We’re starting off 3D Printing News Briefs with research about vat photopolymerization for high viscosity resin, and then 3D printed smart mesh gloves. Robotics and 3D printing in architectural ceramics were recently on display, and researchers developed a recyclable material to replace concrete formwork. XEV is offering owners of its YOYO EV the chance to customize their car with 3D printing. Finally, a maker created a desktop 3D printed ion thruster.
Linear Scan-Based VPP for Ultra-High Viscosity Resin
Vat photopolymerization (VPP) is often used in 3D printing due to its large build envelope, high efficiency, and versatile material options, but high fluidity of UV curable resin is needed due to the technique’s bottom-up printing mechanism. This material viscosity requirement is limiting: UV-curable resin often has to be diluted before usage, and adding reactive diluent sacrifices the oligomers’ mechanical properties. So the difficulties of 3D printing high-viscosity resins is leveling the material, and deformation of the cured parts from the film. A team of researchers from the Chinese Academy of Sciences (CAS), led by Professor Wu Lixin from the Fujian Institute of Research on the Structure of Matter, published a study on the use of linear scan-based vat photopolymerization (LSVP) for 3D printing ultra-high viscosity resin. Their system could build a better, more efficient platform for preparing 3D printed materials with diversiform properties, as oligomers could be used to prepare 3D printable UV-curable resins without using reactive diluents.
“In this work, an elaborated designed linear scan-based vat photopolymerization system is developed, allowing the adoption of printable UV-curable resins with high viscosity (> 600,000 cps). Briefly, this is realized by the employment of four rollers to create an isolated printing area on the resin tank, which enables the simultaneous curing of the resin and the detachment of cured part from the resin tank. To verify the applicability of this strategy, oligomer dominated UV-curable resin with great mechanical properties, but high viscosity is prepared and applied to the developed system. It is inspiring to find that high stress and strain elastomers and toughened materials could be facilely obtained,” the team wrote in their abstract.
Postgrad Researchers 3D Printing Smart Gloves for AR, VR, & Robots
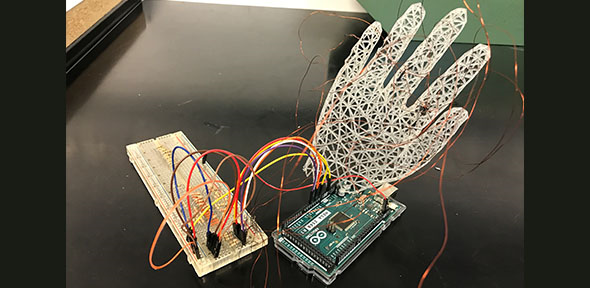
3D printed mesh glove, paired with 3D printed conductive strain gauges, connected to a circuit to enable real-time measurement of resistance changes as the fingers of the glove bend. Credit: Charlotte Hester.
Two University of Cambridge postgrad students are investigating the use of 3D printed wearable smart gloves in human-robot collaboration for augmented reality (AR) and virtual reality (VR) applications. Their flexible conductive mesh is piezoresistive, meaning its conductivity changes in response to applied strain. So measuring resistance between nodes of the lightweight lattice-like mesh of the gloves allows them to infer deformations, i.e. conform to any desired shape. Their research is at the early proof of concept stage, and the goal is for the 3D printed self-sensing mesh gloves to be used to reconstruct gestures and track 3D shapes, applicable to sign language, AR, VR, and other applications. Researchers Ivan Grega and Sara AlMahri received a 2023 CAPE Acorn Postgraduate Research Award (CAPA) for their work, and they will now develop an algorithm for the 3D reconstruction of the mesh’s deformation.
“The applications of such a system are numerous. For example, tracking the shape of a hand or other part of the human body can enable anthropomorphic robotic systems to learn motions. The tracking system, for instance, could provide feedback to a robot’s human operator as the robot tries to learn a motoric skill e.g. a tennis swing. The 3D representation of posture can also be used for real-time control of remote agents (e.g. remote surgery) or used in the digital domain (VR or AR),” said AlMahri.
