According to a study published in February 2022 titled “The First Environmental Evaluation of 3D-Printed Footwear,” the current standard production process involved in footwear manufacturing leads to “an industry where one out of every five shoes made goes unsold.” In a way, it’s almost surprising the percentage isn’t higher, given the wastefulness of the fashion industry in general. Nonetheless, this fact — and the study as a whole — encapsulates the significant extent to which an industry that has long been rightly criticized for its appalling labor abuses, is also detrimental to the planet in ecological terms.

The study was done by a team of graduate students at Yale’s Center for Business and the Environment, with assistance and data from the Portland, Oregon-based 3D-printed footwear startup HILOS, as well as HILOS’ supply chain partners, BASF Forward AM, HP 3D Printing, and Additive Manufacturing Technologies (AMT). HILOS uses HP’s Multi Jet Fusion to turn BASF Ultrasint TPU filament into platforms for shoes made from veg-tanned leather. “The First Environmental Evaluation of 3D-Printed Footwear” focuses on three central questions:
- “How does 3D-printed footwear compare to legacy shoemaking?”
- “Where does the technology have the potential to deliver the greatest environmental impact?”
- “Where are the greatest opportunities for future improvement, and how do we get there?”
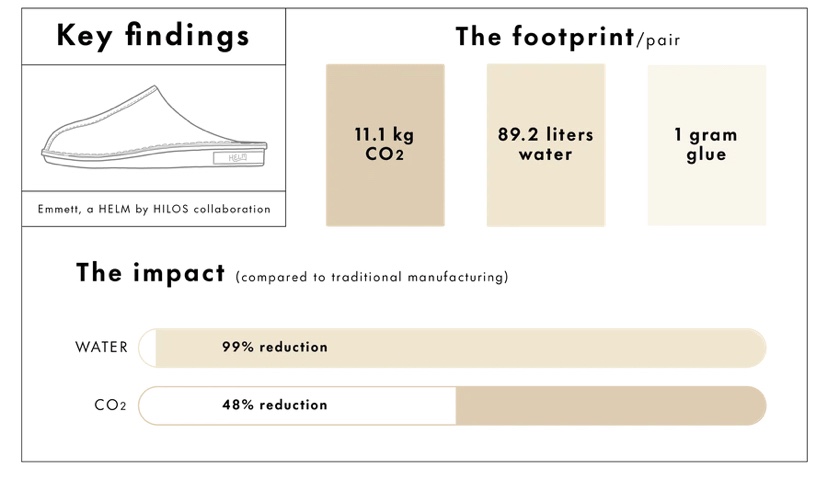
The study compares 3D-printed shoemaking to “legacy” shoemaking in categories such as CO2 emissions, water usage, and parts and labor devoted to the manufacturing process. Overall, its most important conclusion is that, at present, the ability to use 3D printing to consolidate the supply chain is the technology’s greatest potential advantage for mitigating environmental damage caused by the footwear industry.
As the study’s author puts it, “By reducing part count and streamlining product assembly, 3D printing reduces overall emissions by 48% even with lower economies of scale.” In addition, 3D printing can help fix the footwear supply chain — and thus, help the industry become more ecologically sustainable — for the simple reason that on-demand production means that just about every pair of shoes made will be sold and worn. The author writes, “Selling the same amount of shoes while actually producing less has an enormous impact on supply chain efficiency across every step of the process, avoiding both the initial material usage as well as the accompanying waste resulting from each step.”
