In 2011, Made In Space created the first 3D printer for microgravity; what sounded like science fiction suddenly became a reality. Since then, at least 15 experimental 3D printers have been tested aboard Zero-G flights worldwide. Powered by companies, academic institutions, and space agencies, this type of 3D printing research has been successful, from a few printers occasionally tested between 2011 and 2018 to half a dozen in 2022 alone.
Looking back at 2011, we might remember it as a year of transition for the space industry, chiefly because it was the beginning of the end for NASA’s Space Shuttle program, which took its final flight in July of that year. With a budget trim to go with it, NASA would soon turn to private industry for many of its space needs. One company, in particular, was keen to leave its mark. Known today as the firm that creates 3D printers for the International Space Station (ISS), Made In Space came out of Singularity University looking to fill a space manufacturing gap.
At its core, Made In Space founders believed that 3D printing and in-space manufacturing would “dramatically change the way we look at space exploration, commercialization, and mission design today.”
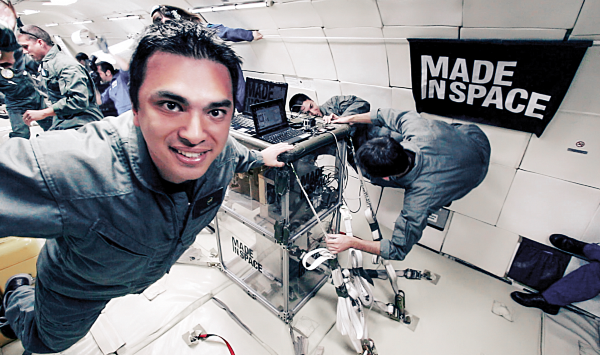
Like Made In Space (now part of Redwire), other companies also decided to test their 3D printing technology in parabolic flights. For example, in 2016, engineering firm and regular NASA contractor Techshot (also acquired by Redwire) partnered with manufacturer nScrypt to create the first microgravity bioprinter and tested it in an aircraft flown by the Zero Gravity Corporation, which operates weightless flights from U.S. airports.
Flying at 30,000 ft (roughly 9,144 meters) over the Gulf of Mexico, the plane simulated weightlessness while the bioprinter created cardiac and vascular structures using human stem cells. Like Made In Space, Techshot and nScrypt later sent the bioprinter to the ISS U.S. National Laboratory, where astronauts are using it for manufacturing human knee cartilage test prints and other human tissue.
The History of Manufacturing in Space
The idea of manufacturing in space has long posed several obvious challenges, primarily “gravity” issues, quality controls, and raw material sourcing. However, once in place, in-situ manufacturing has the potential to relax the dependence on resource resupply from Earth, making survival in space a little bit easier.
For decades, in-space manufacturing has been investigated as a method for producing parts and components in orbit that would otherwise be almost impossible to obtain immediately or at all. In the late 1960s, Soviet cosmonauts conducted the first welding experiments in space as part of their space manufacturing research. In the next decade, the United States began experimenting with space manufacturing in Skylab, the first space station launched by NASA.
But the gateway to space manufacturing lies in the investigations of parabolic flights that can reproduce gravity-free conditions in an aircraft right here on Earth. By alternating upward and downward arcs, they provide the necessary microgravity environment for scientists to conduct research without actually traveling to space. This simulated weightlessness may have started in the 1960s with the first flying space labs aboard U.S. military planes. Still, it has expanded to incorporate several private businesses, like US-based company Zero-G and French-based Novespace.
Parabolic Flights: A Pit Stop to 3D Printing in Orbit
With more options to recreate the unique weightlessness of space, we have witnessed a series of printers that have been successfully tested in parabolic flights. For example, in late 2016, Luke Carter of the Advanced Materials and Processing Laboratory (AMP Lab) at the University of Birmingham demonstrated metal 3D printing in microgravity aboard three separate parabolic flights. By creating a printing process much like directed energy deposition (DED), and using aluminum wire as feedstock, Carter and his team made a near-net shape part.
