Additive manufacturing (AM) and more specifically, direct metal laser sintering (DMLS) technology has brought unprecedented design freedom and application complexity to metal manufacturing. It has enabled the creation of complex, high-precision parts with often considerably shorter lead times than traditional means like welding or CNC machining. DMLS, a type of AM, uses high-powered lasers to melt and fuse powdered metal, layer by layer, to achieve detailed and intricate geometries. Leveraging metal 3D printing can unlock a variety of new strategies and part designs for your part production, but still requires post-processing due to the use of support structures and possible rough surfaces from the printing process. Let’s dive into what it takes to successfully post-process an AM part and what processes are best for the 3D printing process.
Heat Treatment and Stress Relief
Heat treatment is often necessary to relieve internal stresses induced during the 3D printing process. Heat treatment can be done with standard industrial furnaces or hot isostatic pressing (HIP) to enhance the mechanical properties and dimensional stability of the part. This is also a post-processing procedure that is performed before the removal of supports. Standard heat treatments often require heating the parts up to a high enough temperature where the material “relaxes”, then cooling it down, sometimes rapidly by dunking in water or oil, potentially with multiple steps to reach the final results. HIP, on the other hand, applies high pressure and temperature simultaneously to eliminate porosity while achieving the desired metallurgical results. The choice of heat treatment depends on the material used and the desired final properties, ensuring that the part meets the stringent performance requirements of its final application.

Demonstration application of Al5X1 material that has been heat treated and anodized for both cosmetic coloring and corrosion resistance protective properties.
Support Structure Removal
During the metal 3D printing process, support structures are crucial to prevent warping and distortion, especially in overhanging areas. However, these supports must be carefully removed once printing is complete. Common removal techniques include wire electrical discharge machining (EDM), milling, and grinding, or even using common hand tools. Each method demands precision to avoid damaging the part and to maintain dimensional accuracy. Proper support removal ensures that the part retains its designed shape and structural integrity, paving the way for subsequent post-processing steps. In the end, best strategy for support is to design it out. Support adds additional build time, requires post-processing time, and consumes extra material, so if there is an opportunity to modify the part according to Design for AM principles, it is favorable.
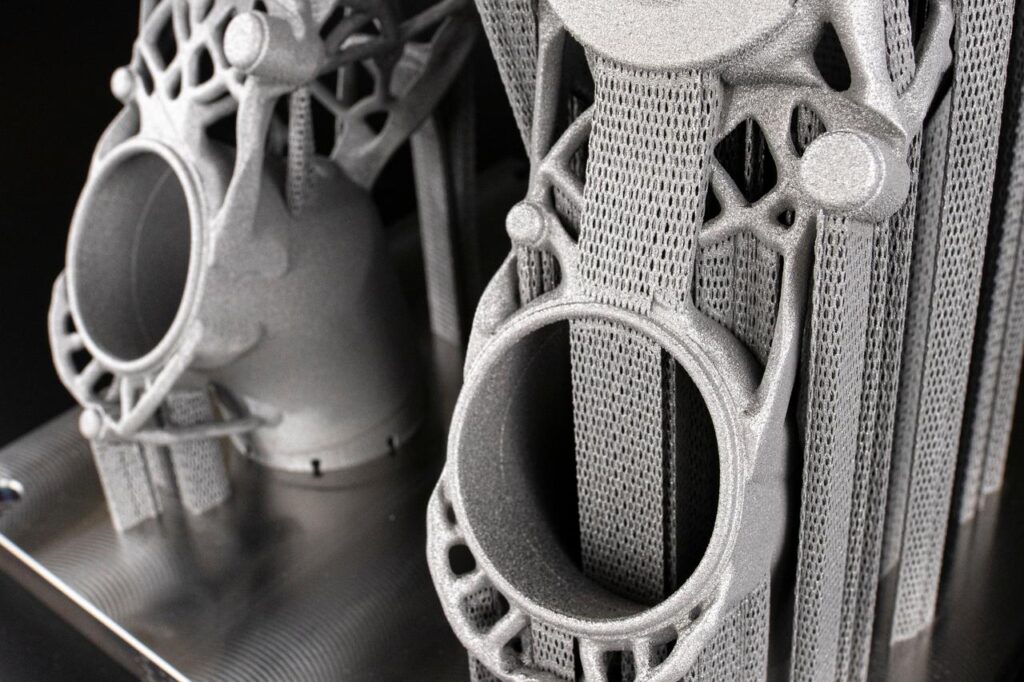
