Two ambitious undergraduate students from the University of Colorado (CU) Boulder Aerospace Engineering Sciences program, Zachary Lesan and Patrick Watson teamed up with industry behemoths, ranging from Velo3D to CFturbo and SpaceX, to engineer an economical and dependable rocket turbopump. Named after a South Carolina hot pepper, the Reaper turbopump was designed to power a 6,000-pound thrust Reaper engine and is the first gas-generator cycle turbopump for flight, designed and built by university-level engineers, in partnership with the Sounding Rocket Lab and printed on Velo3D’s fully integrated metal AM solution.
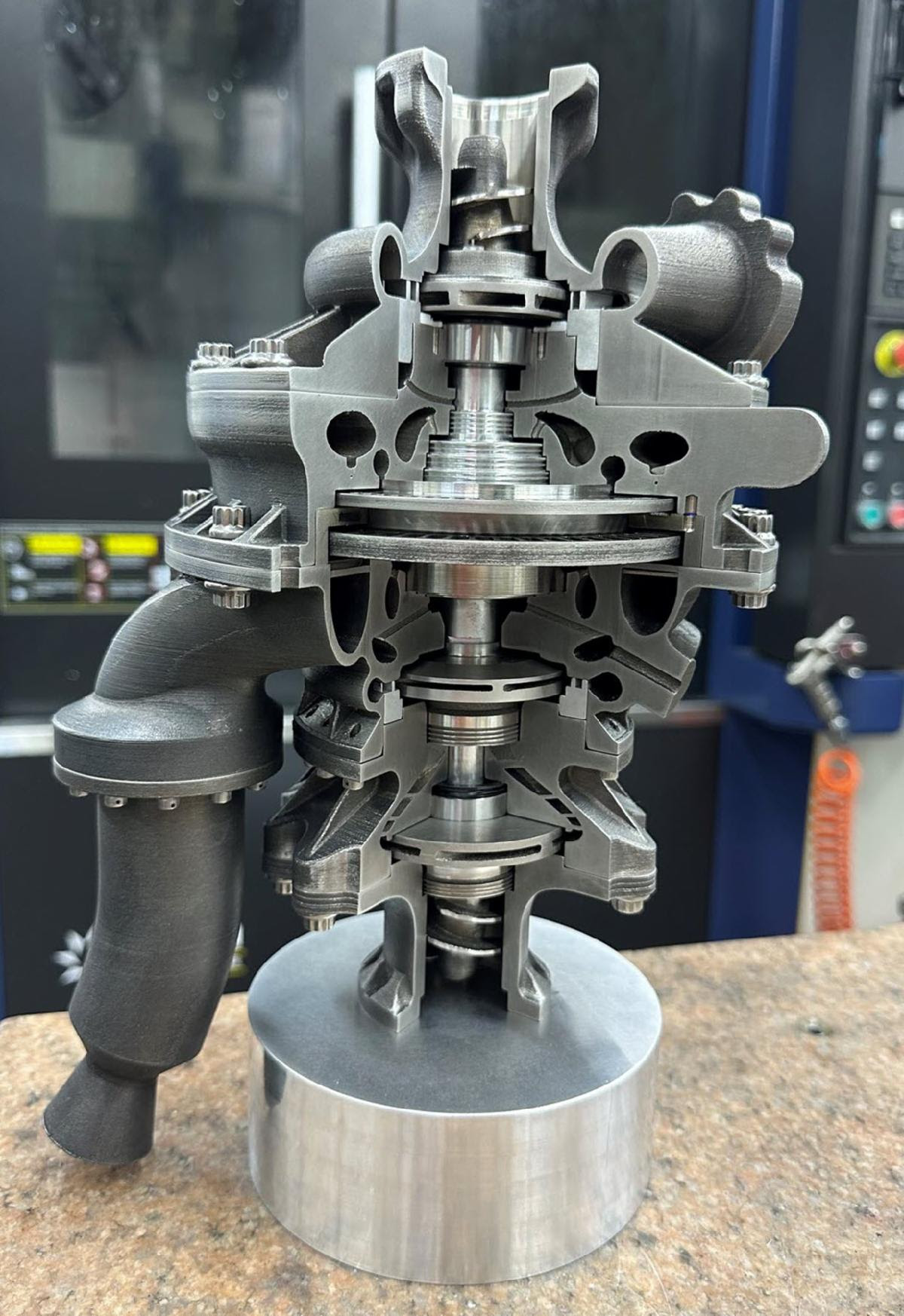
A cutaway view of a metal 3D printed rocket turbopump called the Reaper. Image courtesy of Parker Group.
