How New Multi-material 3D Printing Can Transform the Dental Industry and Beyond – AMS Speaker Spotlight
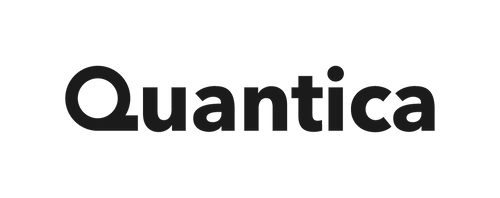
Until now, additive manufacturing techniques have mainly been used to produce existing products in smaller quantities or in personalized forms. Occasionally, an additive manufacturing process can generate additional benefits, such as the ability to create tool-free geometries, resulting in weight savings through biomimetic forms. However, most additive manufacturing processes are subject to a limitation: once multiple components or functional objects are involved, the individual components have to be manufactured separately and then assembled.
However, Quantica, our Berlin-based manufacturing company specialized in the design and development of advanced additive technology, is changing this. Quantica’s material jetting technology allows, for the first time, users to produce multi-component, functional objects in a single production step. This eliminates many production and assembly steps and enables nested geometries of different materials.
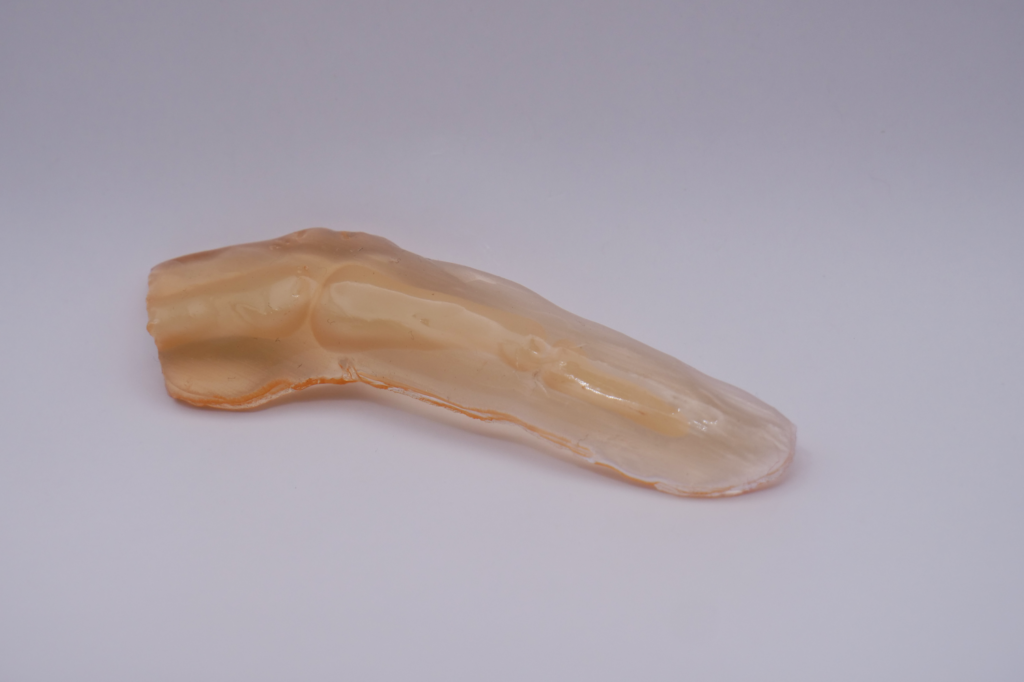
Multi-Material Finger Model, another print sample designed to showcase the ability to print two materials together.
This is an invention that I personally have been waiting and hoping for over the past 20 years, as I have conducted feasibility studies on the use of additive production methods in several industries. The result was often that the use of additive production methods did not offer any significant advantage beyond faster availability and customization. However, this has changed with the use of material jetting of high-viscosity, high-performance and functional materials. Now, products are possible where multiple materials are combined in a single printing process, and designs that could not be produced or assembled as tool-falling parts can be created. The dental industry is only the beginning, but a significant one. In this article I’ll use the dental space as an example to explore the value that multi-material can add to an industry.
