Fused filament fabrication (FFF) is a popular additive manufacturing (AM) process that relies on a heated nozzle to melt and deposit thermoplastic filament layer by layer to create a 3D object. It is a versatile and cost-effective technology that can be used for a wide range of applications, from prototyping to production manufacturing.
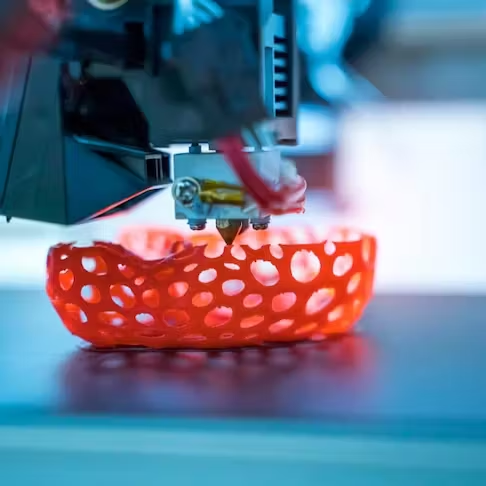
Image courtesy of Xometry
Reasons to Choose FFF 3D Printing
- Affordability: FFF 3D printers are relatively inexpensive to purchase and operate, making them a good option for businesses of all sizes. Prices can range from just a couple hundred dollars to tens of thousands, depending on the exact quality and applications required.
- Wide range of materials: These systems can work with a variety of thermoplastic materials, including ABS, PLA, Nylon, and Polycarbonate and much more. This gives users the flexibility to choose the right material for their specific needs.
- Design freedom: FFF 3D printing allows enterprises to create complex geometries that would be difficult or impossible to produce using traditional manufacturing methods. Water-soluble filament in a dual extruder can be used to make support structures that can be washed away post-print, opening design possibilities even further
- Rapid prototyping: Filament-based technology can quickly produce prototypes for new products, which can help businesses to accelerate their product development cycle and time-to-market.
- On-demand manufacturing: FFF 3D printing can be used to produce parts on-demand, which can help businesses to reduce inventory costs and lead times.
Other FFF Options
- Metal FFF: Metal FFF printers rely on metal-infused filaments to produce metal parts that are then sintered in a furnace to achieve full density. Metal FFF components are typically stronger and more durable than plastic, but they can also be more expensive to produce due to post-print sintering.
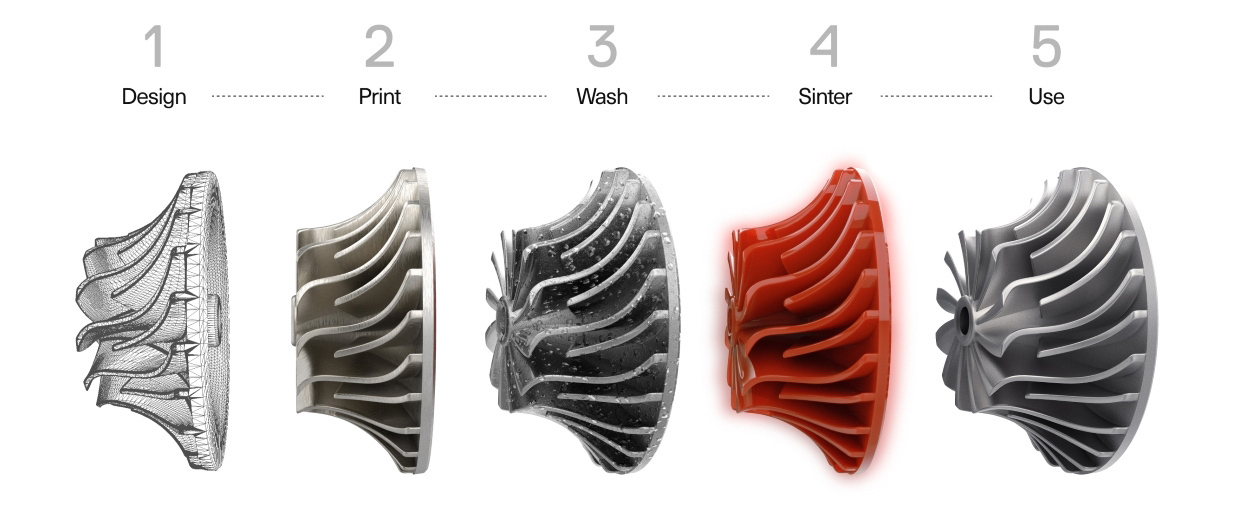
Image courtesy of Markforged – Showcasing the process of a metal FFF part
- Continuous fiber-reinforced FFF: Fiber-reinforced FFF printers deposit filament in conjunction with continuous fiber strands, such as carbon,glass fiber, and kevlar to produce parts that are stronger and stiffer than traditional FFF components.
The image uses Kevlar to highlight the continuous fiber reinforcement, making it easier to distinguish from the regular printed part. Both metal and fiber-reinforced components are stronger than traditional FFF parts, making them ideal for applications where high strength are required. Whereas metal filament results in overall increased durability, most fiber-reinforced items may demonstrate enhanced stiffness.
Applications for FFF 3D Printing in Business
FFF 3D printing can be leveraged for a wide range of applications in business, including:
- Prototyping: Due to its low cost, filament-based 3D printing may be preferred for prototyping compared to other AM techniques.
- Manufacturing: With FFF, it’s possible to manufacture a variety of products, including custom components, tooling, and jigs. Due to the rapid improvement in FFF printing accuracy and quality, parts can now be printed in end-use, customer-facing applications. In turn, businesses may be able to reduce their manufacturing costs and improve their efficiency.
- Repair and maintenance: FFF 3D printing can be used to repair or replace damaged parts on equipment and machinery, thus reducing downtime and improving productivity.
Conclusion
FFF 3D printing is a versatile and cost-effective technology that can be used for a wide range of applications in business. It is a good option for enterprises of all sizes that are looking to accelerate product development cycles, reduce manufacturing costs, or improve efficiency. With its affordability, wide range of materials, design freedom, and rapid prototyping capabilities, FFF 3D printing can help nearly any user to achieve their goals.
Feature image courtesy of the Virtual Foundry.
Subscribe to Our Email Newsletter
Stay up-to-date on all the latest news from the 3D printing industry and receive information and offers from third party vendors.
Print Services
Upload your 3D Models and get them printed quickly and efficiently.
You May Also Like
Johns Hopkins University Researchers Develop HyFAM Technology
Two scientists from Johns Hopkins University, Nathan C. Brown and Jochen Mueller, have developed a hybrid manufacturing technology they call HyFam, or Hybrid Formative Additive Manufacturing. Their work on this technology...
3D Printing G-Code Gets an Upgrade: T-Code
Good old G-Code still manages many 3D printers, great and small. Just like the STL, it’s a standard that enables collaboration while also holding the additive manufacturing (AM) industry back....
AM Rewind: The Biggest News and Trends of 2024
After a sluggish 2023, driven by persistent inflation and geopolitical tensions, 2024 has seen some recovery. Economic growth climbed from about 2.8 percent in 2023 to a modest 3.2 percent...
Metal Wire 3D Printer OEM ValCUN Announces Plans for 2025 Expansion
ValCUN, a Belgian original equipment manufacturer (OEM) of wire-based metal additive manufacturing (AM) hardware, has announced that the company has entered the next phase of its growth trajectory, making key...