Let’s get kids 3D printing! Kicking off 3D Printing News Briefs today, Anycubic and Yale Funbotics held virtual camps to introduce children to 3D modeling and 3D printing. Moving on to research, a team from the University of Virginia is using machine learning to detect a certain kind of 3D printing defect in real time. Finally, rms Company added yet another 3D Systems printer to its fleet, in order to scale medical device production.
Anycubic & Yale Funbotics Introducing Kids to 3D Printing at Camp
Popular 3D printer company Anycubic, founded in 2015, recently collaborated with non-profit organization Yale Funbotics to hold its first education incubation project, the Anycubic X Yale Funbotics 3D Modeling & Printing Camp, in order to introduce children to 3D printing and 3D modeling. The camps are designed for 4th to 12th-grade students, and all three sessions were held virtually over Zoom for three days, with the first day focused on learning to assemble the beginner-friendly Anycubic Kobra printer. On the second day, the students worked with mentors to learn how to model designs in CAD, and on the last day, they learned to slice, print, and troubleshoot their own models, like phone cases, pencils, and Harry Potter wands. Yale Funbotics was founded to provide underrepresented youth the technologies and opportunities to learn about STEM, and the project, founded in Shenzhen in 2020, showed the participating students much fun STEM can be.
“The Anycubic X Funbotics camps not only introduced and showed young students how much fun STEM is but gave them the opportunity and resources to pursue the field in the future. Funbotics plans to continue our partnership with Anycubic to promote STEM education in underrepresented communities. We are working on adding to the 3D modeling and printing curriculum to teach students how to print, assemble and program their own autonomous robots. We are also opening our Funbotics Lab Centers for students to come and work on their engineering projects. We are incredibly grateful to the Anycubic team – without your support, such a monumental impact would not have been possible,” said Pranav Avasarala, the Founder of Yale Funbotics.
UVA Researchers Detecting LPBF 3D Printing Defects in Real-Time
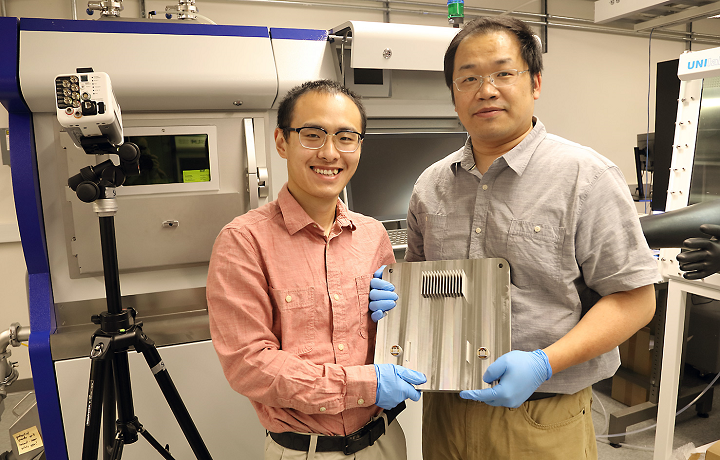
UVA materials science and engineering postdoctoral fellow Zhongshu Ren, left, and Tao Sun display the results of their research. Ren is the first author of the Science journal article. (Photo by Tom Cogill for UVA Engineering)
Laser powder bed fusion (LPBF) technology uses lasers and metal powder to 3D print parts, but porosity defects like keyhole pores are a challenge for fatigue-sensitive applications, such as aircraft wings. A collaborative research team, led by University of Virginia (UVA) associate professor of materials science and engineering Tao Sun, recently published a paper about their work using machine learning to detect the formation of these common defects in real-time. The size and formation of a keyhole is a function of scanning velocity, laser power, and a material’s capacity to absorb laser energy: if its walls are wobbly or collapse, the material solidifies around the keyhole, which traps the air pocket inside the new layer and makes the material more brittle and likely to crack under stress. The team integrated machine learning, near-infrared imaging, and operando synchrotron x-ray imaging to detect the thermal signature associated with keyhole pore generation with, as Sun said, “sub-millisecond temporal resolution and 100% prediction rate.”
