While the aerospace giants, like Airbus, are working to get 3D printed components into the largest of jumbo jets, additive manufacturing (AM) in aerospace is continuing apace across the industry. This includes the use of 3D printing for maintenance, repair, and overhaul (MRO), where a variety of firms, from Air New Zealand to Lufthansa, are exploring the use of the technology to produce on-demand replacement parts. So far, these have been the projects of larger airlines, but Cabin Management Systems (CMS) is using Markforged machines to 3D print parts for its own MRO services for luxury aircraft.
CMS is a comparatively new company, founded in 2019. It works alongside MRO companies and individual aircraft owners to create cabin control and entertainment systems for luxury, private, and business jets. Using two Markforged X7 3D printers, the company is 3D printing parts for maintenance, upgrades, and replacements of cabin management and entertainment systems.
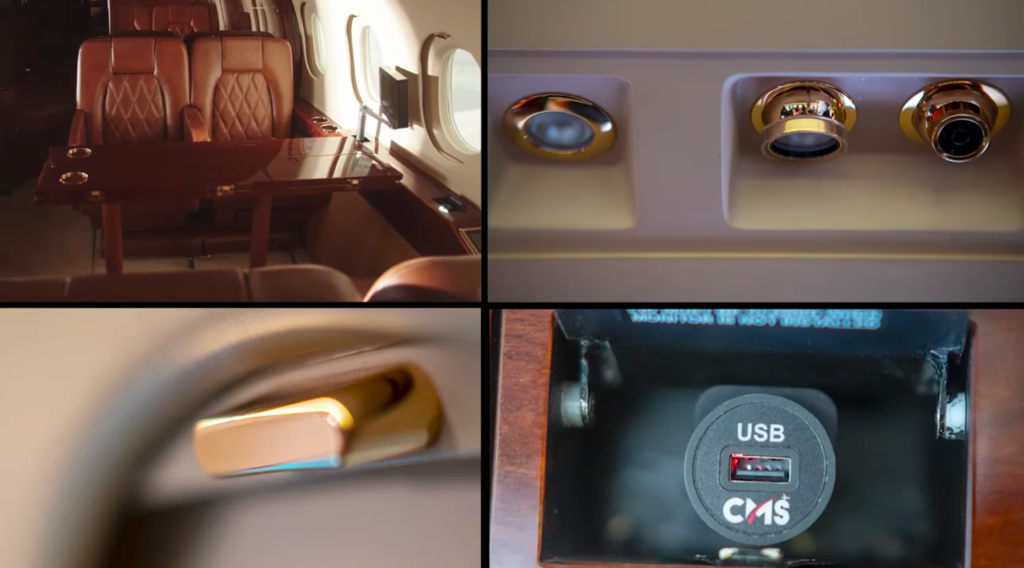
Parts made with Markforged Onyx FR by Cabin Management Systems. Image courtesy of Markforged/YouTube.
Key to the operation is the use of Markforged Onyx FR material, which offers the flame retardant properties and FAA compliance necessary for in-cabin items. Additionally, the components made with Onyx FR are described as high strength and low weight. Altogether, the process speeds up the time it takes to make new parts for an aircraft, but also allows the company to repair or replace obsolete items. Jeff Pike, VP of Engineering at CMS, explained how the technology is ideal for their niche sector:
“In the aerospace industry, quality and on-the-fly adaptability are crucial to success. We often have to produce low-volume, high-value parts from scratch which can be time- and labor-intensive. Markforged’s X7 allows us to do this quickly and more efficiently, while ensuring functionality and retaining the upscale aesthetics expected in luxury aircrafts.”