A crucial component in modern liquid rocket engines, the turbopump supplies propellants to the combustion chamber at high pressures. Traditional turbopumps include several parts manufactured separately and assembled, leading to many possible weak spots. With metal additive manufacturing (AM), Lesan and Watson explored the possibility of printing significant portions of the turbopump as one unified piece. This approach reduces failure points and enables the creation of intricate designs unachievable with conventional methods.
In their project, 3D printing played a vital role in conceptualizing and realizing their turbopump. Metal AM allowed them to integrate multiple components and incorporate complex internal channels, optimizing fluid flow and performance. For example, cooling channels, critical in rocket components due to the extreme temperatures, could be intricately designed with 3D printing for more efficient cooling.
Furthermore, by using 3D printing, rapid prototyping became possible. They could swiftly move from a design to a physical model, test it, and then iterate it based on the results. This agility is key in aerospace projects where design adjustments are routine, and the goal is optimal performance.
Partnering with Velo3D and other industry leaders, the duo harnessed advanced laser powder bed fusion (LPBF) capabilities, producing lightweight and durable parts. Their work highlights the transformative potential of metal AM in the future of aerospace design and construction.
“I started this project because I loved rockets and turbomachinery,” said Lesan. “I knew how solid-state rocket motors worked and designed them in the past while in high school. However, liquid-propulsion rockets captured my imagination. I wanted very much to understand all the details.”