“Porosity in metal parts remains a major hurdle for wider adoption of LPBF technique in some industries. Keyhole porosity is the most challenging defect type when it comes to real-time detection using lab-scale sensors because it occurs stochastically beneath the surface. Our approach provides a viable solution for high-fidelity, high-resolution detection of keyhole pore generation that can be readily applied in many additive manufacturing scenarios,” Sun explained.
rms Company Adds DMP Flex 350 Dual to Scale Medical Device Production
rms Company, one of the largest US-based contract manufacturers of tight-tolerance, high-quality medical devices, has added yet another printer from 3D Systems (NYSE:DDD) to its existing 30+ fleet. 3D Systems has been helping rms expand its direct metal printer portfolio over the last four years, and by adopting the DMP Flex 350 Dual into its production workflow, the company believes it can scale medical device production by expanding the types of implants it can produce and accelerating throughput. The most recent addition to 3D Systems’ Direct Metal Printing (DMP) portfolio, the DMP Flex 350 Dual is a two-laser system with all the benefits of the single-laser configuration, including quick-swap build modules and a central server to manage print jobs, materials, settings, and maintenance. It enables up to 50% productivity increases, and includes Oqton’s 3DXpert software, as well as a unique vacuum chamber that reduces argon gas consumption while also delivering high oxygen purity.
“The rms additive division owes a large part of our success to our customers. Over the past several years, our customers have come to expect a continual flow of high-quality, additively manufactured medical devices. Our Powder to Package solution provides a complete end-to-end value proposition that allows us to control the entire manufacturing and packaging process flow,” stated Troy Olson, Director of Oerations – Additive Manufacturing Division, rms Company. “A key element of our process flow is the reliability and performance we get from our stable of 30-plus 3D Systems’ DMP ProX ® 320 and DMP Flex 350 machines. Uptime on these machines is crucial for us to maintain our customer commitments. Our printers operate on a 24/7 production cadence, which leaves little room for downtime. 3D Systems has taken these first-in-class single laser platforms and have expanded on that technology with the DMP Flex 350 Dual. During our validation process, the DMP Flex 350 Dual showed no measurable differences in mechanical properties or dimensional accuracy. We are excited to add this new capability to our existing printing operation. As we continue to scale our additive manufacturing business, the 3D Systems DMP Flex 350 Dual will be at the forefront of our growth strategy.”
Subscribe to Our Email Newsletter
Stay up-to-date on all the latest news from the 3D printing industry and receive information and offers from third party vendors.
Print Services
Upload your 3D Models and get them printed quickly and efficiently.
You May Also Like
U.S. Navy Lab Uses 3D Printing to Reduce Tooling Lead Time By Over 90%
The F-35 Lightning II Joint Program Office (JPO), responsible for life-cycle management of the key fifth-generation joint strike fighter (JSF) system used by the U.S., its allies, and its partners,...
Etsy Design Rule Change Reduces Selection of 3D Printed Goods
Online marketplace Etsy has implemented a rule change requiring all 3D printed goods on the site to be original designs. The update to the site’s Creativity Standards states, ¨Items produced using...
Honeywell Qualifies 6K Additive’s Nickel 718 for 3D Printed Aerospace & Defense Parts
6K Additive is renowned for manufacturing sustainable additive manufacturing (AM) powder, and offers a wide portfolio of premium metal and alloy powders that include titanium, copper, stainless steel, and nickel,...
MetalWorm Sells WAAM Systems to Research Institutes in Brazil and Malaysia
Turkish WAAM firm MetalWorm has sold a system in Malaysia and another in Brazil. This is an excellent example of a few emerging trends in additive. Firstly, WAAM was experimented...