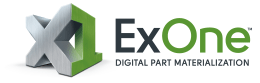
Critical replacement parts and difficult-to-source castings often suffer from the long lead times, most caused by the wait to procure traditional patterns or core boxes. The expensive acquisition of tooling machined from wood or metal for low-volume or one-off pours is often not cost effective.
Yet the most critical castings, often for infrastructure or transportation applications, are in high demand, and supply chain delays are increasingly common. Disruptive technologies are driving growth with the next generation of metalcastings.
Digital sandcasting using binder jet 3D printing eliminates the high-cost and months-long lead times of traditional foundry tooling. The sand 3D printing process uses digital data to replace tooling by printing molds and cores in sand directly from CAD files. No delays are caused waiting for new patterns to be created or core boxes to be repaired after years of storage. Legacy parts can be supplied without the upfront cost of creating new tooling to supply a single, yet critical, replacement metalcasting.
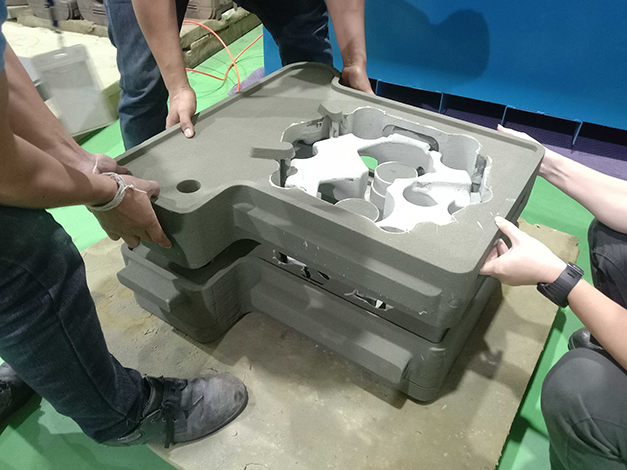
De-risked supply chains with sand binder jetting producing foundry molds and cores direct from digital models that drastically decrease lead times, tooling investment, and casting defects
Foundries, like producers in other industrial sectors, are benefiting from integrating 3D printing to solve supply chain challenges and are operating more efficiently while exceeding the expectations of customers by supplying rapid castings for replacement parts.
On-demand tooling enables decentralized production, a solution to help de-risk supply chains.
Sand 3D printing has been used in foundries for more than two decades to create metalcasting tooling and today’s binder jetting systems produce precision molds and cores at with production-volume output. An industrial printhead selectively deposits a binder into a bed of sand particles creating a solid part one thin layer at a time, similar to printing on sheets of paper.
ExOne works to help quantify the need for sand 3D printing technology to build a framework for the procurement of fast replacement metalcastings. Together with partners in various mission-critical industries, we are working to develop defined attributes and associated thresholds to establish a method of when it’s efficient and economical to source castings made from digital molds and cores.
The benefits of 3D printing can also be leveraged to improve the quality of hard to source components that often run into quality and consistency issues during casting. Building forms with binder jetting provides a design freedom that allows innovation in casting tooling – creating complex, consolidated geometries that enable lightweighting and optimized part performance not possible with traditional processes.
The design freedom of additive manufacturing unlocks benefits like core consolidation for reduced scrap or organic rigging features that help successful first pours to get precision critical castings into service fast.
Obsolete Part Replacement in Two Weeks – Sand 3D Printing to the Rescue
Marine engines operate in harsh environments with constant exposure to humidity and water, often salt water, that will deteriorate engine components. Because diesel engines create combustion from high cylinder pressure and heat, they must run at high compression ratios in order to generate enough heat to auto-ignite the diesel fuel.
Cylinder heads are critical components in the engine that support other important parts such as the fuel injectors and inlet and exhaust valves. Located on top of the liner flange and secured to the cylinder block with nuts and bolts, they are exposed to extremely high temperatures and pressures, expanding and contracting as the engine rapidly heats and as it cools.
Because of these environmental conditions, marine diesel engines must be built to withstand the extreme pressures involved with high cooling requirements.
