You May Also Like
Printing Money Episode 30: Q1 2025 Public 3D Printing Earnings Review with Troy Jensen, Cantor Fitzgerald
Printing Money is back with Episode 30, and it’s that quarterly time, so we are happy and thankful to welcome back Troy Jensen (Managing Director, Cantor Fitzgerald) to review the...
3DPOD 260: John Hart on VulcanForms, MIT, Desktop Metal and More
John Hart is a Professor at MIT; he´s also the director of the Laboratory for Manufacturing and Productivity as well as the director of the Center for Advanced Production Technologies....
Etsy Design Rule Change Reduces Selection of 3D Printed Goods
Online marketplace Etsy has implemented a rule change requiring all 3D printed goods on the site to be original designs. The update to the site’s Creativity Standards states, ¨Items produced using...
3DPOD 259: AM at Stratasys with Rich Garrity, Chief Business Unit Officer
Rich Garrity is the Chief Business Officer of Stratasys. Rich shares Stratasys´ vision and future with us. We talk about machines, applications, clients, and the market in general. What technologies...