Industrial 3D printing company EOS recently began a partnership with Sauber Technologies for its polymer 3D printing, but is definitely working to continue improving its metal 3D printing capabilities as well. Today, the company announced that its metal 3D printing materials portfolio for the M 290 printer has grown with the addition of four new materials. The mid-sized, powerful DMLS system already has quite an extensive materials portfolio, and the addition of these new stainless steel, tool steel, and nickel alloy materials will just make it stronger.
EOS has what it calls the Quality Triangle, which is a unique approach in our industry. The company takes the data from each of the three main technical elements of the AM production process—the system, the material, and the process—and assigns each combination a Technology Readiness Level (TRL). This designation makes the estimated production capability and performance of the solutions more transparent, so customers know just what they’re getting. Premium products (TRL 7-9) have a proven capability, highly validated process data, and reproducible part properties. TRL 3 and 5 are called core products, which means that they are less mature and with less data, but give customers early access to technology that’s still under development. These four new materials have all received a TRL 3 Core classification.
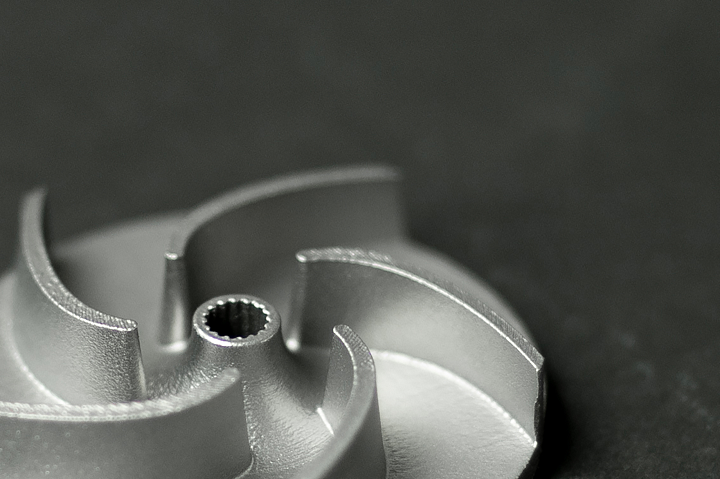
Impeller, 3D printed with austenitic EOS StainlessSteel 254 material, with excellent corrosion resistance
The first of these new materials is EOS StainlessSteel 254, well-suited for applications in extreme conditions, such as chemical handling equipment, pulp and paper manufacturing devices, and chlorinated seawater handling equipment. The austenitic stainless steel features high resistance to pitting, uniform, and crevice corrosion, and comes with a 40/60 µm process for the EOS M 290 printer. This material’s excellent corrosion resistance comes from its high chromium, molybdenum and nitrogen alloying, and EOS says it also features great stress corrosion cracking, as well as higher strength than conventional austenitic steel.
The other stainless steel material is EOS StainlessSteel SuperDuplex, for difficult environments. Optimized for AM, the austenitic-ferritic duplex stainless steel maintains “super duplex properties,” and also features high chromium, molybdenum and nitrogen alloying for great corrosion resistance.
Just like EOS’s other new stainless steel, StainlessSteel SuperDuplex shows great pitting, uniform, and crevice corrosion resistance. The company says this material also enables high strength, and that it’s great for applications in mining and offshore equipment, the oil and gas industry, and for pulp and paper manufacturing devices. It comes with a 40/80 µm process for the M 290, and due to what EOS calls the “optimization of phase balance,” this material can often be used in as-manufactured condition.
“Material development is always driven by customer demand and very often is the result of a close customer cooperation. These four new metal materials were designed and optimized specifically to the needs of additive manufacturing,” explained Sascha Rudolph, SVP BU Metal Materials at EOS. “We are increasing application opportunities for demanding industries by bringing AM tailored alloys to our customers.”
The new cobalt-free, ultra-high strength EOS ToolSteel CM55 is meant for use at elevated temperatures in tooling and engineering solutions. This high hardness steel has a 40/80 µm process for the EOS M 290 printer, and the combination of its moderate carbon content and alloying elements have formed a stable, strong structure for more demanding applications, such as powertrain components, cold and hot working tools, and parts for mechanical engineering.
Finally, the last new material, EOS NickelAlloy HAYNES 282, is also meant for 3D printing parts for applications at elevated temperatures. Manufactured under license from Haynes International Inc., this precipitation strengthened, nickel-based superalloy powder was developed specifically for high-temperature structural applications, such as energy industry components, turbomachinery and gas turbine parts, and aerospace and rocket engine components. It features what EOS calls a “unique combination” of thermal stability, excellent weldability, good oxidation and corrosion resistance, and high temperature strength.
Subscribe to Our Email Newsletter
Stay up-to-date on all the latest news from the 3D printing industry and receive information and offers from third party vendors.
Print Services
Upload your 3D Models and get them printed quickly and efficiently.
You May Also Like
3D Printing News Briefs, July 2, 2025: Copper Alloys, Defense Manufacturing, & More
We’re starting off with metals in today’s 3D Printing News Briefs, as Farsoon has unveiled a large-scale AM solution for copper alloys, and Meltio used its wire-laser metal solution to...
3DPOD 260: John Hart on VulcanForms, MIT, Desktop Metal and More
John Hart is a Professor at MIT; he´s also the director of the Laboratory for Manufacturing and Productivity as well as the director of the Center for Advanced Production Technologies....
3D Printing News Briefs, June 28, 2025: Defense Accelerator, Surgical Models, & More
In this weekend’s 3D Printing News Briefs, 3YOURMIND was selected to join an EU Defense Accelerator, and PTC has announced model-based definition (MBD) capabilities within Onshape. Finally, a study out...
EOS in India: AM’s Rising Star
EOS is doubling down on India. With a growing base of aerospace startups, new government policies, and a massive engineering workforce, India is quickly becoming one of the most important...