Robotics & 3D Printing in Architectural Ceramics Displayed in Exhibition
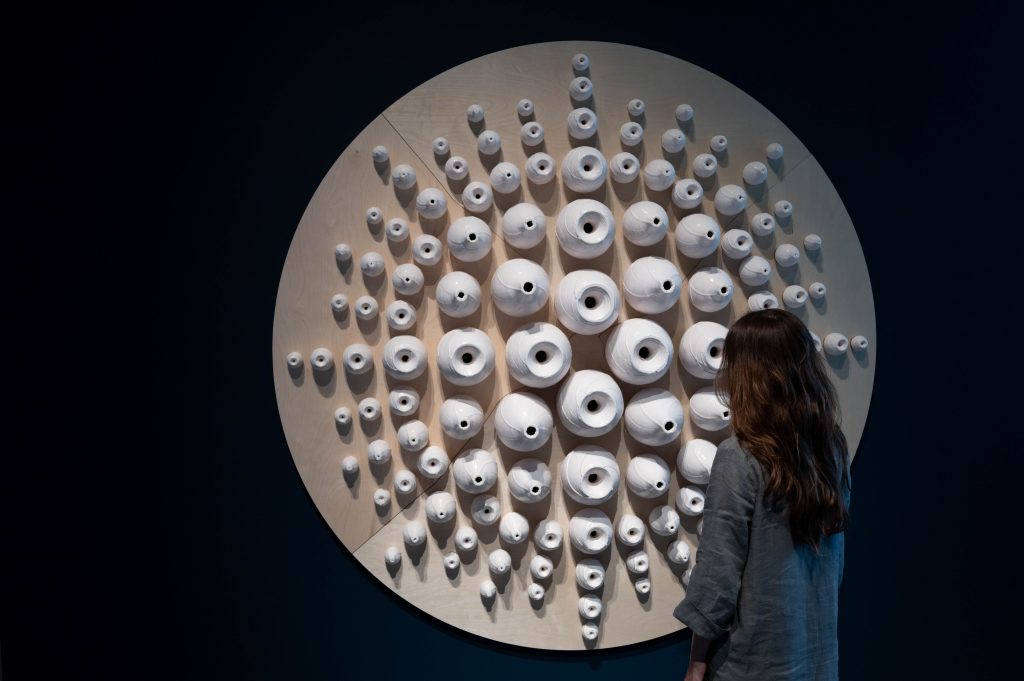
Acoustic Resonator Vases: Inverted neck design prototypes. Glazed stoneware, plywood. An inverted neck design for a compact Helmholtz resonator concept. (Nicholas Hoban, John Nguyen, Brady Peters, Ross Cocks, Nermine Hassanin, Elham Khatei, Yuuko Kosame Li-Han, Pablo Espinal Henao, Robin Yu Bin He, Paul Kozak, Rahul Sehijpaul, Liam Cassano. Daniels Robotic Prototyping Lab, John H. Daniels Faculty of Architecture, Landscape, and Design, University of Toronto)
A recent exhibition at the Canadian Clay and Glass Gallery in Waterloo, Ontario, titled Robotic Clay: New Methods in Architectural Ceramics, looked at the role of 3D printing and robotics in architectural ceramics, and invited academic institutions from all around North America to present the ceramic pieces they created using robotic techniques. These digital fabrication methods included CNC milling multipart molds used in manual pressing, clay 3D printing, waterjet carving moist clay slabs, and more. In combining these methods with traditional ceramic crafting to create walls and functional components, the exhibition showcased the potential of forging new form and spatial languages with the merging of the material’s characteristics and the emerging technologies.
Robotic Clay: New Methods in Architectural Ceramics was curated by David Correa, James Clarke-Hicks, and Isabel Ochoa with the University of Waterloo, and Denis Longchamps and Peter Flannery from the gallery. Participants in the exhibition came from the University of Waterloo, Laurentian University, Carleton University, the University of Toronto, the University at Buffalo, Dalhousie University, the University of Calgary, and more.
Reusable Robotic 3D Printed Formwork from Sawdust
Researchers with the University of Michigan‘s BioMatters team want to replace wasteful concrete formwork, and have developed a nearly zero-waste solution for the construction industry. The base of their biodegradable and reusable material is upcycled sawdust—a resource that’s available in abundance, as millions of tons of sawdust waste is created each year from 15 billion cut trees. In the concrete industry, formwork accounts for about 40% of construction expenses, so upcycling an unused byproduct of the wood industry could be a big step towards more efficient and environmentally friendly concrete construction methods. The team’s novel method creates nearly zero-waste freeform concrete structures by combining robotic 3D printing of the sawdust with incremental set-on-demand concrete casting. During casting, the 3D printed wood formwork shapes the concrete, which in turn stabilizes the wood against deformation. Once the concrete is cured, the formwork is removed, and then completely recycled by grinding and rehydrating the upcycled material with water.