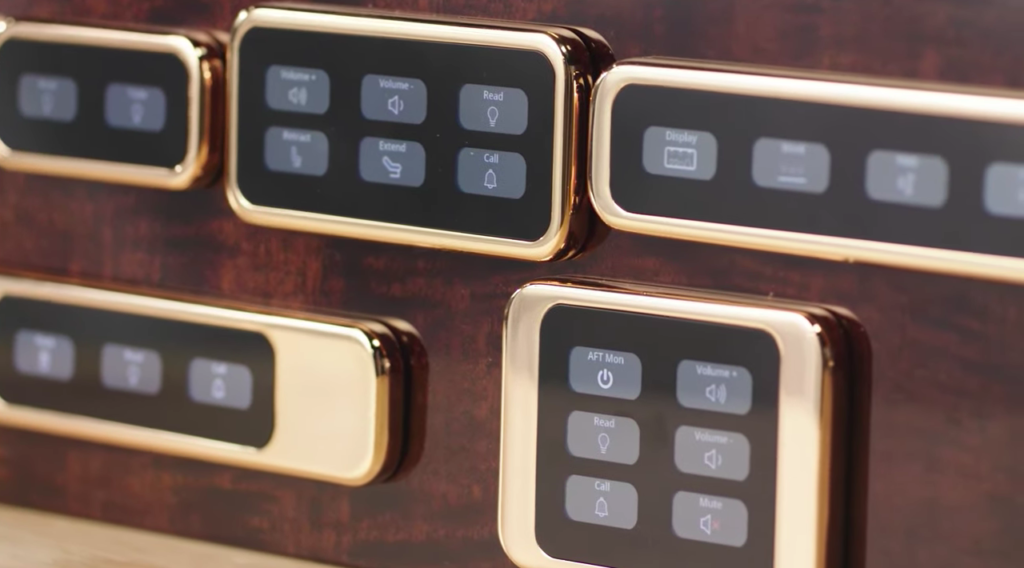
3D printed panel housings made with Markforged Onyx FR by Cabin Management Systems. Image courtesy of Markforged/YouTube.
In one case, the CMS team 3D printed some 100 parts for an aircraft. These included 20 light switch panels, a cabin climate controller, and USB-C and drop-in USB-A chargers, as well as latches, release buttons, and adjustable touch screen brackets. To create a luxury finish, the parts may be customized with inlays, such as gold metal electroplating or wood veneer.
At the moment, CMS must have its projects approved on a case-by-case basis; however, Markforged is in the process of qualifying aerospace-ready grades of its Onyx FR and Carbon Fiber FR materials by the National Center for Advanced Materials Performance. Once approved, Onyx FR-A and Carbon Fiber FR-A components will be able to be more quickly integrated into aircraft, allowing CMS to take on more jobs more quickly.
Subscribe to Our Email Newsletter
Stay up-to-date on all the latest news from the 3D printing industry and receive information and offers from third party vendors.
Print Services
Upload your 3D Models and get them printed quickly and efficiently.
You May Also Like
Reinventing Reindustrialization: Why NAVWAR Project Manager Spencer Koroly Invented a Made-in-America 3D Printer
It has become virtually impossible to regularly follow additive manufacturing (AM) industry news and not stumble across the term “defense industrial base” (DIB), a concept encompassing all the many diverse...
Inside The Barnes Global Advisors’ Vision for a Stronger AM Ecosystem
As additive manufacturing (AM) continues to revolutionize the industrial landscape, Pittsburgh-based consultancy The Barnes Global Advisors (TBGA) is helping shape what that future looks like. As the largest independent AM...
Ruggedized: How USMC Innovation Officer Matt Pine Navigates 3D Printing in the Military
Disclaimer: Matt Pine’s views are not the views of the Department of Defense nor the U.S. Marine Corps Throughout this decade thus far, the military’s adoption of additive manufacturing (AM)...
U.S. Congress Calls Out 3D Printing in Proposal for Commercial Reserve Manufacturing Network
Last week, the U.S. House of Representatives’ Appropriations Committee moved the FY 2026 defense bill forward to the House floor. Included in the legislation is a $131 million proposal for...