A Belgian consortium consisting of Ghent University, KU Leuven, and research organization VITO has been working on the Additive Manufacturing for Electrical Machines (AM4EM) project. They want to make more energy-efficient electrical motors. Startup Additive Drives along with several companies in the automotive supply chain are taking a hard look at 3D printing electrical motors, windings, and motor components. This can have a much broader impact than cars though with many motors finding their way into bikes, industrial equipment, and many other things that populate our daily lives.
The group is specifically looking at 3D printing stators and rotor cores. In electric motors typically the stator has magnets in it while the rotor has windings in it that carry current. There is an air gap in between the two while a bearing lets the rotor spin smoothly inside the stator. The windings are wound in different directions and current is passed through them. The magnets exert forces on these windings in different directions which creates torque causing the rotor to spin while the current is applied. There are millions of DC and AC motors in the world and they can be super small or the size of rooms. Generally, people have optimised the parts, geometries, and designs of these things quite well over the past 100 years.
What the trio of Belgian research groups is trying to do is to apply multi material 3D printing to motors. With multi material 3D printing, we can deposit different materials, mix them, and create different configurations of these materials or layers with different materials in them. They hope that through doing this they can come upon methods to make more efficient motors that optimise the magnetic fields or forces at play in ways that have not been possible so far.
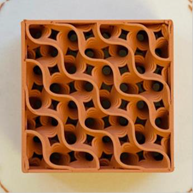
A copper print by VITO
Vito has been researching 3D printing since 2006 and is particularly interested in printing pastes using ceramics, metals and polymers. One sign of progress is that the team has paste printed pure copper, demonstrating the “Micro-extrusion 3D-printing of copper paste has led to printed parts without printing defects, a relative density of 95 – 99% and an impressive electrical conductivity of 90 – 102% IACS [International Annealed Copper Standard].”
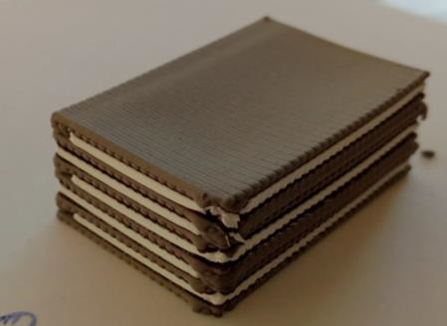
A Fe-Si print by VITO
The team has also printed a Fe-Si (also called electrical steel, often used as a motor core material). Now the team is working on printing parts for the core where ceramic is printed in one layer followed by a Fe-Si layer. For now, they have significant warp and shrinkage but they hope to be able to optimise cores.
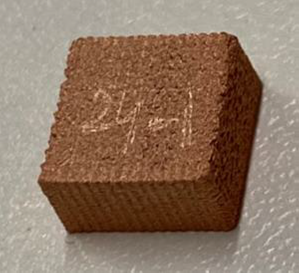
A bound metal filament copper print by the KU Leuven
Whereas VITO focused on paste extrusion, KU Leuven is working on FDM for metal and ceramics similar to the bound metal process used by Desktop Metal, Nanoe and Markforged. Here they also tried to mix materials in one print. Ghent University in turn is working on the design optimisation of the motors to enhance magnetic flux. The trio hopes to increase the energy efficiency of their motors by 5% and have a power density increase of 40% at the end of their project.
I really like this approach. Given the sheer volume and importance of electrical motors, a small improvement will potentially have a big impact. Now of course if we just have a marginal impact then it will be tough to impossible to get battery makers to switch to our technology. If the impact is significant enough we’re still going to have an advantage that could cover the trouble and costs of adopting a new production technology. What is also potentially very fruitful is that the filament process and paste process being used here are inexpensive. They could both be very cost effective technologies to implement at a very large scale. They’re finicky at the moment but do show promise. They would need a lot of automation especially since they need a separate debunking and sintering step. But, if this is overcome, then they could very well make quite cost effective parts.
Images courtesy of VITO, KU Leuven and Ghent University.
Subscribe to Our Email Newsletter
Stay up-to-date on all the latest news from the 3D printing industry and receive information and offers from third party vendors.
Print Services
Upload your 3D Models and get them printed quickly and efficiently.
You May Also Like
3D Printing News Briefs, July 2, 2025: Copper Alloys, Defense Manufacturing, & More
We’re starting off with metals in today’s 3D Printing News Briefs, as Farsoon has unveiled a large-scale AM solution for copper alloys, and Meltio used its wire-laser metal solution to...
3DPOD 260: John Hart on VulcanForms, MIT, Desktop Metal and More
John Hart is a Professor at MIT; he´s also the director of the Laboratory for Manufacturing and Productivity as well as the director of the Center for Advanced Production Technologies....
3D Printing News Briefs, June 28, 2025: Defense Accelerator, Surgical Models, & More
In this weekend’s 3D Printing News Briefs, 3YOURMIND was selected to join an EU Defense Accelerator, and PTC has announced model-based definition (MBD) capabilities within Onshape. Finally, a study out...
EOS in India: AM’s Rising Star
EOS is doubling down on India. With a growing base of aerospace startups, new government policies, and a massive engineering workforce, India is quickly becoming one of the most important...