All the Moving Pieces: Nexa3D’s Chief Government Officer Elisa Teipel Explains 3D Printing’s Role in Logistics
Right as Formnext 2023 was getting started, Nexa3D announced its acquisition of Essentium, a deal that officially went through earlier this month. The two companies have hit the ground running as a combined force, with Elisa Teipel, formerly the Chief Technology Officer (CTO) at Essentium, now serving as the Chief Government Officer (CGO) at Nexa3D.
At the time of my interview with Teipel, 2024 was just over a couple of weeks old, but both Nexa3D and Essentium have already had a busy year, and not just because of the acquisition. Essentium was also the main sponsor for the Military Additive Manufacturing (MilAM) Summit in Tampa, FL, where Teipel was the keynote speaker.

I write about the US military’s use of AM quite frequently, so I think often about one particular operational advantage that can be supported by 3D printing, which is key to the MilAM Summit: sustainment and readiness. The ability to keep in-house as much of the supply chain as possible for a given component epitomizes why the military’s interest in AM is growing at a seemingly exponential rate:
“AM is really poised to help in the defense and military space because you can problem solve right at the point of need,” Teipel said. “Logistics can make or break success on the battlefield. That has been the case in wars throughout history, and we can see it unfolding in real time everywhere that there’s ongoing conflict and hardship in the world today. This is what makes defense one of the sectors where AM is in highest demand. It’s always striking to see how many innovations are continuously happening right on the frontlines.
“Different Essentium High Speed Extrusion platforms are being used overseas for example in Ukraine. We are seeing Additive Manufacturing used more and more at the frontlines. The bigger question, long-term, is how do we grow it? That will take some policy changes and organizational adjustment, and at the end of the day, people always have reservations when there’s a new method of doing things. But, generally speaking, I think military users are seeing that additive really can solve problems at the point of need, and it can solve those problems fairly quickly in many cases.”
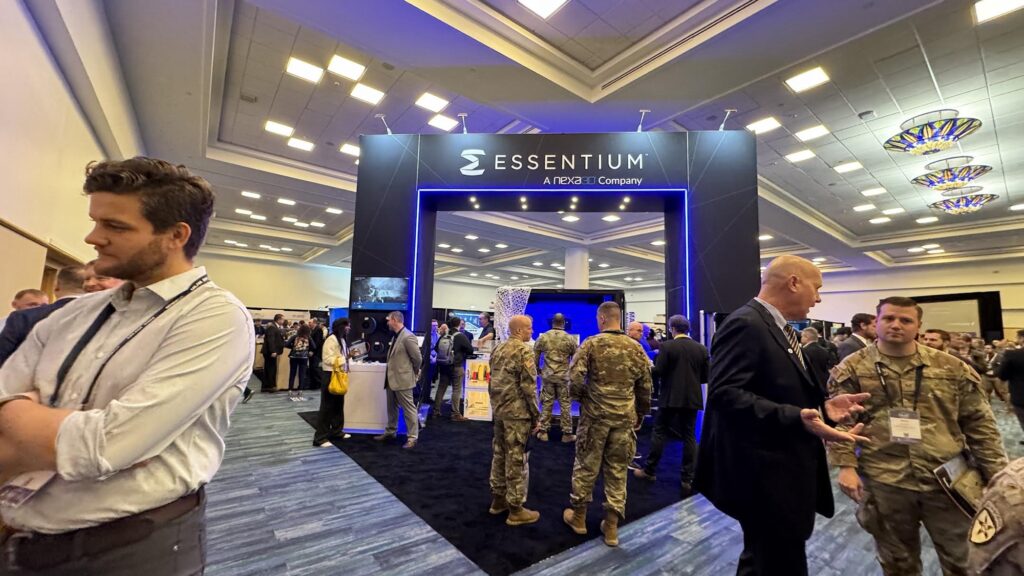
According to Teipel, that consideration of enabling decision-making on the frontlines was one of the topics from MilAM that stood out most strikingly:
“Whenever someone is talking about using additive in a situation where it hasn’t been used before, the decision about whether or not to do so usually comes down to the extent to which the new application has to be tested,” Teipel explained. “From the OEM’s standpoint, we have to make sure that it’s going to work, which requires substantial amounts of data. On the frontline, they need the data to be able to make sound leadership decisions.”
“There is a tendency to want to make sure everything is perfect. But we also need to be able to provide the data to a military commander, for instance, in a context of, how material or technology can be used. We need to establish a difference between the attitudes toward AM applications in emergency situations versus those about the technology’s use in the long-term, and strike a balance between the two.”
