Moving from a Closed Material Ecosystem to Open Materials: Increasing AM Adoption in Production and Unleashing Innovation
Remember those old ink cartridges that cost more than the printer itself? The 3D printing industry has long held onto a similar “razor-razor blade” model, where a significant portion of the OEM’s profits came from proprietary materials sales. In recent years, we’re seeing a paradigm shift occurring as more companies enable open materials.
As 3D printing graduates from prototyping playgrounds to production floors, becoming additive *manufacturing*, the much-higher material volume of production environments puts a much greater emphasis on material costs, costs that today are often a barrier to wider adoption of AM in these high-volume settings.
In addition, the closed ecosystem restricts creativity, denying users access to a universe of potential materials beyond the manufacturer’s curated offering. Engineers and designers crave access to specialized materials with specific properties – conductive filaments for printed electronics, biocompatible resins for medical devices, or high-performance thermoplastics for aerospace applications. Opening printers for material developers significantly accelerates the pace of innovation.
With that in mind, what impact will ‘open materials’ have on the OEMs?
Let’s take Stratasys, the AM market leader: Materials are ~35% of Stratasys’ revenues (>$200M annually) and are estimated to be >40% of its gross profit (~$100-120M). As Stratasys is starting to offer ‘open materials’ on select printers, there is a concern about a negative impact to its profitability. Stratasys is already not profitable, with an operating margin of ($73M) in the last 12 months (TTM). Can it afford to take this ‘hit’? Or on the flip side, will open materials drive enough additional printer sales to compensate, and perhaps even reduce some of its R&D spend ($88M in TTM, of which a large portion is likely devoted to materials development)?
The main ‘upsides’ from open materials are:
- Higher machine sales in production environments: While production environments put more pressure on prices, these are more likely to purchase multiple printers.
- Machine sales to research customers who want to develop new materials; which in turn might yield additional machine sales, driven by these materials.
- “Indirect” material revenues, e.g. by taking a cut off “certified” materials of 3rd party material vendors.
- Revenues from open materials licenses: For example, Stratasys sells its open materials license for the FDM Fortus 450 printer for ~$12K annually (or ~$80K for a perpetual license).
- New revenue streams from materials development and testing services.
Is that enough to compensate for the decline in the materials revenue stream, a stream that is – important to stress – recurring, more stable and certainly more ‘recession proof’ than printer revenues?
The key is likely to not give up on the materials revenue stream altogether, but compromise on the margins by offering more attractive materials pricing to keep the customers buying from the OEM, especially for high-volume customers (e.g. offer volume discounts); and in addition, leverage ‘open materials’ to create specialized materials that otherwise would have taken the OEM significantly longer time to develop, if at all.
That said, the legacy AM OEMs, such as Stratasys and 3D Systems, are likely to experience at least a short term negative impact by enabling ‘open materials’ either way, which will likely manifest in their share prices.
By contrast, emerging OEMs, especially those targeting industrial settings ‘off the bat’, are exempt from the ‘self-disruption’ concern and are planning their business models in accordance with these production environments.
Let’s take Tritone, an Israel-based metal AM company, as an example. Tritone, which has a sinter-based technology targeting high-volume production of metal and ceramics parts, is heavily focused on production environments. The company does sell materials directly – materials tested and qualified on its printers – while in parallel also selectively working with customers on specialized materials development.
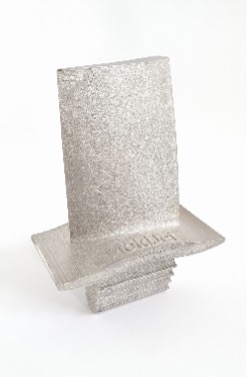
Parts made by Fraunhofer using Tritone printers with Inconel 713C. Photo source: https://www.linkedin.com/feed/update/urn:li:activity:7135160440484962305/
Fraunhofer IFAM, Germany’s leading research institution, with collaboration from MIMplus, has used Tritone’s printer to develop its Inconel 713C metal paste, a material used in applications such as aerospace turbine blades, gas turbines and reactor vessels. Tying into the previously-mentioned ‘upsides’, this material could potentially drive Tritone sales in aerospace, power generation and chemical processing industries, creating a “win-win” situation.
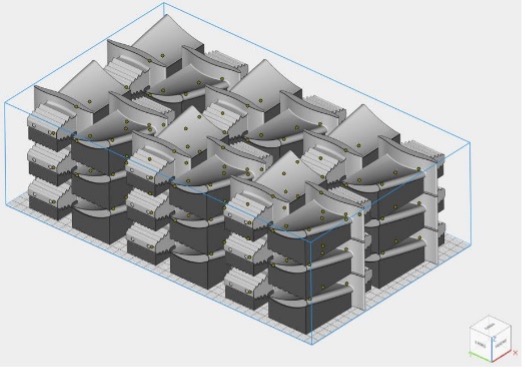
Parts made by Fraunhofer using Tritone printers with Inconel 713C. Photo source: https://www.linkedin.com/feed/update/urn:li:activity:7135160440484962305/
To summarize, open materials are important for the AM industry to drive wider adoption in industrial setting, as an outcome of reduced material prices (competition-driven) and/or as an outcome of accelerated material innovation, allowing more applications.
The legacy companies will likely struggle to manage the short-term financial hit and will be more cautious, while the emerging players for this from the get-go and position themselves well with production customers.
Feature image: Parts made by Fraunhofer using Tritone printers with Inconel 713C. Photo source: https://www.linkedin.com/feed/update/urn:li:activity:7135160440484962305/
Startup advisor Tali Rosman will be participating at the upcoming Additive Manufacturing Strategies business summit in New York, February 6 to 8, 2024. Rosman will be moderating “Panel 2: Workflow Software for AM.”
Subscribe to Our Email Newsletter
Stay up-to-date on all the latest news from the 3D printing industry and receive information and offers from third party vendors.
Print Services
Upload your 3D Models and get them printed quickly and efficiently.
You May Also Like
Reinventing Reindustrialization: Why NAVWAR Project Manager Spencer Koroly Invented a Made-in-America 3D Printer
It has become virtually impossible to regularly follow additive manufacturing (AM) industry news and not stumble across the term “defense industrial base” (DIB), a concept encompassing all the many diverse...
Inside The Barnes Global Advisors’ Vision for a Stronger AM Ecosystem
As additive manufacturing (AM) continues to revolutionize the industrial landscape, Pittsburgh-based consultancy The Barnes Global Advisors (TBGA) is helping shape what that future looks like. As the largest independent AM...
Ruggedized: How USMC Innovation Officer Matt Pine Navigates 3D Printing in the Military
Disclaimer: Matt Pine’s views are not the views of the Department of Defense nor the U.S. Marine Corps Throughout this decade thus far, the military’s adoption of additive manufacturing (AM)...
U.S. Congress Calls Out 3D Printing in Proposal for Commercial Reserve Manufacturing Network
Last week, the U.S. House of Representatives’ Appropriations Committee moved the FY 2026 defense bill forward to the House floor. Included in the legislation is a $131 million proposal for...