Replique, part of the BASF venture builder, is establishing a 3D printing materials network to advance the production of 3D printed parts. This partner network of authorized material vendors is meant to ensure a set of standards among all members. In turn, customers of Replique’s digital inventory platform, as well as users of these materials in general, will be assured that the polymers are of a certain quality.
As a spinout of the world’s largest chemical company, Replique has the resources and reach to become a powerful player in the world of 3D printing services. So far, it has provided 3D printing of spare parts for German appliance manufacturer Miele. Now, by partnering with a series of companies beyond BASF, it will be able to extend its reach.
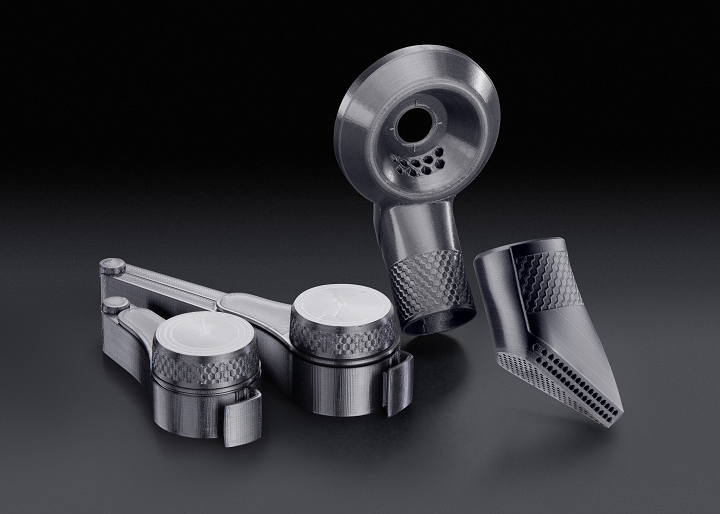
Four Miele accessories are produced so far using Replique’s platform: A coffee clip in two sizes, a borehole cleaner, and a valuable separator (Source: Miele).
The partner network will begin with LEHVOSS Group, Evonik Industries, BASF Forward AM and igus GmbH. The firms are collaborating to ensure that standards related to development, manufacture, and certification of materials are in place to qualify 3D printed spare parts. This will be performed in part through an automated quality documentation process, which will result in a certificate of analysis verifying that the material meets the required specifications. This certificate is linked to each part and saved on Replique’s digital inventory platform.
In addition to enabling this validation, Replique will also analyze customer business cases and requirements and adjust, improve, or develop materials to meet those needs. Material partners will be able to see an anonymized overview of legacy feedstocks from when customers were onboarded. That way, partners can more directly develop materials for those customers. This allows material companies business cases, while customers are able to access the latest feedstock developments, including chemistries made just for their applications.
“With our trusted material network, we have created a solution to provide our customers with industrial grade material systems. Overall, the cooperation will transform the usability of 3D printing beyond prototyping towards serial production and industrialization, e. g. by achieving a faster part qualification through close iterations with material development, certifications and replacement of legacy materials. Our aim is to find the best solution for our clients,” says Dr. Max Siebert, CEO and Co-Founder of Replique.
“Through the partnership with Replique we can determine and offer the best material formulations for professional end user applications. The information given by Replique helps us to broaden our reach and to generate superior material solutions,” says Dr. Stefan Schulze, Director 3D Printing Materials at LEHVOSS Group.
All industry consortia work in part as a gatekeeping and lobbying group, just by their very design. Combining forces necessarily strengthens their power so that, when a trade issue arises, the consortium can work together to address those issues, whether they be related to national laws, tariffs, or otherwise.
If the group achieves a high enough status, it can become a de facto arbiter of standards, even if it is not a public body. For instance, UL is one of the major safety standards organizations in the world, despite the fact that it is not a government or public organization. In turn, it becomes necessary for those wishing to participate in that industry to obtain the validation of this organization. Therefore, if a materials network like that being launched by Replique becomes the de facto standard, it will be able to set the rules for the industry. This is the name of the game as industrial giants increasingly enter the 3D printing space. As AM industrializes, industry will control AM.
This is just the beginning for the network. Replique plans to broaden its material partners to include both polymers and materials.
Subscribe to Our Email Newsletter
Stay up-to-date on all the latest news from the 3D printing industry and receive information and offers from third party vendors.
Print Services
Upload your 3D Models and get them printed quickly and efficiently.
You May Also Like
The Dental Additive Manufacturing Market Could Nearly Double by 2033, According to AM Research
According to an AM Research report from 2024, the medical device industry, specifically in dentistry, prosthetics, and audiology, is expected to see significant growth as these segments continue to benefit from...
Heating Up: 3D Systems’ Scott Green Discusses 3D Printing’s Potential in the Data Center Industry
The relentless rise of NVIDIA, the steadily increasing pledges of major private and public investments in national infrastructure projects around the world, and the general cultural obsession with AI have...
AM Research Webinar Explores Continuum’s Sustainable Metal Additive Manufacturing Powders
Metal additive manufacturing (AM) powder supplier Continuum Powders is working to develop solutions that empower industries to reduce waste and optimize their resources. An independent life cycle assessment (LCA) of...
3D Printed Footwear Startup Koobz Lands $7.2M in Seed Round
California-based Koobz is focused on reshoring the U.S. footwear supply chain with advanced manufacturing processes, including 3D printing. The startup just announced that it has added $6 million to its...