The Biden administration recently announced a slew of new opportunities for increasing the adoption of additive manufacturing (AM) across the U.S. Initial participating companies of the AM Forward program are already well-steeped in military applications of the technology, signaling that industrial AM will likely continue to be led by those in the defense sector. This was further demonstrated by new collaborations between the U.S. Air Force (USAF) and established 3D printing firms GE and Optomec.
GE Aviation and Pacer Edge
With GE, the USAF has been working on its ‘Pacer Edge’ pathfinder program, dedicated to the use of metal AM for maintenance and operation of aircraft. Nearly a year ago, this resulted in the first jet engine part fabricated with metal 3D printing to be qualified by any Department of Defense body. The item was a replacement for a legacy part that was previously cast, a sump cover for the F110 engine, used on F-15 and F-16 fighter jets.

Left: A hand-drawn technical illustration of the cross-shaft arm dating from the 1960s. Image Credit: USAF. Right: The first successful development build of the cross-shaft arm was printed nine months after requirement flow down. Image Credit: GE.
Now, the partners enter the third phase of their program, focusing on four obsolete parts: a bellcrank, gearbox seat, anti-icing valve body, and a cross shaft arm. So far, GE has 3D printed the cross shaft arm and the bellcrank from cobalt-chrome on an M2 Series 5 system at GE Additive‘s facility in Cincinnati.
In addition to completing the final two parts, GE and USAF will work to establish additive production infrastructure at Tinker Air Force Base in Oklahoma. The goal is to alleviate supply chain issues related to casting and forging by relying on metal AM.
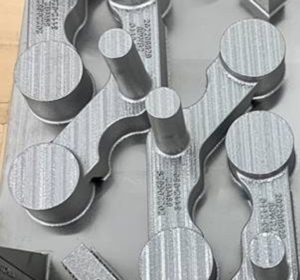
Metal 3D printed production parts for the Pacer Edge program (printed in cobalt-chrome and nickel alloy 718 on GE Additive’s Concept Laser M2) nine months after requirement flow down. Image Credit: GE Additive
“Pacer Edge represents a monumental step forward in innovative partnership with industry. Through this program, our enterprise team will deliver safe and timely propulsion readiness in support of the United States warfighter,” said Mr. John Sneden, Director of Propulsion, USAF.
“Public-private initiatives like the recently announced ‘AM Forward’ initiative will also help to address DoD’s sustainment and readiness challenges head on. Strengthening U.S. supply chains, by encouraging small and medium sized manufacturers across the United States to adopt metal additive technology, will create a nationwide network of a qualified additive manufacturing suppliers,” said Lauren Tubesing, Director of Operations, Military Programs at GE Additive.
Optomec Repairs Blisks with DED Metal 3D Printing
In addition to collaborating with GE, the USAF has awarded Optomec a $1.5 million contract dedicated to the development of a metal 3D printer for repairing “oversized titanium components used in aircraft engines.” Optomec’s version of directed energy deposition (DED), LENS, was originally developed for aircraft repair, making the company any ideal candidate.
The first components to be targeted are integrally bladed rotors (referred to as “blisks”). These rotors are made up of a single, complex unit made from lightweight titanium alloy. Regularly damaged and subject to wear-and-tear, blisks can cost over $500,000 to replace. With 3D printing, it is projected that more than 80 percent of cost savings can be achieved, resulting in tens of millions of dollars in maintenance savings by the USAF. Additionally, 3D printing will shorten the supply chain for producing parts for the Air Force before being applied to the larger commercial aviation market.
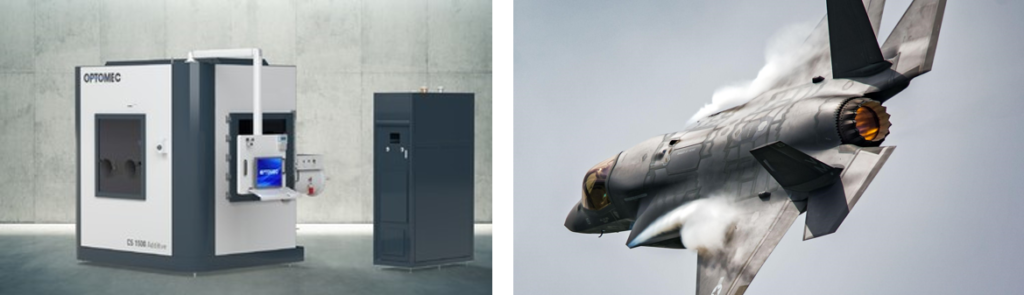
The Optomec Additive Manufacturing system, projected to reduce Titanium blisk repair costs by 80%. Images courtesy of Optomec.
“As OEMs lightweight and simplify their commercial and military aircraft engine designs, the industry is faced with larger, more complex titanium parts to maintain on the MRO side.” said Jamie Hanson, Optomec’s VP of Business Development, “Optomec is best positioned to deliver production solutions to this growing need, based on its proprietary machine, software and process capabilities, combined with its existing position as the market leader delivering machines for production repair of individual turbine blades. There’s no question that this project with the Air Force will benefit the broader aerospace market significantly over the next ten years.”
The contract specifies that the system will be a five-axis LENS DED machine with a massive build envelope of 1500 x 1500 x 1000 mm (5 x 5 x 3 ft). This will make it possible to work with blisks of up to 46” in diameter. A proprietary gas purification system will protect the work environment from oxygen and moisture to ensure the proper metallurgical and mechanical properties are achieved. Optomec will also explore the use of process monitoring techniques for validation and quality assurance. Upon proving the ability to repair wear and foreign object damage on critical areas of blisk blades, Optomec will repair a large-scale blisk that will be evaluated in a spin pit test.
As the AM Forward program kicks off, we’re sure to see more projects like this, but with increasing crossover between the military and aerospace sectors with other manufacturing areas. We can imagine Optomec’s blisk repair project on a large scale, as small and medium businesses receive contracts and grants to adopt additive to support the defense companies involved in AM Forward.
Subscribe to Our Email Newsletter
Stay up-to-date on all the latest news from the 3D printing industry and receive information and offers from third party vendors.
Print Services
Upload your 3D Models and get them printed quickly and efficiently.
You May Also Like
The Dental Additive Manufacturing Market Could Nearly Double by 2033, According to AM Research
According to an AM Research report from 2024, the medical device industry, specifically in dentistry, prosthetics, and audiology, is expected to see significant growth as these segments continue to benefit from...
Heating Up: 3D Systems’ Scott Green Discusses 3D Printing’s Potential in the Data Center Industry
The relentless rise of NVIDIA, the steadily increasing pledges of major private and public investments in national infrastructure projects around the world, and the general cultural obsession with AI have...
AM Research Webinar Explores Continuum’s Sustainable Metal Additive Manufacturing Powders
Metal additive manufacturing (AM) powder supplier Continuum Powders is working to develop solutions that empower industries to reduce waste and optimize their resources. An independent life cycle assessment (LCA) of...
3D Printed Footwear Startup Koobz Lands $7.2M in Seed Round
California-based Koobz is focused on reshoring the U.S. footwear supply chain with advanced manufacturing processes, including 3D printing. The startup just announced that it has added $6 million to its...