Since the explosion of high-temperature material extrusion 3D printers began taking place, polyaryletherketone (PAEK) has been the polymer family on everyone’s lips. This is thanks in large part to British advanced materials company, Victrex, a legacy maker of the durable, heat- and chemical-resistant plastic that began developing 3D printable varieties. (For the sake of this article, we will not distinguish between PAEK and the widely used sub-variety known as “PEEK,” but you can learn about those distinctions here.)
At the 2023 Additive Manufacturing Users Group (AMUG) Conference, we were able to catch up with Robert McKay, head of New Business Development at Victrex, to learn how the firm’s endeavor into additive manufacturing (AM) has evolved in a substantial portion of its business and the development of LMPAEK polymer for all manner of 3D printing processes and applications.
What Is LMPAEK Polymer?
McKay joined Victrex in 2014 to lead the team dedicated to emerging technologies, just as the field of AM became an area of interest for Victrex. Given the overall success of 3D printing for the division, the industry need for a PAEK based filament optimized for 3D printing was high on the list of the emerging technology team’s activities. The key to making PAEK work for PBF, and then material extrusion was reformulating it to have a lower melting temperature and speed of crystallization.
“Victrex LMPAEK polymer is really a modified PEEK polymer, with a slightly different construction that changes the crystallization behavior of the PEEK polymer in AM to make it perform better in these processes,” McKay explained. “So, most of the activities you see from us in additive manufacturing is based on this LMPAEK polymer technology.
The technology was derived from Victrex’s work in layered composites construction with automated tape layup and automated fiber replacement using VICTREX AE 250 UDT, also based on LMPAEK polymer, where the process temperature of PEEK is lowered by 40°C and composite structure manufacture is faster and more efficient without sacrificing the performance properties. In these composites processes, the conditions seen by the polymer are very different than in injection molding.
“In injection molding, you’ve got this high-pressure, high-temperature environment where you have a lot of stresses on the polymer and that makes it behave a certain way. In printing, as soon as it leaves that nozzle, it’s just flowing in open air after the melt leaves the nozzle. So, we needed a polymer that flows well in this very low shear open air environment, and that’s one of the benefits of LMPAEK polymer.
Though it can be processed at a lower melting temperature, LMPAEK polymer’s degradation temperature is like PEEK’s, so the material has a 40°C wider processing window providing more flexibility in print profile settings. It can be printed at lower temperature than PEEK or printed at the same temperatures to achieve even higher flow rates from the nozzle for strong and intricate parts. In addition, as a PEEK-based copolymer, the material still offers the same strength, temperature resistance, and nearly the same chemical resistance that a high-melt PEEK variety would.
McKay acknowledges that even with the benefits of LMPAEK polymer in printing, there are still users that forgo the benefits of LMPAEK polymers for traditional PEEK because it has already passed regulatory requirements. He explained that these printers still must use high chamber temperatures to slow crystallization and obtain strong parts. This would make most sense in medical applications, for instance, where injection molded PEEK is already approved for implants and devices. For this reason, Victrex’s affiliate Invibio is providing PEEK-OPTIMA LT1 PEEK filament to medical-specific PAEK 3D printers, printing the material at the higher end of its processing window.
Another medical example is a joint project with Bond3D in the Netherlands. Bond3D garnered enough interest from Victrex that the British firm backed the startup financially in order to develop the next generation of porous spinal cages using the technology. Bond3D differentiates its technology from FDM through the use of PEEK rods, which it fuses essentially uniformly in all directions in a high-temperature build chamber. This means isotropic part properties, even across the Z-axis, an obstacle for AM generally and FDM in particular.
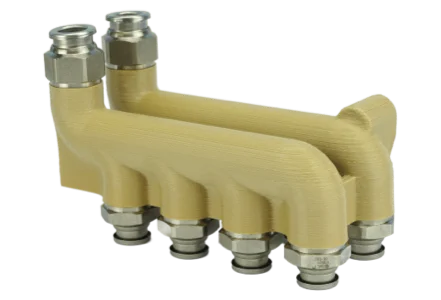
A cooling manifold that has been redesigned for 3D printing by Bond3D to reduce weight and optimize flow. Image courtesy of Bond3D.
VICTREX AM 450 PEEK filament is also available for industrial applications on similar very high chamber temperature machines. McKay point out that, in addition to medical implants, technologies such as Bond3D’s that enable printing with PEEK also have value with customers seeking to put printed PEEK parts in the most extreme environments. Although LMPAEK™ polymer is nearly identical to the high-melt variety, it does offer a somewhat lower level of chemical resistance in only the most extreme cases. So, for downhole applications in oil and gas, users tend to lean toward the variety, given the demanding environment. In those situations, very high temperature printers such as Bond3D are required to use PEEK for oil and gas in the most corrosive of environments. Example parts include oil pump casings, rings, and seals.
For everyone else, including aerospace application where LMPAEK polymer is already used in composite form, LMPAEK polymer can be printed at a lower melt and lower chamber temperature, easing printability, and lowering the stress on the machine.