Example AM Metals Bracket built with support structures
Surface Finishing Techniques
After heat treatment and stress relief, and support structure removal, a part may be functionally ready, but can also require a final step to smooth any rough edges or surfaces left by the support structures. This is called surface finishing – it enhances the appearance, functionality, and overall quality of the metal 3D printed parts. Here are few examples of surface finishing techniques:
Media Blasting/ Shot Peening: This involves bombarding the part with medias such as organics, oxides, ceramic beads, or steel shot to smooth rough edges and improve surface uniformity. Each type of media creates a different surface finish. Organic grit, like corn husks or walnut shells are used to simply remove additional powder on the surface without changing the surface texture. Abrasive grits, like sand or aluminum oxide, remove material from the surface and impart a matte finish. Steel shot will compact the surface, leaving a shinier finish while also helping to improve the strength of the part by creating a compressive strain on the surface. This can be done with a post-processing system like a shot-blasting cabinet within a production facility.
Polishing: A more refined technique that uses abrasive materials to achieve a mirror-like finish, essential for applications demanding high aesthetics or low friction surfaces. If the part will be visible in the end-use application, this brings a more professional look and feel to the component. In critical applications, having a smooth, polished surface can even extend its life as well.
Chemical Etching: This method uses chemical solutions to remove material at a microscopic level, providing a precise and controlled finish that is ideal for intricate designs.
For instance, medical implants often require extremely smooth surfaces to minimize bacterial growth and enhance biocompatibility, making polishing and chemical etching preferred choices.
Machining: In the additive world, we often refer to machining as “traditional manufacturing.” It consists of mills or lathes or other machines that use a cutter to physically remove material from a surface. In many production scenarios, machining is a critical part of the process. Any mating features, like hinges, sealing grooves, or tight fits, will generally require a machining operation to reach the surface quality and tolerances necessary to ensure proper performance. While AM can create amazingly complex structures, it is important to consider the overall system that the AM part will be integrated into and make sure that there are appropriate clearances to do all the necessary machining to make it work.
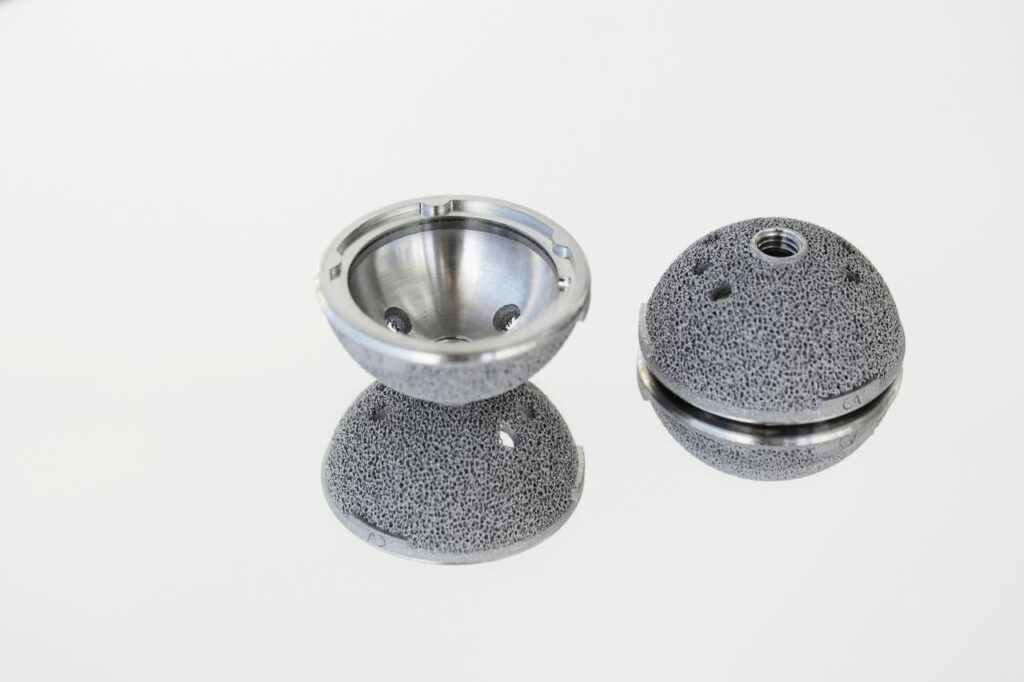
Example of the different surface finishes that can be achieved through post-processing and targeted to different areas of an application such as this acetabular cup implant.