Then in 2017, the Canadian Reduced Gravity Experiment Design Challenge (CAN-RGX), supported by the National Research Council and the Canadian Space Agency, chose two teams to test their 3D printing experiments in parabolic flights. Team AVAIL (Analyzing Viscosity and Inertia in Liquids) from the University of Toronto built a system that controls the flow of a viscous liquid (corn syrup, in this case) through 15 different nozzles, and Team iSSELab (Interfacial Science and Surface Engineering Lab), hailing from the University of Alberta, collected data from 3D printing materials in a reduced gravity environment.
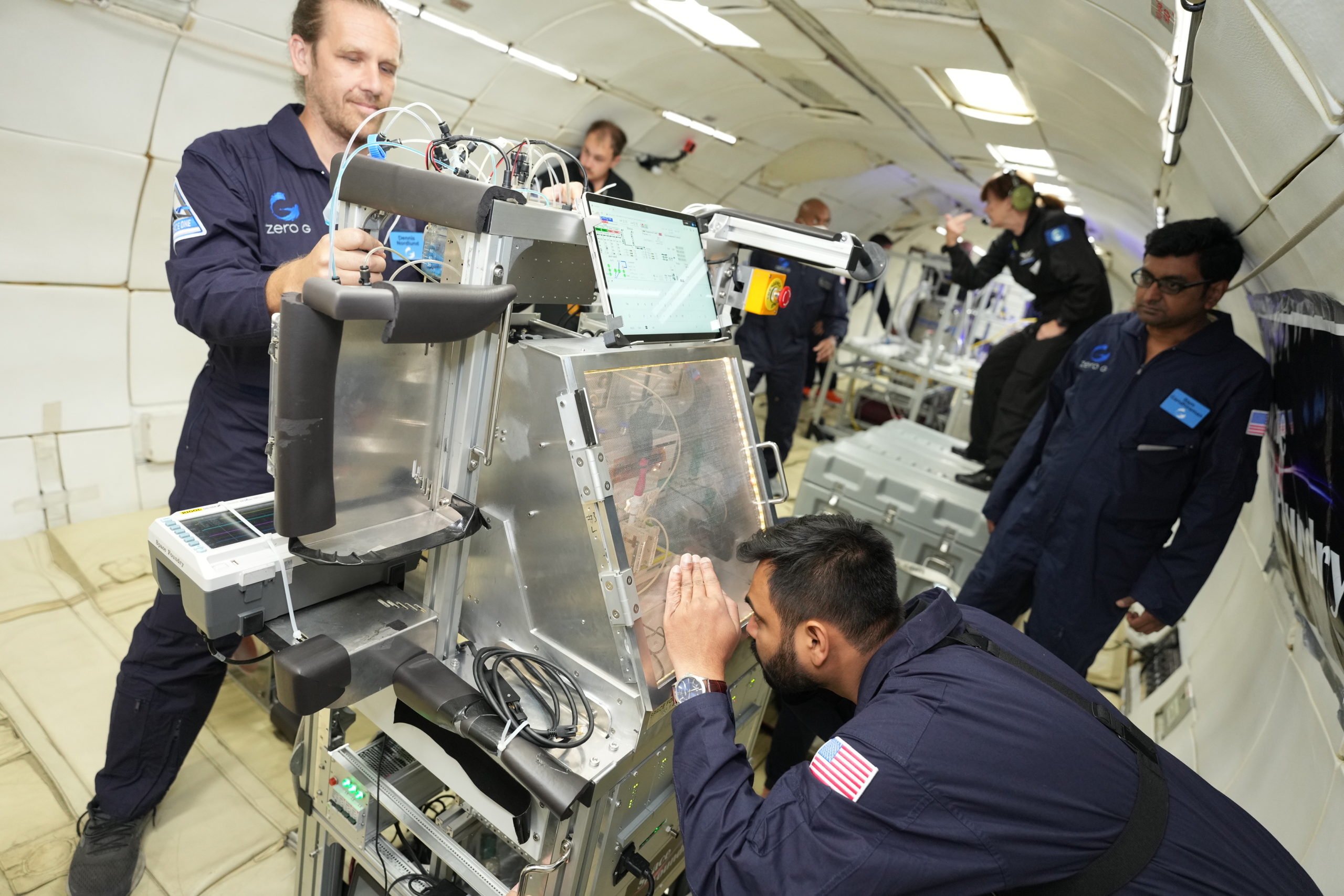
The following year, a European parabolic flight aircraft in New Zealand took scientists from the Technology and Engineering Center for Space Utilization of the Chinese Academy of Sciences (CAS) to test the first ceramic DLP 3D printer in microgravity. Following this successful event, NASA chose Associate Professor Gregory Whiting and his research group to test and model how 3D printing functional materials would work in lunar gravity. Whiting’s research group, the Boulder Experimental Electronics and Manufacturing Lab, geared up for two parabolic flights in 2021.