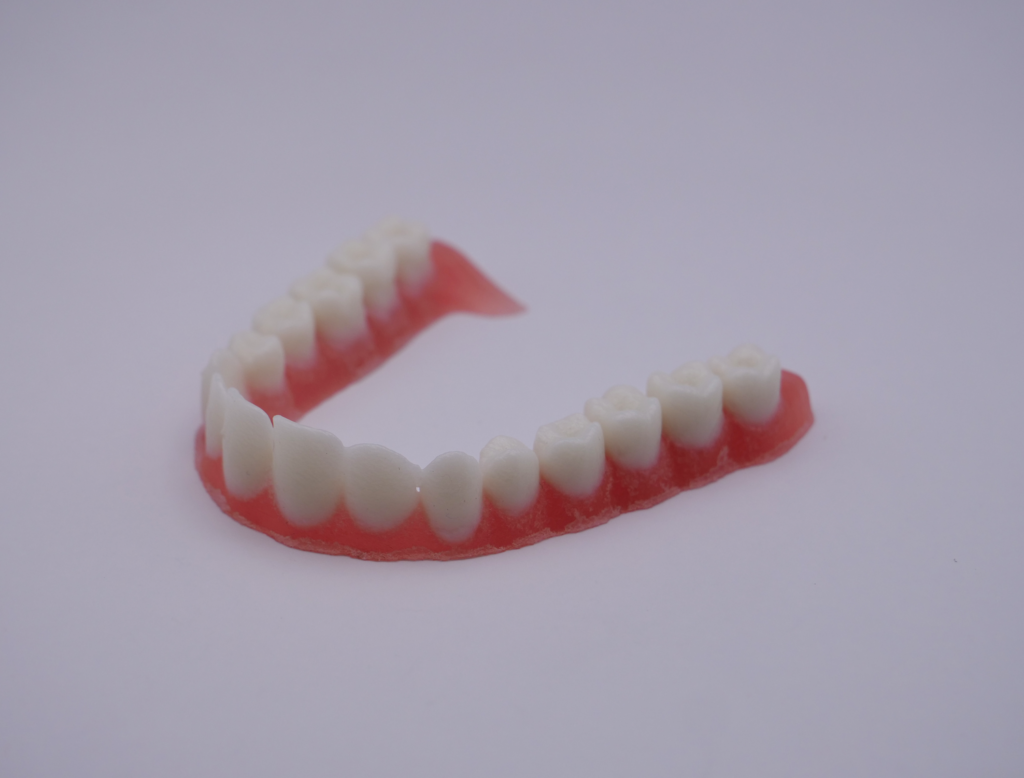
Multi-Material Denture Model, a print sample designed to showcase the ability to print two materials together.
Over the last three years, I have had the opportunity to speak with many professionals in various industries about the benefits of Quantica’s technology. When it comes to additive manufacturing, the dental industry has been an early adopter as they have both the knowledge and funds to innovate quickly, and I would add that they are the most developed industry using additive manufacturing to produce end-parts. During these years, I’ve been fortunate to have hundreds of conversations with those in the space, from large dental labs to individual dentists, and the items I mention come from these conversations.
The core value that multi-material 3D printing offers to the dental industry is enabling the creation of more esthetically pleasing and natural-feeling dentures. With the ability to use multiple colors to mimic the patient’s natural tooth color and multiple materials to simulate the properties of real teeth, such as a hard, wear-resistance, ductile, translucent enamel outer layer, 3D printed dentures can offer a close-to-natural appearance.
The production process can also be fully digitalized, with data driving the entire process from scanning to final product, reducing the need for human interaction to the preparation of data. Saving on labor costs and manual work needed in post-processing. This can greatly reduce the production time of dentures and other applications, going from days to just hours. Additionally, production can be facilitated at the dentist’s office rather than at a lab, allowing for customized solutions to be created in just one visit, eliminating the need for multiple visits and waiting times.