Inspection and Qualification
Metal 3D printing is being leveraged more and more in critical part production for the aerospace, medical, and energy sectors. A robust inspection and quality assurance framework is necessary to ensure part accuracy, material properties, and overall performance.
Non-Destructive Testing (NDT) techniques like X-ray computed tomography (CT) and ultrasonic testing allow for the identification of internal defects or porosity without damaging the part. These methods provide detailed insights into the internal structure, confirming there are no hidden flaws that could compromise performance of the part when performing its high-intensity job within the complete product.
Destructive testing methods such as tensile testing and hardness testing involve subjecting parts to controlled stress or deformation to assess their mechanical properties. Although these tests destroy the sample, they provide invaluable data on the material’s strength, ductility, and toughness and measure the amount of strain that can be put on a part before it begins to fail. The qualification of parts additively manufactured is done by showcasing the statistical equivalence based on testing of many randomly selected parts across multiple builds and powder lots. In other words, it confirms that even if the batch of material, the system, and the batch of parts changes, the quality of the produced part remains the same. Creating an internal system to standardize the production process of additively manufactured parts is important for production in all metal 3D printing.
- Additional medical application production images that show the use of support-free strategy and are end-use hip implants made manufactured with industrial 3D printing.
Advancing Your Metal 3D Printing Production
Post-processing and quality control are vital steps in the metal AM workflow, transforming raw 3D printed parts into high-quality, functional products. By meticulously addressing heat treatment, support structure removal, surface finishing, and employing rigorous inspection methods, manufacturers can ensure their 3D printed parts meet stringent specifications and performance criteria. As AM continues to evolve, these post-processing techniques will play an increasingly important role in unlocking the full potential of 3D printed metal components. To learn more about quality assurance testing and metal post-processing, read about EOS’ in-depth qualification process with the help of Additive Minds consulting.
Subscribe to Our Email Newsletter
Stay up-to-date on all the latest news from the 3D printing industry and receive information and offers from third party vendors.
Print Services
Upload your 3D Models and get them printed quickly and efficiently.
You May Also Like
U.S. Navy Lab Uses 3D Printing to Reduce Tooling Lead Time By Over 90%
The F-35 Lightning II Joint Program Office (JPO), responsible for life-cycle management of the key fifth-generation joint strike fighter (JSF) system used by the U.S., its allies, and its partners,...
Etsy Design Rule Change Reduces Selection of 3D Printed Goods
Online marketplace Etsy has implemented a rule change requiring all 3D printed goods on the site to be original designs. The update to the site’s Creativity Standards states, ¨Items produced using...
Honeywell Qualifies 6K Additive’s Nickel 718 for 3D Printed Aerospace & Defense Parts
6K Additive is renowned for manufacturing sustainable additive manufacturing (AM) powder, and offers a wide portfolio of premium metal and alloy powders that include titanium, copper, stainless steel, and nickel,...
MetalWorm Sells WAAM Systems to Research Institutes in Brazil and Malaysia
Turkish WAAM firm MetalWorm has sold a system in Malaysia and another in Brazil. This is an excellent example of a few emerging trends in additive. Firstly, WAAM was experimented...