VICTREX AM 200 Filament
In turn, Victrex has been able to open up a whole new world for what is one of the world’s highest-performing polymers. Most recently, this has been through the release of the VICTREX AM 200 filament from Victrex for fused deposition modeling (FDM). Several machine manufacturers are already supporting the material, including Intamsys, 3DGence, 3NTR, AON3D, and Zortrax. Stratasys has also announced upcoming support for VICTREX AM™ 200 on their 450MC printer as they add third party materials to their eco-system.
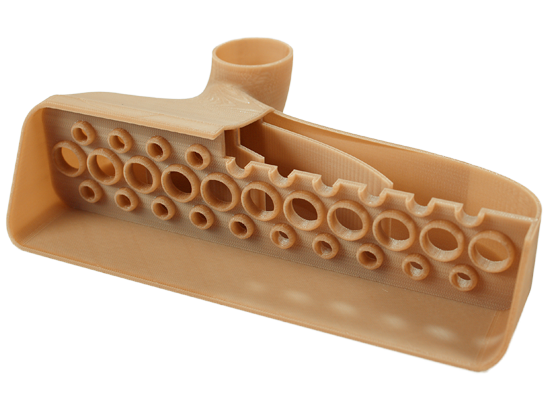
Complex aero ECS duct printed with FDM technology in Victrex AM 200 material. Image courtesy of Stratasys.
Three areas that previously would have difficulty using PEEK from the company are large-format AM, 3D printing with soluble supports, and printing strong crystalline parts in low chamber temperature machines. In the former case, it is impractical to heat large-format 3D printers up to the levels needed for high-melt varieties of PEEK. Whereas, in latter case, available soluble support material does not hold up under such an environment. Finally, the slower crystallizing VICTREX AM 200 filaments result in stronger interlayer adhesion when printed amorphous in colder chambers but hold their shape better in annealing to crystalline than amorphous varieties of PEKK. McKay explains VICTREX AM 200 material as “having the ease of printing of amorphous PEKK, with the part performance of crystalline varieties of PEKK and PEEK, and the design flexibility of using soluble supports common in lower performing polymers.”
With LMPAEK polymer, it’s possible for these areas to benefit from the power of PAEK. For large-format 3D printing, one can imagine large pipe seals for oil and gas or molds for composite aerospace parts that must undergo extreme processing temperatures. For soluble supports, this means actually being able to take full advantage of the geometric possibilities of AM, including complex, moving assemblies 3D printed in a single operation.
PAEK Adapts to the Environment
One question that may arise when discussing such a heavy-duty polymer as PAEK is the role it will play in an ecologically conscious and resource-constricted environment. As the world shifts to renewable energy, petroleum will have to be an increasingly smaller role in the chemical industry. This is particularly true as the limits of easily accessible oil supplies become more widely apparent.
McKay clarified that, just because PAEK is such a robust material does not mean that it must be made with petrochemicals.
“All of these polymers are made from carbon, oxygen, and hydrogen molecules. You can make those molecules from bioresources or oil. Oil is bioresources that have been fossilized. So, you can just skip the fossilization step and go directly to renewable bio-based resources, certainly. And that’s already happening. And as the industry builds that infrastructure out, we’ll benefit from that and people will be able to source those bio-based hydrocarbon resources and construct their own polymers, just as we do.”
In other words, PAEK is not going anywhere anytime soon. So, as AM becomes one of the go-to technologies for energy transition, the feedstocks the technology relies on will have to undergo their own transition, but they will still be largely available. And, if any company is likely going to be involved in that evolution, it will be Victrex.
Subscribe to Our Email Newsletter
Stay up-to-date on all the latest news from the 3D printing industry and receive information and offers from third party vendors.
Print Services
Upload your 3D Models and get them printed quickly and efficiently.
You May Also Like
U.S. Navy Lab Uses 3D Printing to Reduce Tooling Lead Time By Over 90%
The F-35 Lightning II Joint Program Office (JPO), responsible for life-cycle management of the key fifth-generation joint strike fighter (JSF) system used by the U.S., its allies, and its partners,...
Etsy Design Rule Change Reduces Selection of 3D Printed Goods
Online marketplace Etsy has implemented a rule change requiring all 3D printed goods on the site to be original designs. The update to the site’s Creativity Standards states, ¨Items produced using...
Honeywell Qualifies 6K Additive’s Nickel 718 for 3D Printed Aerospace & Defense Parts
6K Additive is renowned for manufacturing sustainable additive manufacturing (AM) powder, and offers a wide portfolio of premium metal and alloy powders that include titanium, copper, stainless steel, and nickel,...
MetalWorm Sells WAAM Systems to Research Institutes in Brazil and Malaysia
Turkish WAAM firm MetalWorm has sold a system in Malaysia and another in Brazil. This is an excellent example of a few emerging trends in additive. Firstly, WAAM was experimented...