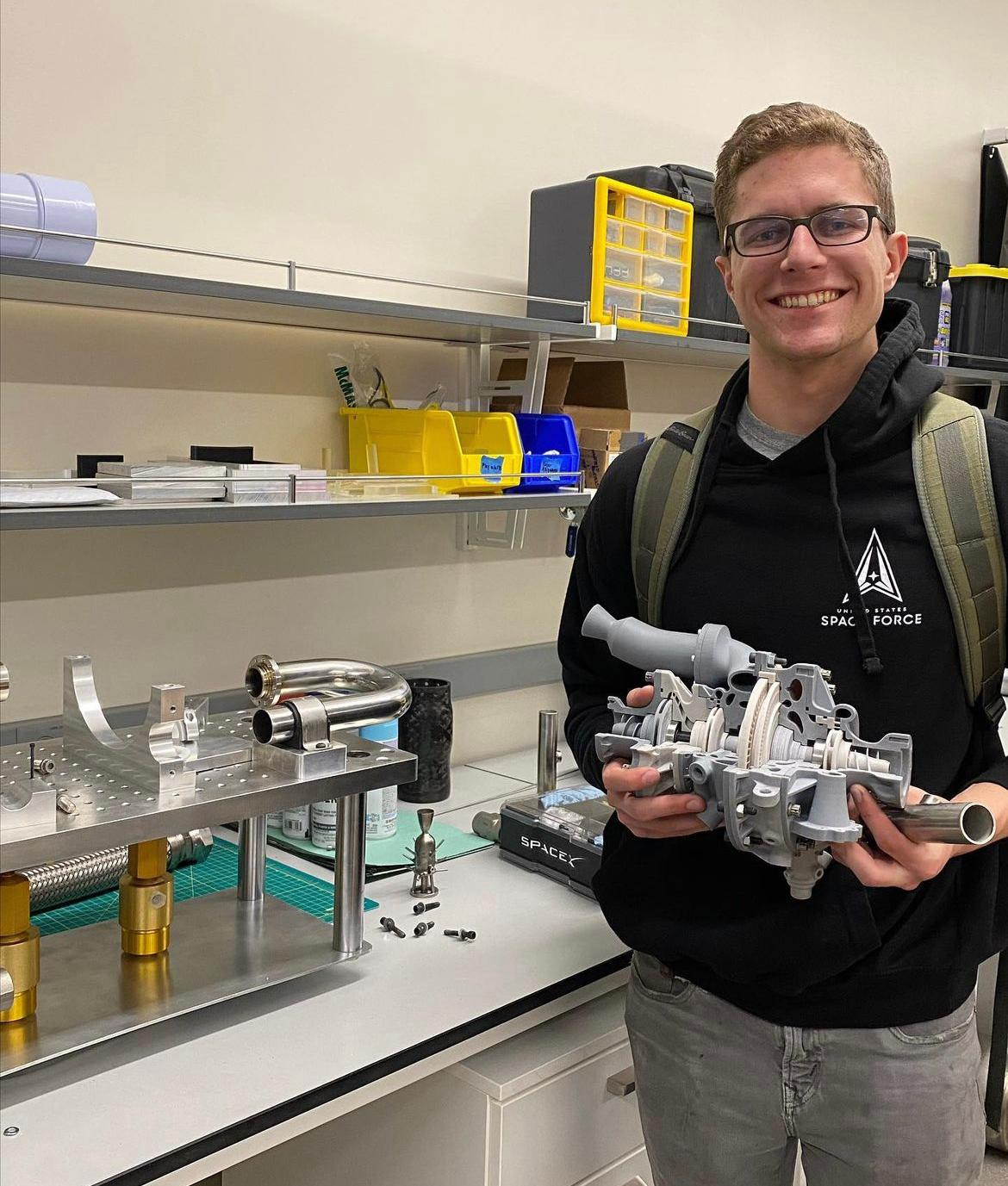
Zachary Lesan, CU Boulder Aerospace Engineering Sciences student designer, 3D printed a rocket turbopump called the Reaper. Image courtesy of Parker Group.
Starting point
It was Lesan’s passion for rockets that ignited this endeavor. Unhappy with his understanding of solid-state rocket motors from his high school days, liquid-propulsion rockets caught his attention during his junior year at CU. Although he didn’t find many other students doing the same thing, he threw himself into this challenging project, focusing on component design, CAD, 3D printing design principles, and software modeling.
Lesan conceived the project in January 2021 while in his junior year of undergraduate schooling. As the project picked up speed, Watson joined and took over most of the duties in the fall of 2022 once Lesan graduated and began an internship at SpaceX. Together, they chose to streamline the turbopump design, focusing on single-part construction, tapping into the potential of metal AM.
“A lot of companies cast their parts,” said Watson. “The real big breakthrough in turbomachinery for space or energy is 3D metal printing, LBPF mostly. We can now print the performance geometries we want, iterate the designs, get the surfaces we need, and use machining more selectively. Metal 3D printing makes our project possible. Zach and I used our intern salaries to fund what wasn’t donated or discounted. Imagine us spending tens of thousands of dollars on machining traditional parts or removing support structures.”
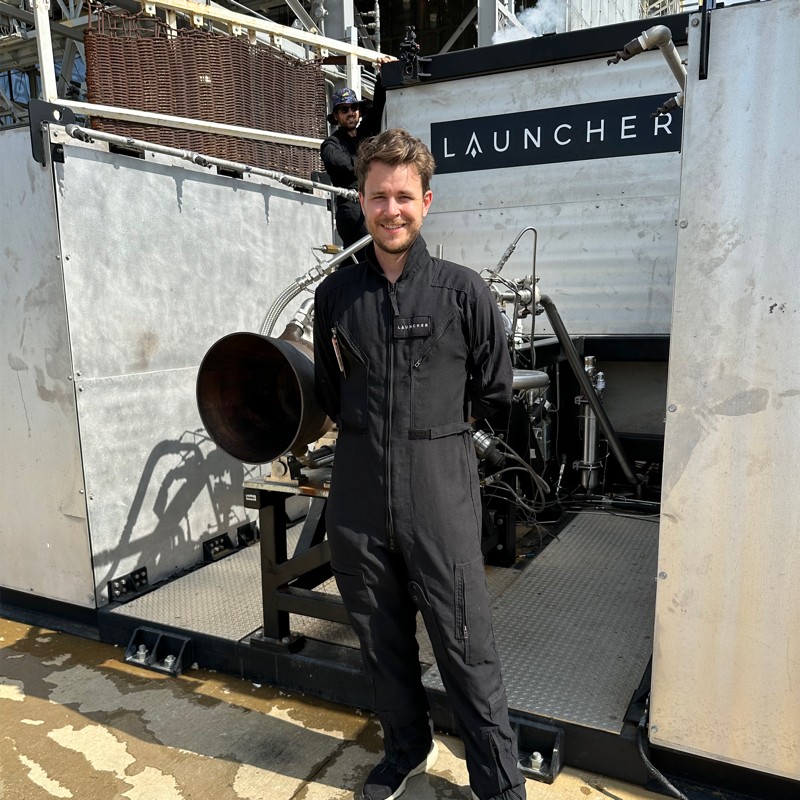
Patrick Watson, CU Bolder Aerospace Engineering Sciences student designer, 3D printed a rocket turbopump called the Reaper. Image courtesy of Parker Group.
