EOS has officially announced the launch of its Smart Fusion software for in-process laser adjustment, eliminating the need for most support structures, minimizing material use, reducing post-processing requirements, and cutting cost-per-part (CPP) for metal 3D printing. According to the company, Smart Fusion achieves all of the above at a speed that is two to five times faster than competitors.
Since Velo3D came to market, metal laser powder bed fusion (LPBF) companies have been in a race to demonstrate that they can 3D print metal parts without support structures. On top of that LPBF has struggled with quality control and ensuring that parts can be printed properly in the first job. Due to the complex number of variables involved in the printing process, it usually takes upwards of seven prints to achieve the proper printing parameters, part orientation, and support structures for a successful print. Not only does this issue result in wasted materials, but it also increases overall costs.
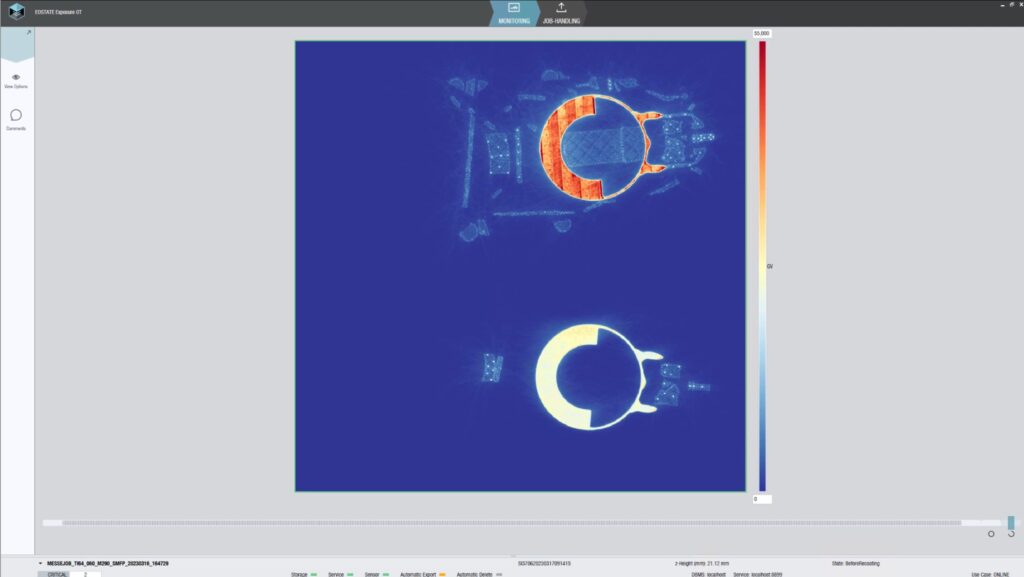
A part being 3D printed with and without supports.
Smart Fusion is the EOS solution to the problem. The technology was first previewed in our interview with members of EOS at the 2023 Additive Manufacturing Users Group Conference, but is now being demonstrated to the public at the upcoming RAPID+TCT May 2-4, 2023 in Chicago at the EOS Booth #4612. It operates by detecting build issues and adjusting laser powder automatically, enabling “first-time-right” printed parts and eliminating the standard trial and error technique.
As discussed in our interview, Smart Fusion achieves this without slowing down the printer or pre-warping parts, which are the two most often used solutions to the problem. The technology achieves this by measuring the amount of laser power absorbed by the powder bed combining EOS’s existing monitoring solutions with new algorithms. This includes use of EOSTATE’s Optical Tomography (OT) camera, which measures meltpool emissions and feeds the data back to the laser to adjust it automatically via EOSYSTEM. As a result, energy is distributed consistently across the entire bed. In turn, stress in the printed parts, as well as overheating and other anomalies, are avoided.
When speaking to 3DPrint.com at AMUG, Senior Additive Manufacturing Consultant for EOS Michael Wohlfart explained, “By avoiding overheating, you have eliminated one of the biggest factors for why you would need supports,” Wohlfart said. “So, we can dramatically reduce supports that you would just need to increase heat transfer in overhanging regions of the parts. Another reason for supports would be compensation for residual stress because of the welding process. We have also seen that, if we avoid overheating, the residual stress becomes lower. The best part is that it’s automated, so it doesn’t require a lot of adjustments by the user.”
