Relying on Inkbit’s vision-controlled jetting (VCJ) technology, researchers from ETH Zurich, along with the Inkbit team, have 3D printed soft and hard structures in single job to create a robotic hand with bones, ligaments and tendons. The results of the work have been detailed in an article titled “Vision-controlled jetting for composite systems and robots,” published in Nature. However, the hand represents more than just a new development in soft robotics. It is also the culmination of several years of collaboration on Inkbit’s technology.
Typically, with photopolymer 3D printers, including traditional inkjetting, curing times are fast and lamps or galvos illuminate a part quickly after depositing, while layers are detached or parts scrape over screens or layers to tidy them up. With slow-curing materials this approach doesn’t work, limiting most photopolymer printing techniques to acrylate-based materials. However, to compensate for irregularities in the deposited materials, VCJ relies on a 3D laser scanning system to feed back information to the jetting process. In turn, the process is able to print slowly curing polymers such as thio-lenes and continuously curing polymers like cured epoxies.
“A feedback mechanism compensates for these irregularities when printing the next layer by calculating any necessary adjustments to the amount of material to be printed in real time and with pinpoint accuracy,” explained Wojciech Matusik, a professor at the Massachusetts Institute of Technology (MIT) in the US and co-author of the study.
The lab of ETH Zurich robotics professor Robert Katzschmann was instrumental in pushing Inkbit’s technology to achieve the capabilities needed for the project. Katzschmann told 3DPrint.com:
“At a high level, just the idea of operating a printer on vision-based feedback control at the voxel level is not new (e.g., MultiFab in 2015). What turned out to be extremely difficult was how to make this technology work at scale and with multiple materials. Inkbit and my lab’s team at ETH Zurich closely collaborated on this technological refinement and what can be made with the technology starting in 2020. While the printer hardware creation happened at Inkbit and the print design and iterations at ETH Zurich, it is not possible to easily dissect who did exactly what in this collaboration since we optimized the print technology together in a team through daily interactions. Our many test prints stress-tested the system and helped the team to find the right vision and print parameters and material formulations to make functional prints work. Before the collaboration, Inkbit was using a completely different scanning method based on Optical Coherence Tomography. That was a dead end that turned out to be too slow; about the time when my team joined the collaboration in 2020, a complete redesign and rebuild of the scanning system happened.”
To demonstrate the possibilities of VCJ, the team was able to print robotic hands with bones, ligaments and tendons made of different polymers in a single job for the first time. The researchers also explored the production of structures such as finger-like parts, pumps, pneumatics, tendons, metamaterials, and other elements crucial to soft robotics.
“We wouldn’t have been able to make this hand with the fast-curing polyacrylates we’ve been using in 3D printing so far,” explains Thomas Buchner, a doctoral student in the Katzschmann’s group and first author of the study. “We’re now using slow-curing thiolene polymers. These have very good elastic properties and return to their original state much faster after bending than polyacrylates.”
Implementing the VCJ compensation approach in certified production processes poses challenges, particularly in maintaining continuous strength and properties in a system where layers are unevenly propagated. Despite these challenges, VCJ enables the creation of highly complex parts with diverse functionalities.