Game changer
While Zachary and Patrick’s endeavor is groundbreaking, they are not alone in recognizing the potential of 3D printing in rocketry. In the aerospace sector, several pioneering companies are already leveraging the technology for rocket production. Colorado-based Ursa Major stands out with its rocket engines, which are more than 80% 3D printed by mass. Meanwhile, Rocket Lab‘s Electron rocket employs a Rutherford engine that’s predominantly 3D printed. SpaceX, led by Elon Musk, incorporates 3D printed components in the SuperDraco engines necessary for the Crew Dragon’s launch escape system.
Similarly, Launcher (now part of Vast) has already demonstrated the whole thrust of its fully 3D printed E-2 engine, bolsters a uniquely liquid oxygen-cooled chamber, and 3D printed in copper alloy in a single piece. However, the ambitious vision of 3D printing an entire rocket as a single piece remains a challenge yet to be fully realized.
The aerospace sector’s shift towards metal AM promises more than just improved designs. The goal is to combine as many parts as possible into a single construction, ensuring material integrity, optimizing weight and performance, and speeding up manufacturing. Such an approach is revolutionary and economically viable, which is especially critical in an industry where costs often skyrocket.
Lesan’s early interest in rockets provided a solid foundation. The challenge was to innovate – not necessarily to improve turbopump performance, but to leverage metal AM to enhance reliability and cost-effectiveness. The duo significantly reduced potential failure modes by eliminating the need for component sealing interfaces, traditionally a failure point, and reducing part count. Although some parts still required conventional manufacturing or purchasing, the emphasis remained on creating a cost-effective and safe system.
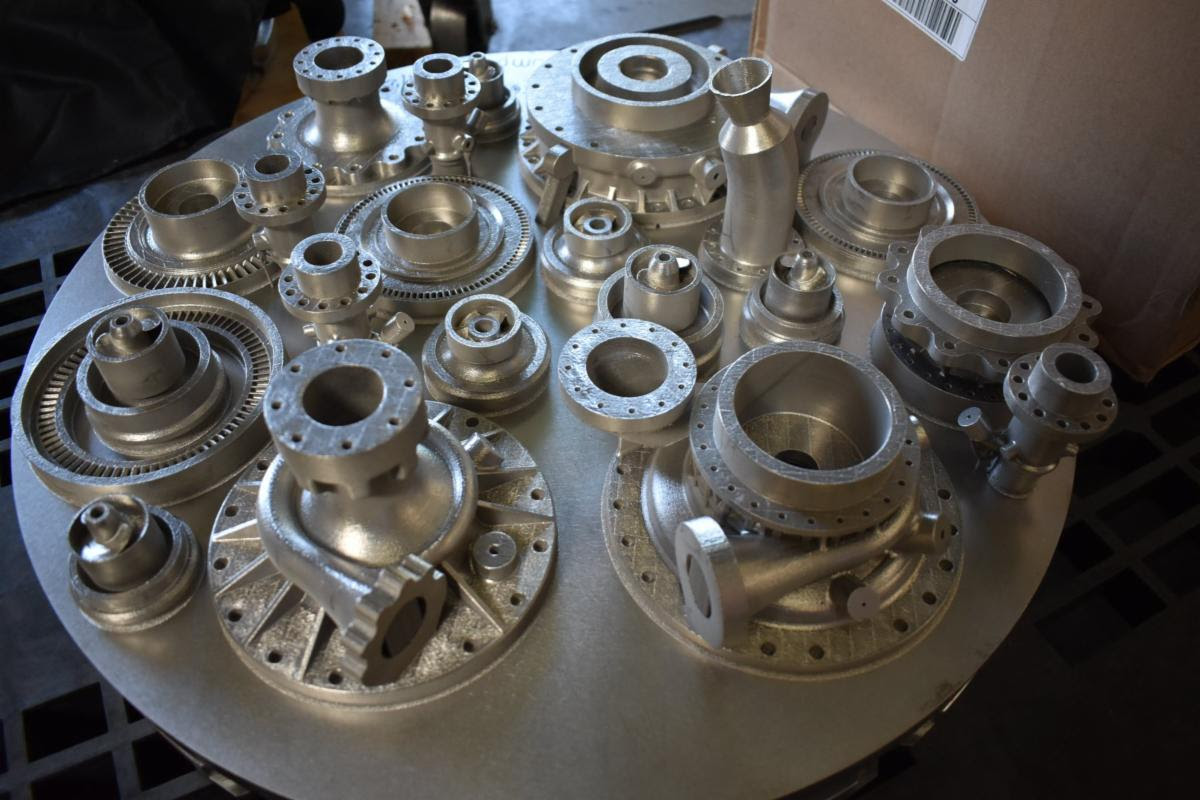
3D printed rocket turbopump called the Reaper had all its parts 3D printed on a single build plate. Image courtesy of Parker Group.
Collaborative triumph
The journey wasn’t without its challenges. From coordinating with industry giants to sourcing 3D printing, machining, and essential components like seals and fasteners, Lesan and Watson faced a big challenge. However, their dedication and initiative stood out. Lesan and Watson’s fast track to rocket development was aided by many. Professor John Farnsworth, Cameron Micksch, and Paul Wingrove from the university’s machining lab were from the CU Bolder Aerospace program.