“We have made a recyclable, all natural biomaterial which is made out of sawdust. Other sawdust-based solutions are using other petroleum-based polymers—we use biopolymers which are completely decomposable. And the biggest thing is it’s very easy to recycle and reuse,” explained Muhammad Dayyem Khan, a researcher at the university’s Digital Architecture Research & Technology (DART) Laboratory.
“When the sawdust decomposes, it is producing fatty acids, lignin, which causes toxicity in water. And once it starts contaminating water, it has its effects on smaller wildlife, microbes and a broad range of organisms. And with sawdust being extremely flammable, its potential contribution to wildfires is very high.”
XEV Offers 3D Printing Customization Service for YOYO Model
Urban mobility company XEV has used 3D printing from its start in 2018, and recently launched its new YOYO model, with deliveries set to begin in the fourth quarter of 2023. The upgraded electric vehicle (EV) will also feature Xpression, a 3D printing customization service that customers can use to personalize the exterior of their car. Specifically, the user can easily replace the YOYO blade, which is the plastic component on the door, so it matches their preference. The Xpression service uses high-precision 3D printing to offer a total of 42 different customizable YOYO blade options from which to choose. Through a collaboration with New York-based emerging online art platform UAAD, artists continuously provide YOYO drivers with stylish and fun options to make their travel experience more enjoyable.
The YOYO mini EV features intelligent frameless windows, a fun geometric body design and minimalist style, panoramic anti-UV glass roof, three-dimensional LED lights that complement each other at the front and rear, and a pure electric range of 150 km, top speed of 80 km/h, and maximum 15 kW motor power. The compact car also has two modes—sport and standard—with EPS electric power steering and a minimal turning radius, which makes it easy to navigate busy city streets. It’s quick and easy to swap out the YOYO’s lightweight battery packs at a swapping station, and XEV has also partnered with European energy giant ENI to deploy and operate battery swapping networks across Europe, which enables drivers to enjoy more convenient urban travel. The starting price for the new YOYO is €16,990 (excluding subsidies).
3D Printed Battery-Powered Desktop Ion Thruster
Finally, a maker who goes by Integza designed a 3D printed ion thruster, but probably not the kind you’re thinking of, which help send high-altitude aircraft and spacecraft to the sky. These engines operate by pulling electrons from a neutral gas supply and creating a cloud of positive ions, which are then accelerated by electromagnetic or electrostatic forces to provide very strong propulsion. Integza’s battery-powered version was designed for desktop use, and the compact solid-state ion thruster generates what Hackster’s Gareth Halfacree called a “pleasing discharge,” along with a gust of air that can blow out your birthday candles 16 inches away! It was built out of 3D printed parts, including a resin ring that was plated in copper for reduced weight. The design delivers enough usable thrust that it worked as an engine for a simple boat, but it got too heavy when potted high-voltage transformers were added to increase its output.
“Ionic wind is created when you shoot electrons from one place to the other. The electrons collide with the air molecules [which] are projected in [a given] direction,” Integza explained about the concept. “Stack a bunch of wires in tubes [and] you can actually get a pretty decent fan — but all of this kept me thinking, ‘what if I try to turn this bladeless fan [design] into an ionic thruster?'”
The 3D printing files for the desktop ion thruster are available on Printables under a permissive public domain license.
Subscribe to Our Email Newsletter
Stay up-to-date on all the latest news from the 3D printing industry and receive information and offers from third party vendors.
Print Services
Upload your 3D Models and get them printed quickly and efficiently.
You May Also Like
Reinventing Reindustrialization: Why NAVWAR Project Manager Spencer Koroly Invented a Made-in-America 3D Printer
It has become virtually impossible to regularly follow additive manufacturing (AM) industry news and not stumble across the term “defense industrial base” (DIB), a concept encompassing all the many diverse...
Inside The Barnes Global Advisors’ Vision for a Stronger AM Ecosystem
As additive manufacturing (AM) continues to revolutionize the industrial landscape, Pittsburgh-based consultancy The Barnes Global Advisors (TBGA) is helping shape what that future looks like. As the largest independent AM...
Ruggedized: How USMC Innovation Officer Matt Pine Navigates 3D Printing in the Military
Disclaimer: Matt Pine’s views are not the views of the Department of Defense nor the U.S. Marine Corps Throughout this decade thus far, the military’s adoption of additive manufacturing (AM)...
U.S. Congress Calls Out 3D Printing in Proposal for Commercial Reserve Manufacturing Network
Last week, the U.S. House of Representatives’ Appropriations Committee moved the FY 2026 defense bill forward to the House floor. Included in the legislation is a $131 million proposal for...