Hi-Tech Marine Engineering, a shipyard in Thailand, was faced with a cylinder head with cracks caused by the large amount of stress from overheating. With a business that operates every day of the week, the cargo boat needed a fast repair to return to service, yet the broken component was nearly a decade old and no longer in production from the OEM supplier. “Time to delivery is critical in our business – we cannot wait for parts because we are in constant operation, so we need fast turnarounds on-budget,” said Aomthep CheinSuwan, Owner of HiTech Marine.
A traditional replacement part had a lead time of over 10 months and would come at a very high investment cost. Because the cylinder head is a legacy part without tooling, an entirely new pattern and core box set would have to be manufactured first to produce the replacement casting. Yet Hi-Tec Marine required a replacement part within four weeks any overseas order would require at least eight weeks with increased costs for shipping.
Speed 3D Mold, a casting and prototype development shop located in Thailand had the solution to offer a high-quality replacement part supplied with a fast turnaround. “For our customers in the maritime industry where there are many legacy parts that need replacement, speed is the most important factor for timely maintenance to keep systems in service,” said Nattinee Valun-araya, Head of Engineering at Speed 3D Mold
With over a decade of experience providing casting simulation support, sand 3D printing, and prototype and replacement casting, Speed 3D Mold’s engineering department supported Hi-Tech Marine with reverse engineering services. The team 3D scanned the original part to create a digital CAD file that could be used to develop a 3D printed mold and core package for casting a new component. With binder jet 3D printing no hard tooling is needed to create the replacement casting, rather the mold and cores are built layer by layer in sand directly from the CAD file.
With digital casting, Speed 3D Mold was also able to make fast iterations to the part to ensure the optimal quality for Hi-Tech Marine’s replacement cylinder head. The part contained many complex features, including large thickness differences and small cooling channels, yet could be easily modified with the digital casting process. The design freedom of additive manufacturing also allowed Speed 3D Mold to update the design of the cooling channel as well as freely place the rigging system within the mold without the traditional limitations to casting design.
The complex 725 x 630 x 572 mm mold package contained 19 pieces 3D printed on the S-Max binder jetting system in just 10 hours with no unexpected errors in dimension or shape.
The nearly 100kg replacement cylinder head was cast in gray iron and the final component was delivered to Hi-Tech Marine in just two weeks. The large capital investment to make tooling for just one replacement part would not have been economical, but Speed 3D Mold’s solution to directly print the mold package with ExOne sand binder jetting can save 40% compared to conventional production.
A traditional replacement casting carried a 10 month lead time for tooling —this replacement was produced with sand 3D printing and delivered in weeks
- A traditional replacement casting carried a 10 month lead time for tooling —this replacement was produced with sand 3D printing and delivered in weeks
Looking for more solutions to your complex production challenges? Register for our upcoming webinar, How 3D Printing Can Solve Supply Chain Challenges Today.
Subscribe to Our Email Newsletter
Stay up-to-date on all the latest news from the 3D printing industry and receive information and offers from third party vendors.
Print Services
Upload your 3D Models and get them printed quickly and efficiently.
You May Also Like
Johns Hopkins University Researchers Develop HyFAM Technology
Two scientists from Johns Hopkins University, Nathan C. Brown and Jochen Mueller, have developed a hybrid manufacturing technology they call HyFam, or Hybrid Formative Additive Manufacturing. Their work on this technology...
3D Printing G-Code Gets an Upgrade: T-Code
Good old G-Code still manages many 3D printers, great and small. Just like the STL, it’s a standard that enables collaboration while also holding the additive manufacturing (AM) industry back....
AM Rewind: The Biggest News and Trends of 2024
After a sluggish 2023, driven by persistent inflation and geopolitical tensions, 2024 has seen some recovery. Economic growth climbed from about 2.8 percent in 2023 to a modest 3.2 percent...
Metal Wire 3D Printer OEM ValCUN Announces Plans for 2025 Expansion
ValCUN, a Belgian original equipment manufacturer (OEM) of wire-based metal additive manufacturing (AM) hardware, has announced that the company has entered the next phase of its growth trajectory, making key...