Private industry stepped in with software, services, parts and advice. Metal printing was done with Velo3D; the team used critical design software and ongoing help from CFturbo and machining services from Silicon Valley Elite Manufacturing and EMP. They also received seals from Gallagher Fluid Seals and instrumentation from Kulite and Omega. Advice from individual engineers at their internship companies, SpaceX and Launcher, Ursa Major, and Andrew Mitchell, formerly with Masten Space Systems, now Astrobotic.
Such extensive collaboration is emblematic of where the industry is heading. According to Sid Raje from Velo3D, the students’ extensive use of advanced AM for part consolidation, challenging geometries, and overhangs set a new standard, signaling a future where reduced post-processing costs and enhanced system reliability become the norm.
With his industry internship having concluded at SpaceX, Lesan heads into military service as a Space Force second lieutenant and Watson nears the end of his undergraduate journey with a promising position at Launcher. However, the legacy of their project stands tall. With several industry professionals keen on bringing the Reaper to fruition, the goal remains clear: a successful flight to the Karman line at 10,0 kilometers.
Subscribe to Our Email Newsletter
Stay up-to-date on all the latest news from the 3D printing industry and receive information and offers from third party vendors.
Print Services
Upload your 3D Models and get them printed quickly and efficiently.
You May Also Like
Havaianas Collaborates with Zellerfeld to Launch 3D Printed Flip-Flops
The shoe of the summer is undoubtedly the flip-flop. Easy on, easy off, your feet won’t get sweaty because there’s not much material, and they’re available in a veritable rainbow...
UCLA Researchers Develop 3D Printed Pen that May Help Detect Parkinson’s Disease
Diagnosing Parkinson’s disease is difficult. Often, early symptoms of the progressive neurological condition may be overlooked, or mistaken for signs of aging. Early diagnosis can help save lives and improve...
Printing Money Episode 30: Q1 2025 Public 3D Printing Earnings Review with Troy Jensen, Cantor Fitzgerald
Printing Money is back with Episode 30, and it’s that quarterly time, so we are happy and thankful to welcome back Troy Jensen (Managing Director, Cantor Fitzgerald) to review the...
Heating Up: 3D Systems’ Scott Green Discusses 3D Printing’s Potential in the Data Center Industry
The relentless rise of NVIDIA, the steadily increasing pledges of major private and public investments in national infrastructure projects around the world, and the general cultural obsession with AI have...