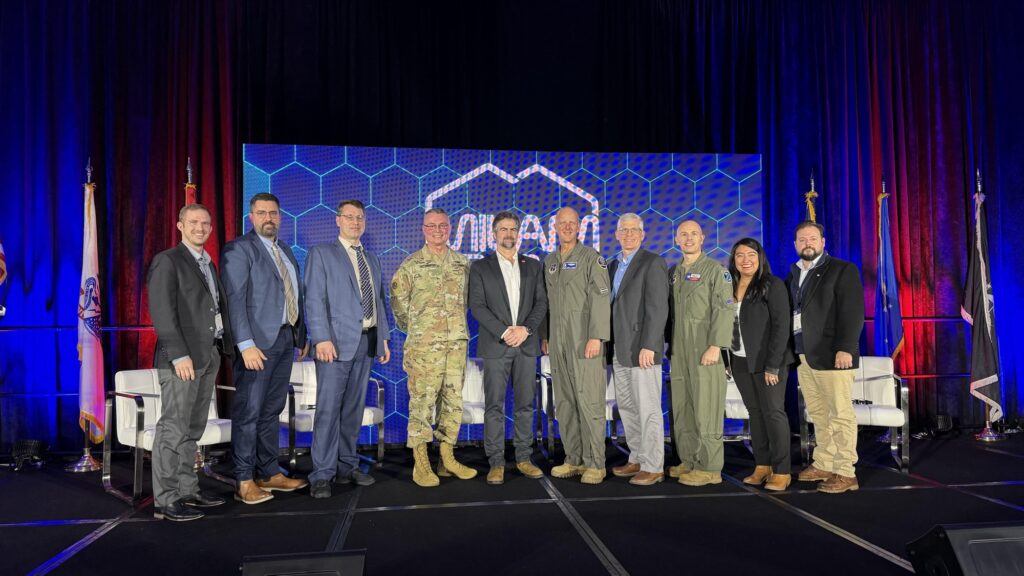
Indeed, the military’s unique demand for and capacity to test new technologies on the fly is precisely what has made the US armed forces such a pivotal factor historically as an early adopter of cutting-edge technologies. At the same time, of course, to make the biggest impact, those gains from “learning by doing” eventually need to become permanently embedded into the military’s routine operations. Teipel noted that MilAM provided reasons to be optimistic on that front, as well:
“Overall, I see a steady continuation of growing interest in AM each year and I think that’s going to be sustainable over the long haul. And that’s what I love about working with the military: progress in the AM industry can seem slow sometimes which can be frustrating. But if that kind of growth is done methodically — a strong suit of military customers — the positive results are more lasting and in turn, more sustainable, because it’s growth that remains independent of any kind of hype bubble.
“In that sense, it’s also important to remember that AM is used not just on the battlefield, on the frontlines, but in sustainment, as well. And once you’re using it for sustainment, that’s when you’re really able to reduce costs, which means eventually, the taxpayer dollars that are saved can go towards other things.”
While those other things don’t have to be AM-related, Teipel nonetheless pointed out other examples that are, which fit the same mold of enhancing the military’s logistical cohesion, but in non-combat contexts:
“The other piece is the humanitarian side,” she said. “AM can provide a huge boost to humanitarian relief efforts. I remember when we had a cold front here in Texas a few years back, we showed how we could 3D print some cleats for the National Guard that could help them get around on the ice when they were providing disaster relief. You can print funnels for hurricane relief, for filling sandbags. Parts that, under normal circumstances, you might consider trivial, but they’re things that can really make a difference. Those parts seem trivial — until a crisis happens that teaches you they’re not.”
And, despite the growing number of crises in the world, MilAM left Teipel more optimistic than ever about the prospects for the AM industry:
“I’ve found myself saying this expression a lot, lately: the best is yet to come,” concluded Teipel. “And I truly believe it, because what we’ve been able to accomplish with the combination of Nexa3D and Essentium is a full coming-together of different technologies under the same roof, which means we can problem-solve together and serve our customers more effectively. It’s still only January, but when I think about the horizon for 2024 and beyond, I see potential that feels almost limitless. And that’s an exciting feeling to have.”
Images courtesy of Essentium, a Nexa3D company.
Subscribe to Our Email Newsletter
Stay up-to-date on all the latest news from the 3D printing industry and receive information and offers from third party vendors.
Print Services
Upload your 3D Models and get them printed quickly and efficiently.
You May Also Like
Making 3D Printing Personal: How Faraz Faruqi Is Rethinking Digital Design at MIT CSAIL
What if your 3D printer could think more like an intelligent assistant, able to reason through a design idea, ask questions, and deliver something that works exactly the way the...
Reinventing Reindustrialization: Why NAVWAR Project Manager Spencer Koroly Invented a Made-in-America 3D Printer
It has become virtually impossible to regularly follow additive manufacturing (AM) industry news and not stumble across the term “defense industrial base” (DIB), a concept encompassing all the many diverse...
Heating Up: 3D Systems’ Scott Green Discusses 3D Printing’s Potential in the Data Center Industry
The relentless rise of NVIDIA, the steadily increasing pledges of major private and public investments in national infrastructure projects around the world, and the general cultural obsession with AI have...
Formlabs Teams Up with DMG MORI in Japan
In late June, Nick Graham, Chief Revenue Officer at Formlabs, announced on LinkedIn that the company had partnered with DMG MORI, one of the world’s leading machine tool companies, to...