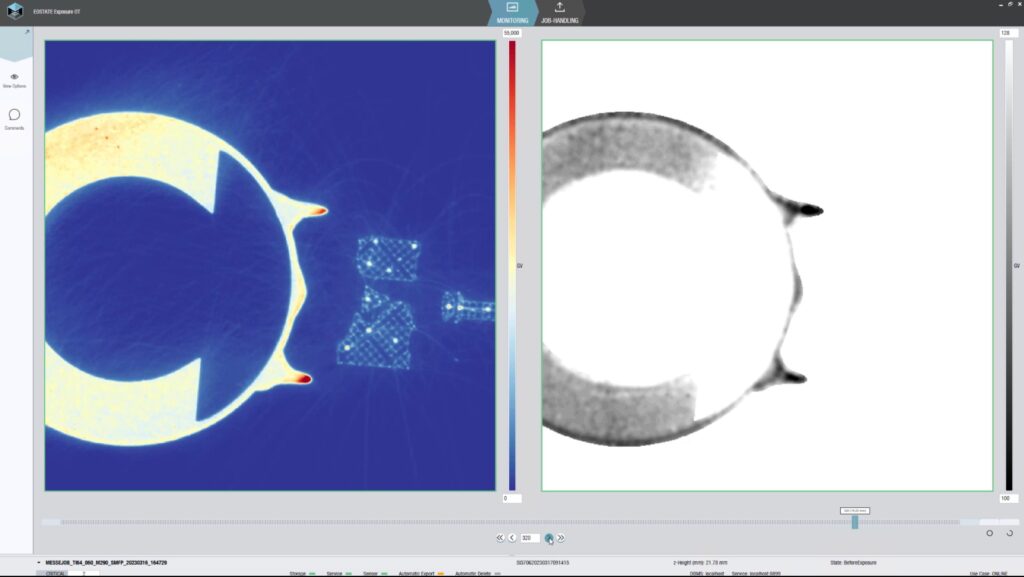
Image of a print captured with the OT camera as compared with its processing in Smart Fusion.
Beta customers have been able to print at two to five times the speed of leading competitors in the market. This, along with reduced support structures and waste from trial and error, improves overall CPP, which EOS highlights as a leading business driver for the technology. Stefan Seidel, Chief Technical Officer at motorsports and aerospace manufacturer Pankl Racing Systems, said of the tool:
“When we learned about Smart Fusion and started to test it several month ago, we knew it would be a game changer. Not only does it significantly reduce the part cost, but it is also a facilitator in the use of optical tomography which, in our view, is a key element to introduce AM for serial production. Over the past few months, we have developed several products with EOS which really show the potential of Smart Fusion. “
Available for €27,000/$29,262 for the EOS M 290 and €38,000/$41,184 for the EOS M 300-4 and EOS M 400-4, Smart Fusion requires the Smart Monitoring System. It is so far available or will be available for these systems for use with Inconel 718, Titanium Ti64, and AlSi10Mg aluminum alloy from EOS. The company also plans to release the technology for its AMCM subsidiary, which manufactures large-scale metal 3D printers.
“The beauty of Smart Fusion is that it is incredibly flexible, easy-to-use, and will work with the majority of customer applications out-of-the-box,” said Mirco Schöpf, EOS product line manager for software. “We challenged our team to mitigate one of metal AM’s significant challenges with a unique software solution and we could not be prouder of the results. “
To learn more about how Smart Fusion compares in the competitive landscape, read our recent interview with the EOS team. Also be sure to visit the EOS booth, #4612, at RAPID+TCT.
Subscribe to Our Email Newsletter
Stay up-to-date on all the latest news from the 3D printing industry and receive information and offers from third party vendors.
Print Services
Upload your 3D Models and get them printed quickly and efficiently.
You May Also Like
U.S. Navy Lab Uses 3D Printing to Reduce Tooling Lead Time By Over 90%
The F-35 Lightning II Joint Program Office (JPO), responsible for life-cycle management of the key fifth-generation joint strike fighter (JSF) system used by the U.S., its allies, and its partners,...
Etsy Design Rule Change Reduces Selection of 3D Printed Goods
Online marketplace Etsy has implemented a rule change requiring all 3D printed goods on the site to be original designs. The update to the site’s Creativity Standards states, ¨Items produced using...
Honeywell Qualifies 6K Additive’s Nickel 718 for 3D Printed Aerospace & Defense Parts
6K Additive is renowned for manufacturing sustainable additive manufacturing (AM) powder, and offers a wide portfolio of premium metal and alloy powders that include titanium, copper, stainless steel, and nickel,...
MetalWorm Sells WAAM Systems to Research Institutes in Brazil and Malaysia
Turkish WAAM firm MetalWorm has sold a system in Malaysia and another in Brazil. This is an excellent example of a few emerging trends in additive. Firstly, WAAM was experimented...