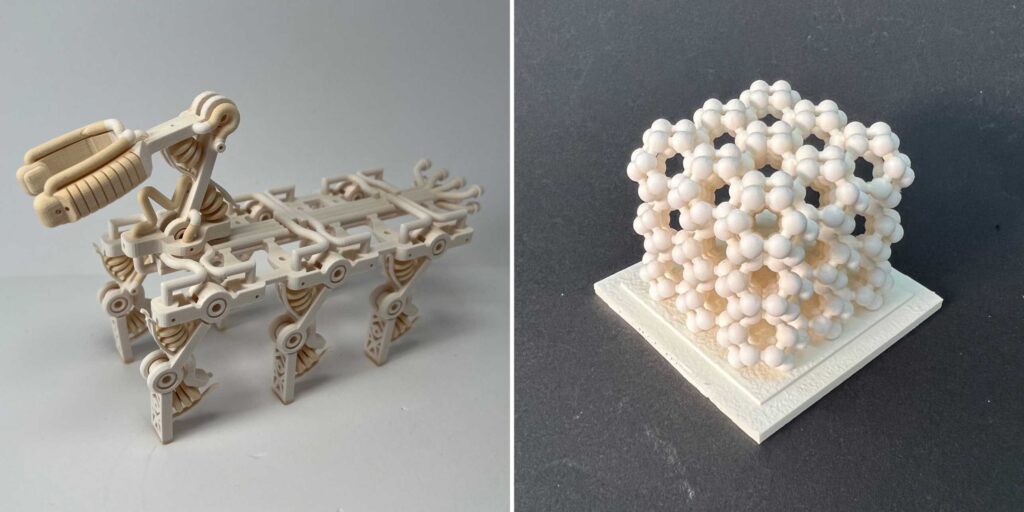
“We wouldn’t have been able to make this hand with the fast-curing polyacrylates we’ve been using in 3D printing so far. We’re now using slow-curing thiolene polymers. These have very good elastic properties and return to their original state much faster after bending than polyacrylates,” said Buchner. “Robots made of soft materials, such as the hand we developed, have advantages over conventional robots made of metal. Because they’re soft, there is less risk of injury when they work with humans, and they are better suited to handling fragile goods,” Katzschmann said in an ETH article.
The concept of soft robots as endearing, harmless entities that pose no threat is appealing. Such robots, built on a fundamentally different technological foundation, could operate in novel ways without relying on costly and environmentally damaging materials like metals, circuits, and batteries. For instance, consider a soft robotic device resembling a small balloon. It would utilize the residual heat from your floor to expand, then deflate overnight, rolling around to collect dust. This approach eliminates the need for cameras, charging, batteries, apps, software, electronics, or metal, relying instead on a chemical system with flexible materials to clean your floor innovatively.
Soft robotics has long been an intriguing concept in search of practical applications. One challenge has been the assembly process, which often resembles kindergarten arts and crafts, involving glue and scissors. Inkbit’s ability to simplify the creation of experimental soft robotic devices could open up a small yet promising market segment.
“The Nature paper shows how everything comes together: for the first time we have now the combination of a fast and reliable scanning system, as well as multiple materials formulations with mechanical properties compelling enough so that, taken together, represent a qualitative change with respect to what was possible before. We believe this opens the door to a whole new way of manufacturing. The materials used in the paper are really the beginning of a journey. We plan to introduce other chemistries with even better properties,” Katzschmann told us.
Subscribe to Our Email Newsletter
Stay up-to-date on all the latest news from the 3D printing industry and receive information and offers from third party vendors.
Print Services
Upload your 3D Models and get them printed quickly and efficiently.
You May Also Like
Reinventing Reindustrialization: Why NAVWAR Project Manager Spencer Koroly Invented a Made-in-America 3D Printer
It has become virtually impossible to regularly follow additive manufacturing (AM) industry news and not stumble across the term “defense industrial base” (DIB), a concept encompassing all the many diverse...
Inside The Barnes Global Advisors’ Vision for a Stronger AM Ecosystem
As additive manufacturing (AM) continues to revolutionize the industrial landscape, Pittsburgh-based consultancy The Barnes Global Advisors (TBGA) is helping shape what that future looks like. As the largest independent AM...
Ruggedized: How USMC Innovation Officer Matt Pine Navigates 3D Printing in the Military
Disclaimer: Matt Pine’s views are not the views of the Department of Defense nor the U.S. Marine Corps Throughout this decade thus far, the military’s adoption of additive manufacturing (AM)...
U.S. Congress Calls Out 3D Printing in Proposal for Commercial Reserve Manufacturing Network
Last week, the U.S. House of Representatives’ Appropriations Committee moved the FY 2026 defense bill forward to the House floor. Included in the legislation is a $131 million proposal for...