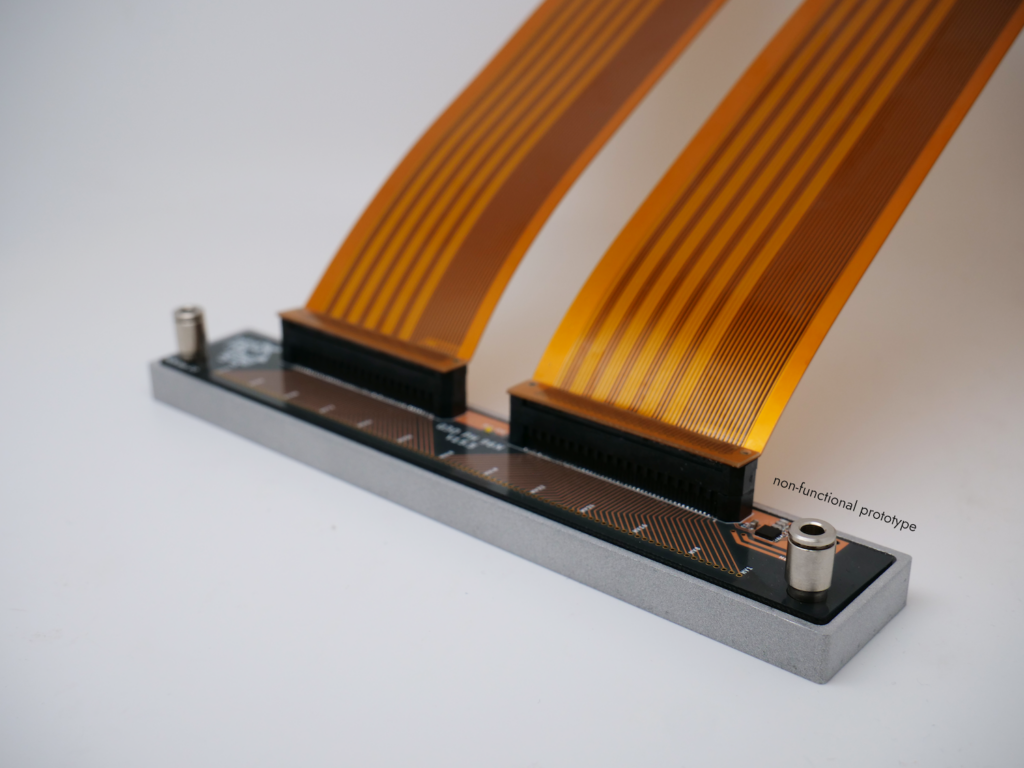
The NovoJet C-7 is the first design of the open research and development system that Quantica will release by the end of the year.
Overall, multi-material 3D printing has the potential to improve the dental industry by providing faster, more personalized solutions with a natural appearance in a fully digitalized workflow. Yet these benefits can also impact many other industries including:
- In healthcare, for producing custom multi-material medical and drug delivery devices.
- In electronics, it can be used to print electronic components with multiple materials such as conductive and insulating materials in one print job.
- In consumer goods, for offering more customization, comfort, and personalization.
The possibilities are endless and we are excited to see how our technology will be used to improve and transform various industries. Join me at AMS from February 7-8, 2023 where I’ll share more about dental trends within additive manufacturing.
Quantica is participating at Additive Manufacturing Strategies, taking place in New York City from February 7-9, 2023. Marcel Strobel, Chief Operating Officer at Quantica, will be taking part in Session 2, Panel 1: Dental Printer Trends on February 8. Register for your ticket to attend here.
Subscribe to Our Email Newsletter
Stay up-to-date on all the latest news from the 3D printing industry and receive information and offers from third party vendors.
Print Services
Upload your 3D Models and get them printed quickly and efficiently.
You May Also Like
Reinventing Reindustrialization: Why NAVWAR Project Manager Spencer Koroly Invented a Made-in-America 3D Printer
It has become virtually impossible to regularly follow additive manufacturing (AM) industry news and not stumble across the term “defense industrial base” (DIB), a concept encompassing all the many diverse...
Inside The Barnes Global Advisors’ Vision for a Stronger AM Ecosystem
As additive manufacturing (AM) continues to revolutionize the industrial landscape, Pittsburgh-based consultancy The Barnes Global Advisors (TBGA) is helping shape what that future looks like. As the largest independent AM...
Ruggedized: How USMC Innovation Officer Matt Pine Navigates 3D Printing in the Military
Disclaimer: Matt Pine’s views are not the views of the Department of Defense nor the U.S. Marine Corps Throughout this decade thus far, the military’s adoption of additive manufacturing (AM)...
U.S. Congress Calls Out 3D Printing in Proposal for Commercial Reserve Manufacturing Network
Last week, the U.S. House of Representatives’ Appropriations Committee moved the FY 2026 defense bill forward to the House floor. Included in the legislation is a $131 million proposal for...