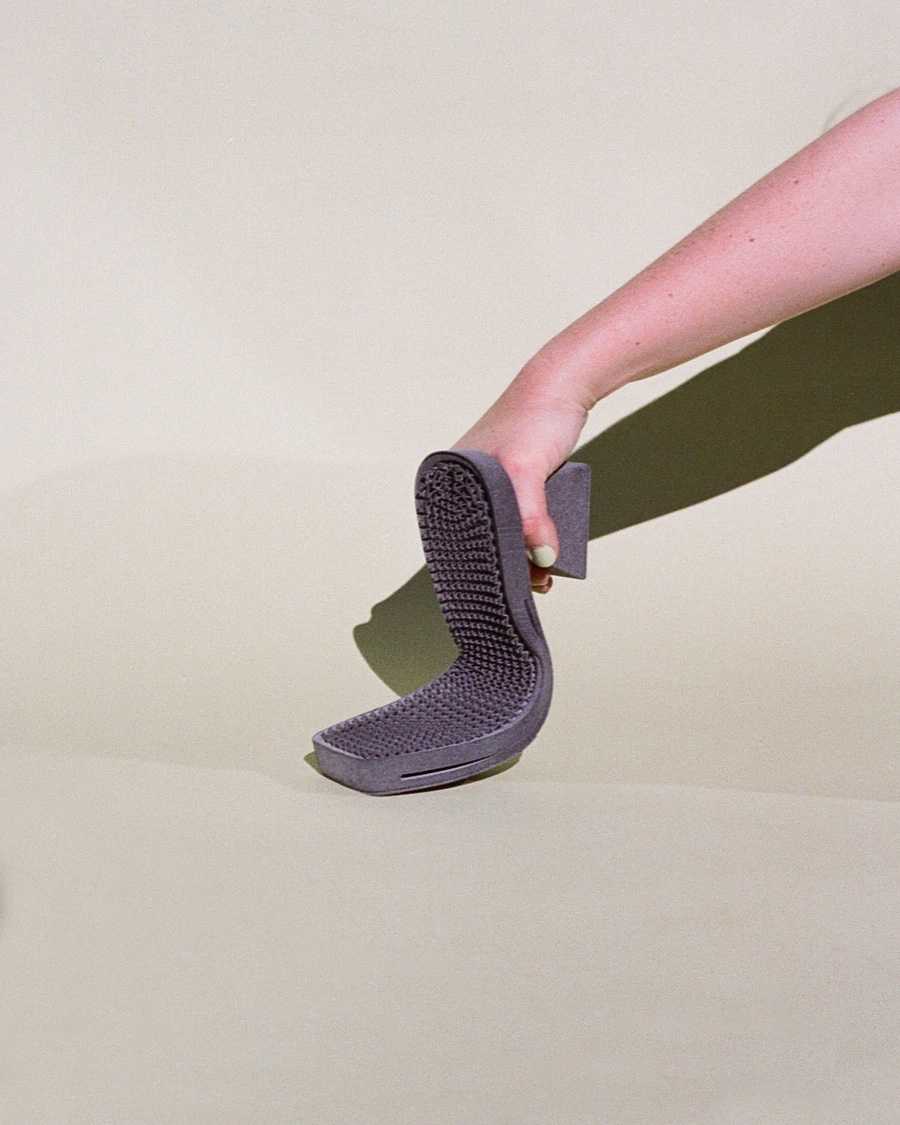
As far as life cycle assessments (LCAs) go, this one is pretty readable (if you’re into that sort of thing), and the main points it brings up elucidate factors that would be relevant to researchers working on any LCA related to 3D printing. Especially impressive is the grasp of prioritizing HILOS displays in its understanding of the elements at stake here. For instance, while noting the advances HILOS has already made in the area of economic circularity, the company also concluded that any current progress that could be made with 3D printing in terms of the renewability of materials and recycling don’t come close to the progress that would be achieved by minimizing the carbon emissions of the supply chain.
Thus, instead of trying to solve every problem at once, HILOS endorses an approach of focusing on the digital supply chain first, and then using the success hopefully attained on that front to start addressing other areas. Once 3D printing has succeeded at reducing costs and emissions associated with the inefficient supply chain of legacy shoemaking, companies can then “reinvest this margin back into manufacturing, in turn increasing the quality, durability, and longevity of product delivered and further reducing returns.”
Fortunately for HILOS, it has so far been successful in pushing its brand. The startup just won Best in Show at SXSW. With this momentum, hopefully it can achieve that vision. This type of thinking shows the type of strategic foresight that every company in the 3D printing sector should be striving for.
Subscribe to Our Email Newsletter
Stay up-to-date on all the latest news from the 3D printing industry and receive information and offers from third party vendors.
Print Services
Upload your 3D Models and get them printed quickly and efficiently.
You May Also Like
Consolidation in AM: How 2025 Is Shaping the Industry’s New Normal
The first half of 2025 has been marked by a clear shift in the additive manufacturing (AM) industry. Companies are no longer just focused on developing new tech by themselves....
Etsy Design Rule Change Reduces Selection of 3D Printed Goods
Online marketplace Etsy has implemented a rule change requiring all 3D printed goods on the site to be original designs. The update to the site’s Creativity Standards states, ¨Items produced using...
U.S. Congress Calls Out 3D Printing in Proposal for Commercial Reserve Manufacturing Network
Last week, the U.S. House of Representatives’ Appropriations Committee moved the FY 2026 defense bill forward to the House floor. Included in the legislation is a $131 million proposal for...
Transforming From Tourist to Native: Duro CEO Michael Corr Explains Why the Company Rebuilt its PLM Software on AI
In these early innings of the AI boom, many market analysts have expressed concern that AI spend has gotten too far ahead of the technology’s proven ability to deliver significant...