Around that time, engineering students of the Munich University of Applied Sciences built a 3D printer with an extruder to dispense a liquid photopolymer that took off on the European Space Agency (ESA)’s 74th parabolic flight campaign from Paderborn-Lippstadt Airport in Germany.
A few memorable 3D printing experiments in zero gravity in 2022 include Space Foundry’s testing of space-based electronic printing, supported by NASA’s Flight Opportunities and Small Business Innovation Research (SBIR) programs. In addition, UC Berkeley research teams tested the “replicator,” a light-based 3D printer, on May 10, printing more than 100 objects. Also, a German consortium tested out its patented 3D printing process and, for the first time, used metallic powders to 3D print in zero gravity.
This is just a taste of what is possible here on Earth, thanks to gravity-free flights. These and other experiments that took place in the last few years can be found below.
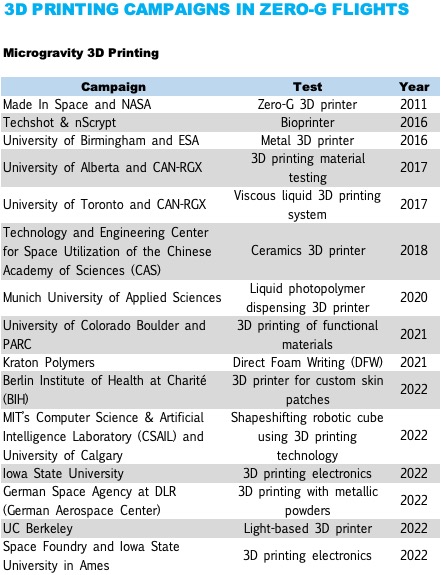
Subscribe to Our Email Newsletter
Stay up-to-date on all the latest news from the 3D printing industry and receive information and offers from third party vendors.
Print Services
Upload your 3D Models and get them printed quickly and efficiently.
You May Also Like
Consolidation in AM: How 2025 Is Shaping the Industry’s New Normal
The first half of 2025 has been marked by a clear shift in the additive manufacturing (AM) industry. Companies are no longer just focused on developing new tech by themselves....
Etsy Design Rule Change Reduces Selection of 3D Printed Goods
Online marketplace Etsy has implemented a rule change requiring all 3D printed goods on the site to be original designs. The update to the site’s Creativity Standards states, ¨Items produced using...
U.S. Congress Calls Out 3D Printing in Proposal for Commercial Reserve Manufacturing Network
Last week, the U.S. House of Representatives’ Appropriations Committee moved the FY 2026 defense bill forward to the House floor. Included in the legislation is a $131 million proposal for...
Transforming From Tourist to Native: Duro CEO Michael Corr Explains Why the Company Rebuilt its PLM Software on AI
In these early innings of the AI boom, many market analysts have expressed concern that AI spend has gotten too far ahead of the technology’s proven ability to deliver significant...