Boston Micro Fabrication is expanding to two new facilities in Massachusetts, U.S. and Shenzhen, China. The company also reported that it has acquired an additional 100 customers in 2021, taking its total to 200. The Massachusetts facility is in Maynard and will be the firm’s headquarters. In Shenzhen, the company will have a facility that includes over 40 of its 3D printers.
“Micro 3D printing is beginning to catch fire around the world. For years, this portion of the market was under-served by existing additive manufacturing platforms as the resolution and accuracy needed for micro parts was not possible. Our microArch platform finally brings 3D printing and miniaturization to these industries that were once left out completely – and our expanded presence helps us support these use cases no matter where our customers are located,” John Kawola, CEO of BMF, said.
These customers use projection micro stereolithography (PµSL) to make parts usually for research, but also in fields such as medical device, microfluidics and electronics production. One of their customers is Dutch company Sonion NL. Sally van der Most, their Development Support Services Manager, said:
“The quality and accuracy of BMF PµSL parts is very unique, and truly mimic expensive micro molded parts, but now we can have parts ready for test within 1-2 days rather than 1-2 months, as well as levitating the huge costs associated with tooling manufacture and reworking as the new products evolve. We can also explore designs previously out of reach due to manufacturing limitations. Our main focus is to lift our prototyping capabilities to the highest possible level, both in quality and speed. BMF will help us to accomplish that.”
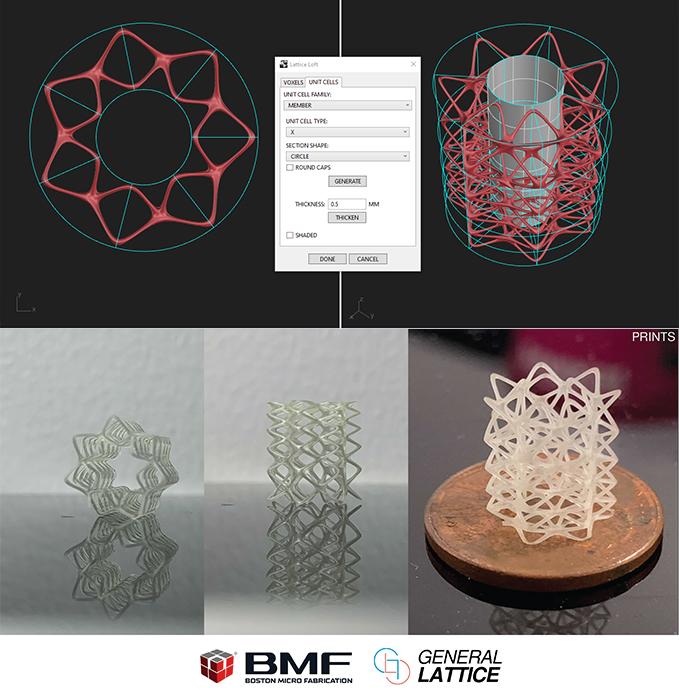
BMF is certainly showing a lot of gumption here by expanding so quickly into a promising Chinese market. The firm’s stereolithography technology is also potentially very scalable, as well. Individual 3D printers such as its microArch platform could be used to make hundreds of thousands of parts a year. In the medical device space, hundreds of thousands of tiny 3D printed polymer and metal parts are being used right now. There is a lot of potential to be had for markets similar to medical devices, as well as precision components needed for surgical robots and other similar applications. The micro 3D printing companies do have a much more significant volume potential however. In electronics or polymer components for our ever more tightly packed cell phones, there could potentially be many millions of parts in the offing. Hearing aids, microphones and headphones will also be a bigger market for them going forward.
It is still very early days yet for micro- and nanoprinting and the potential is considerable, including for optics, high-end electronics, and defense applications. If they can make parts cost effective enough for truly high-volume work remains to be seen. At the moment, BMF is replacing micro molding in certain tools and assemblies where this is advantageous because of the geometry, production run, or the economics of their system as compared to molding. In this case, companies can often have real cost advantages through directly 3D printing these parts. This is a relatively straight forward, short sales cycle path to making components and selling things to customers. Rather than try to convince people that they should invest in a machine they can just bid on production runs of parts and get volume business this way. Then later the company could scale towards getting a machine.

A 3D printed cardiovascular stent made using BMF technology. Image courtesy of BMF.
The scale of the company’s ambition and its direction is shown by opting to start in Asia in Shenzhen. The city is a maelstrom of making things and is the global HQ of the electronics industry. In Shenzhen, you can find any part for any application. By putting in its service there, the company is aiming squarely to be a solutions provider for electronics manufacturing.
Rather than opt for more high-end applications or to grow in medical, the company is here going for volume. I like that this approach will force them to be cost effective and have to deliver on volumes by a certain date. This should make them and their equipment much better, exposing them to the cliff face of capitalism that Shenzhen is. I do worry that, at one point, their technology may lead to Shenzhen Micro Fabrication and other similar copycat firms, especially since BMF fits so well in China’s future economic plans.
Subscribe to Our Email Newsletter
Stay up-to-date on all the latest news from the 3D printing industry and receive information and offers from third party vendors.
Print Services
Upload your 3D Models and get them printed quickly and efficiently.
You May Also Like
Reinventing Reindustrialization: Why NAVWAR Project Manager Spencer Koroly Invented a Made-in-America 3D Printer
It has become virtually impossible to regularly follow additive manufacturing (AM) industry news and not stumble across the term “defense industrial base” (DIB), a concept encompassing all the many diverse...
Inside The Barnes Global Advisors’ Vision for a Stronger AM Ecosystem
As additive manufacturing (AM) continues to revolutionize the industrial landscape, Pittsburgh-based consultancy The Barnes Global Advisors (TBGA) is helping shape what that future looks like. As the largest independent AM...
Ruggedized: How USMC Innovation Officer Matt Pine Navigates 3D Printing in the Military
Disclaimer: Matt Pine’s views are not the views of the Department of Defense nor the U.S. Marine Corps Throughout this decade thus far, the military’s adoption of additive manufacturing (AM)...
U.S. Congress Calls Out 3D Printing in Proposal for Commercial Reserve Manufacturing Network
Last week, the U.S. House of Representatives’ Appropriations Committee moved the FY 2026 defense bill forward to the House floor. Included in the legislation is a $131 million proposal for...