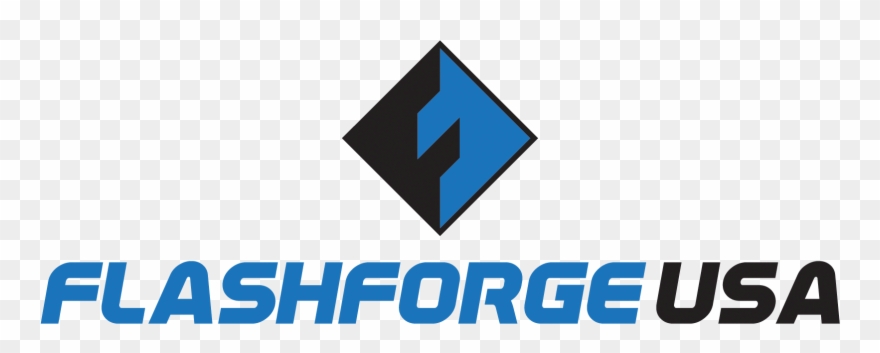
Nearly two and a half years after the initial release of the popular Adventurer 3, Flashforge has come out with a refresh that offers several upgrades to improves the printing experience and capabilities. Touted as the next generation in the Adventurer series lineup, Adventurer 4 boasts features at the mid-tiered price point that will give users their money’s worth, such as an auto-leveling print bed, a much larger build area, and an extruder that can use a variety of materials.
A versatile machine that caters to a broad audience base
Flashforge is a global 3D printer brand and one of the pioneers of bringing 3D printing to consumers through its printer quality and price. Founded in 2011, Flashforge first offered 3D printers to at-home hobbyists and tinkers and has since expanded its footprint to provide printers for businesses, schools, and even the government.
Adventurer 4 is an all-around printer aimed at a broad user base. Beginners can tap into the world of 3D printing right out of the box, and as printing skills grow, Adventurer 4 is able to accommodate more advanced print jobs also. It is also just as capable being used in business environments for applications such as prototyping, production lines, and more. Flashforge USA partnered with Layerbylayer to provide a 3D printing curriculum bundle, so schools can leverage Adventurer 4 to provide 3D printing lessons in classrooms.
More than a good-looking machine
Flashforge has kept its design cue the same for the most part. On the outside, Adventurer 4 can easily be identified as part of the Adventurer series lineup. Those coming from the previous generation will find a much larger footprint that extends to the build chamber as well. At 220 x 200 x 250mm (8.7 x 7.9 x 9.8 in), Adventurer 4 has a build volume that is over 2x its predecessor. Inside the chamber, there is a HEPA 13H air filter that can effectively eliminate 99% of TVOC powder and activated carbon filter odor. It is also fully enclosed with a see-through door in the front. Removing the side panel reveals the filament tray that can accommodate 1kg spool.
Based on FFF (fused filament fabrication) technology, Adventurer 4 uses filament extrusion method to print objects. It can use a variety of materials ranging from the standard ABS, PLA, PETG to PC, PLA-CF, PETG-CF, ASA, and more. Depending on the filament used, extrusion temperature will need to vary. Adventurer 4’s versatile single extruder has a maximum temperature of 265°C (509°F) and uses a patented buckle design that allows users to quickly swap between different Flashforge nozzles. In addition, the nozzle can reach 200°C (392°F) in just 60 seconds, saving users time between prints.
An intelligent self-leveling platform
Flashforge Adventurer 4 is one of the few printers on the market that offers true auto-leveling print bed. Compared to manual or assisted bed leveling, time is saved from having to align the bed. The flexible magnetic plate can also heat up to 110°C (230°F) to accommodate different types of filament.
Other notable features
Adventurer 4 uses the latest FlashPrint software from Flashforge. The printer can be monitored remotely through FlashPrint and the build-in camera. Multiple printers can also be connected to form a production line. Adventurer 4 also features filament run out detection and resume print from power outages, so print jobs will not be interrupted.
Technical specification
Print Technology FFF (Fused Filament Fabrication)
Number of extruders 1
Print volume 220 x 200 x 250 mm (8.7 x 7.9 x 9.8 in)
Printer Dimension 500(L) x 470(W) x 540(H) mm, (19.7 x 18.5 x 21.3 in)
Connectivity USB, Wi-Fi, Ethernet, and Cloud Printing
Adventurer 4 is available today and can be purchased directly from Flashforge USA with fast delivery from its facility in Southern California.
Subscribe to Our Email Newsletter
Stay up-to-date on all the latest news from the 3D printing industry and receive information and offers from third party vendors.
Print Services
Upload your 3D Models and get them printed quickly and efficiently.
You May Also Like
Reinventing Reindustrialization: Why NAVWAR Project Manager Spencer Koroly Invented a Made-in-America 3D Printer
It has become virtually impossible to regularly follow additive manufacturing (AM) industry news and not stumble across the term “defense industrial base” (DIB), a concept encompassing all the many diverse...
Inside The Barnes Global Advisors’ Vision for a Stronger AM Ecosystem
As additive manufacturing (AM) continues to revolutionize the industrial landscape, Pittsburgh-based consultancy The Barnes Global Advisors (TBGA) is helping shape what that future looks like. As the largest independent AM...
Ruggedized: How USMC Innovation Officer Matt Pine Navigates 3D Printing in the Military
Disclaimer: Matt Pine’s views are not the views of the Department of Defense nor the U.S. Marine Corps Throughout this decade thus far, the military’s adoption of additive manufacturing (AM)...
U.S. Congress Calls Out 3D Printing in Proposal for Commercial Reserve Manufacturing Network
Last week, the U.S. House of Representatives’ Appropriations Committee moved the FY 2026 defense bill forward to the House floor. Included in the legislation is a $131 million proposal for...