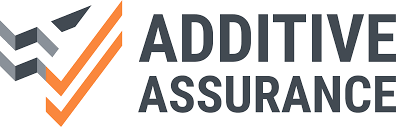
The future of laser-based metal additive manufacturing is looking brighter than ever. The last few years have seen a substantial increase in production rates due to the increase in laser count, improved gas flow, and improved control systems. With the drive towards serial production and resulting increased speed and throughput, the compromise is often component quality. This makes quality control the last and most critical unresolved issue for the additive manufacturing industry.
In situ monitoring offers an obvious solution to this problem. Melt pool monitoring is a particularly powerful tool that can ensure the quality and consistency of parts. By tracking the melt pool emission signatures, anomalies and faults can be detected. It is one of the few inspection technologies that can scale with production demand, making it an essential component of AM production at scale.

In-situ monitoring can take many forms; keeping an eye on various parameters of the AM process, such as temperature, powder distribution, and consolidation properties. This information, coupled with intelligent analytics, can identify issues before they result in defects in the final product. Identifying faults in the process can help to reduce the number of defective parts produced and increase the overall operating efficiency of the manufacturing process.
While in situ monitoring is an obvious solution to the quality assurance (QA) problem, what is non-obvious is the need to have a common form of QA across all production parts. Many machine vendors offer their proprietary monitoring solutions with varying capabilities depending on the approach and sensors used. Operators using L-PBF systems from different vendors will end up with non-compatible QA systems and with data that is not easily comparable. Curating non-comparable QA increases cost and in many cases is not acceptable for safety-critical parts.
Additive Assurance has built the AMiRIS quality assurance suite to solve exactly this; provide uniform real-time quality assurance across all machines. The unique sensor package captures melt pool emissions from an off-axis vantage point at a very high resolution in the near-infrared (NIR) spectra. By utilising NIR wavelengths, the sensor has the unique capability of identifying melt pool anomalies through the process chamber window, without the need to modify the machine. Crucially, no machine requalification is required after installation. The sensor package feeds the captured melt pool data to a central server (cloud or on-premise) where a ML model has been trained to detect a range of process faults, including: lack of fusion, overmelting, spatter frequency, laser errors and more.
Additive Assurance is working to enable the next generation of metal AM users, by reducing the entry barriers, making production quality simple, and reducing the workload on operators and quality managers. The AMiRIS cloud based platform has been, and continues to be, developed in collaboration with leading AM providers to do exactly this.

While process monitoring is a powerful tool for capturing faults and anomalies, it has previously been seen as a burden on operators to inspect and understand. Any effective QA system using in situ monitoring must have a high degree of automation in order for the technology to work at scale. Automation is a core philosophy behind the design of AMiRIS. Every part of the workflow has been automated, from initial calibration and detection of individual anomalies, to the final go/no-go part checks.
For additive manufacturing operators at scale, in situ monitoring across a fleet of machines can provide a common form of quality control, which helps to ensure consistent AM quality and reduce the chances of defects, regardless of the machine brand/vendor. When automated, in situ process monitoring enables the production of quality assured parts at scale.

In situ process monitoring is a powerful tool for solving the quality issues of AM, and has the flow on effects of reducing failures and increasing productivity. As the AM industry continues to evolve, in situ monitoring will become increasingly important for manufacturers at scale, providing a unified way to access, monitor and control the quality of the parts produced.
Additive Assurance is participating at Additive Manufacturing Strategies, taking place in New York City from February 7-9, 2023. Marten Jurg, CEO and Co-Founder of Additive Assurance, will be taking part in Session 3, Panel 1: AM in the Auto Industry on February 8. Register for your ticket to attend here.
Subscribe to Our Email Newsletter
Stay up-to-date on all the latest news from the 3D printing industry and receive information and offers from third party vendors.
Print Services
Upload your 3D Models and get them printed quickly and efficiently.
You May Also Like
Making 3D Printing Personal: How Faraz Faruqi Is Rethinking Digital Design at MIT CSAIL
What if your 3D printer could think more like an intelligent assistant, able to reason through a design idea, ask questions, and deliver something that works exactly the way the...
Reinventing Reindustrialization: Why NAVWAR Project Manager Spencer Koroly Invented a Made-in-America 3D Printer
It has become virtually impossible to regularly follow additive manufacturing (AM) industry news and not stumble across the term “defense industrial base” (DIB), a concept encompassing all the many diverse...
Heating Up: 3D Systems’ Scott Green Discusses 3D Printing’s Potential in the Data Center Industry
The relentless rise of NVIDIA, the steadily increasing pledges of major private and public investments in national infrastructure projects around the world, and the general cultural obsession with AI have...
Formlabs Teams Up with DMG MORI in Japan
In late June, Nick Graham, Chief Revenue Officer at Formlabs, announced on LinkedIn that the company had partnered with DMG MORI, one of the world’s leading machine tool companies, to...