Leveraging their key strategic partnership, materials manufacturer Covestro and Chinese powder bed fusion company Farsoon want to create the best possible customer experience for end-use parts. In this collaboration, the duo will develop new engineering-grade powders for polymer parts to encourage 3D printed series production.
With Covestro contributing its expertise in polymer-based 3D printing materials and Farsoon deploying its know-how of powder-based laser sintering machines, the new polymer powder materials could help a wide range of applications, including automotive, electrical, and consumer goods. Covestro has already successfully launched TPU (thermoplastic polyurethane) and PBT (polybutylene terephthalate) polymer powders that were tested using Farsoon’s 252P high-temperature series platform, which made its debut at TCT Asia 2020 in July 2020.
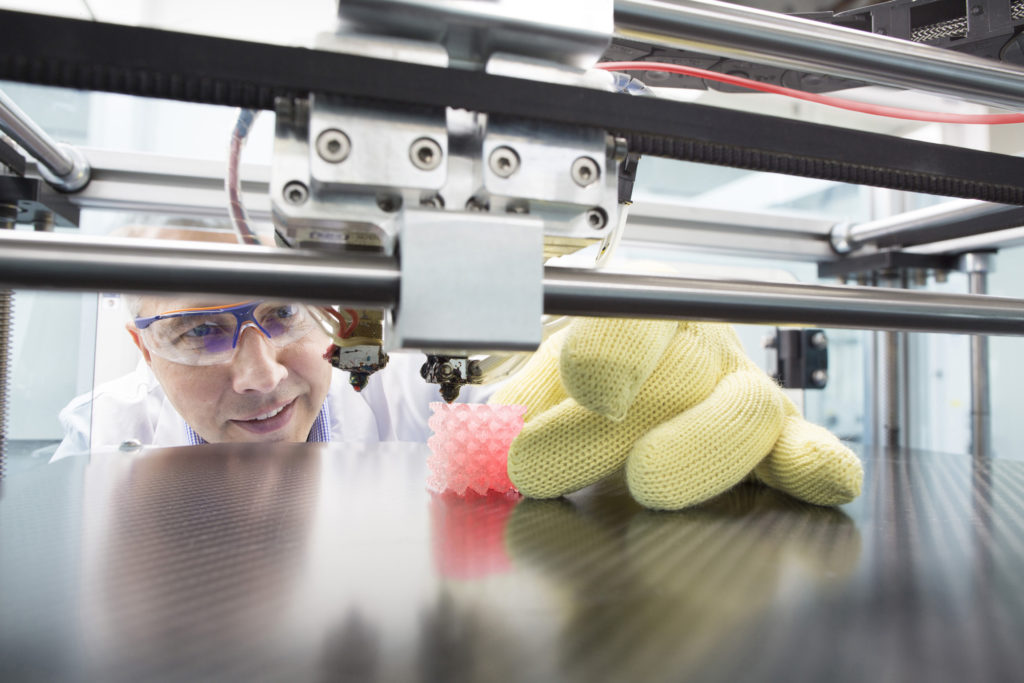
Covestro expert Roland Wagner observes the manufacture of a small component in the new 3D printing laboratory. Image courtesy of Covestro.
The German polymer manufacturer has been using its local AM facilities as well as operating its Dutch center (part of Covestro’s recently acquired DSM’s Resins & Functional Materials unit) to test the processing and printing of materials using Farsoon’s laser sintering systems. Additionally, several downstream customers have already validated such parts for end-use applications.
For example, with logistics and forwarding service provider Seifert Logistics Group (SLG) and its Additive Manufacturing Business unit in Ulm, Germany, Covestro and Farsoon jointly developed TPU parts for footwear using a Farsoon SS403P at high productivity levels. Similarly, they also teamed up with an undisclosed partner in the automotive industry to create end-use parts for interior car applications using a PBT powder originally developed by DSM called Arnite® T AM1210, commercially available for selective laser sintering (SLS).
It is based on this customer feedback and success that the two companies are strengthening their collaboration.
“By collaborating closely with printer manufacturers, we can test materials in the development process and provide customers verified material and printer solutions,” commented Geoff Gardner, Innovation Director Additive Manufacturing at Covestro. “Farsoon SL printers and especially their Flight™ Technology can run at standard and high temperatures so we can print PBT, PP and TPU all on the same printer. And with their higher accuracy and productivity, and lower cost per part, they are well suited for industrial production.”
Both firms are committed to an open-systems philosophy, so customers are free to choose materials for their 3D printing systems that suit their end-use applications. Since Farsoon launched China’s first high-end SLS machine in 2010, it has been focused on creating all genuinely open systems, which give operators the chance to optimize process parameters for the highest productivity at required part qualities for the material of choice. This complete freedom of operation means users have access to all parameter settings in the machine as well as any material source.
Moreover, the high-temperature and super-temperature configurations in Farsoon platforms allow process chamber temperatures of up to 220°C or 280°C, respectively. In addition, the machines are equipped with high-speed scanners and powerful lasers. Deploying its systems from Changsha, the capital of central China’s Hunan province, Farsoon is committed to making the fabrication of 3D printed parts cheaper. For example, with its trade-marked Fiber-laser Flight Technology, the high productivity of parts production makes series applications increasingly accessible.
Eager to “proactively support new applications with new polymer powders,” Farsoon Europe’s managing director Dirk Simon highlighted that Farsoon SLS machines are very compatible with Covestro’s polymer powders, offering a very interesting property profile to set an important foundation for its customers’ market success.
3D printing enthusiasts can witness the strengthened integration of these market-leading companies at Formnext 2021, which takes place November 16 through 19 in Frankfurt, Germany. Both companies will showcase their polymer powder materials and printers, Covestro at booth C11 and Farsoon at booth G 19, both located in Hall 12.1.
Subscribe to Our Email Newsletter
Stay up-to-date on all the latest news from the 3D printing industry and receive information and offers from third party vendors.
Print Services
Upload your 3D Models and get them printed quickly and efficiently.
You May Also Like
The Dental Additive Manufacturing Market Could Nearly Double by 2033, According to AM Research
According to an AM Research report from 2024, the medical device industry, specifically in dentistry, prosthetics, and audiology, is expected to see significant growth as these segments continue to benefit from...
Heating Up: 3D Systems’ Scott Green Discusses 3D Printing’s Potential in the Data Center Industry
The relentless rise of NVIDIA, the steadily increasing pledges of major private and public investments in national infrastructure projects around the world, and the general cultural obsession with AI have...
AM Research Webinar Explores Continuum’s Sustainable Metal Additive Manufacturing Powders
Metal additive manufacturing (AM) powder supplier Continuum Powders is working to develop solutions that empower industries to reduce waste and optimize their resources. An independent life cycle assessment (LCA) of...
3D Printed Footwear Startup Koobz Lands $7.2M in Seed Round
California-based Koobz is focused on reshoring the U.S. footwear supply chain with advanced manufacturing processes, including 3D printing. The startup just announced that it has added $6 million to its...