ExOne (Nasdaq: XONE) continues to showcase interesting developments, amid its ongoing acquisition by Desktop Metal. The metal and sand binder jetting pioneer has announced the ability to 3D print copper e-winding parts for electric motors. The motors, built by Tennessee startup Maxxwell Motors, rely on a unique axial flux design and could be used in electric cars, as well as heavy-duty vehicles and industrial equipment.
Established in 2018, Maxxwell has so far commercialized two products, a 10 KW air-cooled motor generator and a 150 kW liquid-cooled motor, as a part of its mission to create electric motors without rare-earth magnets. At its helm are Chairman Gary Wells, former CEO of Wells’ Dairy, and former General Motors executive Michael Paritee, Maxxwell’s CEO.
Among the components necessary for the shift from fossil fuel to hybrid and electric vehicles are copper windings and rotors. Existing designs are typically made in an inefficient and expensive manner. Moreover, their geometries are limited, thus hindering their overall performance.
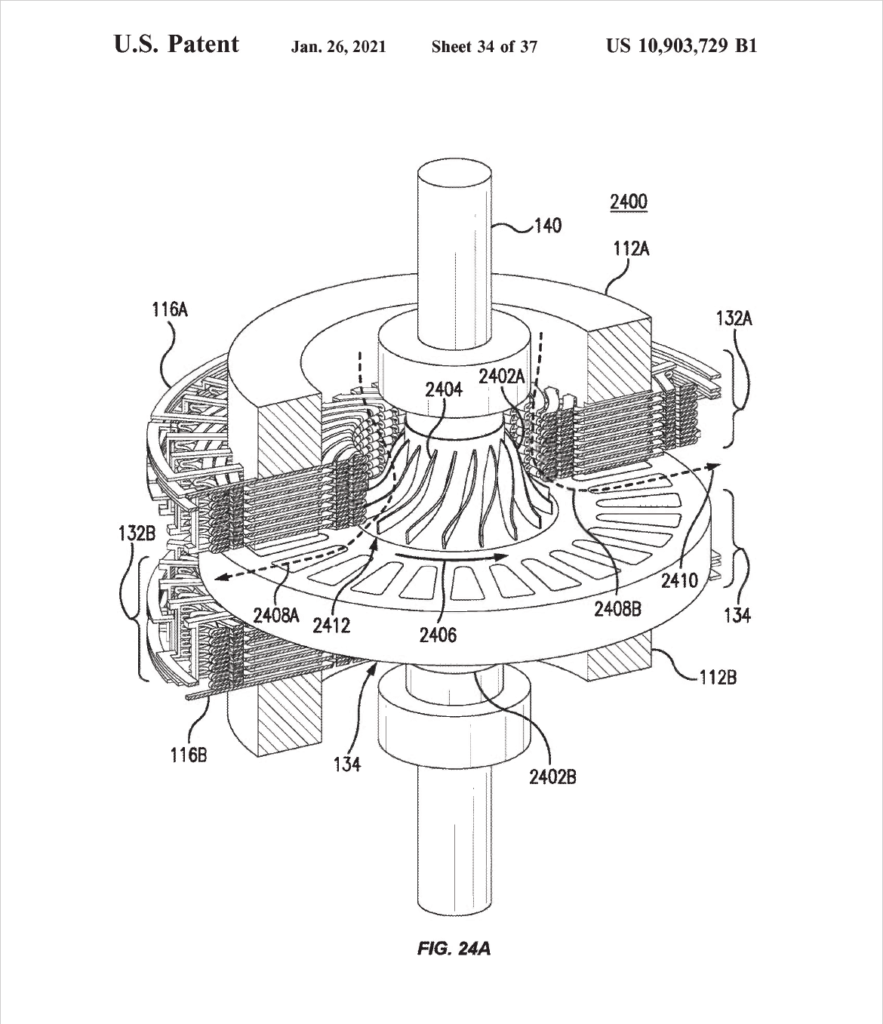
The 36 coils in areas 132A and 132B of this Maxxwell patent may be 3D printed under this partnership between ExOne and Maxxwell Motors. Image courtesy of ExOne.
With 3D printing, however, it’s possible to produce more complex copper designs, as we’ve seen from the induction coil segment. For Maxxwell, this means the ability to produce some of its more intricate designs. Among its nine patents is an electric motor design that features 36 copper coils for a stator winding that encapsulates the motors. With ExOne, the Tennessee firm aims to consolidate all of those coils into a single, 3D printed part.
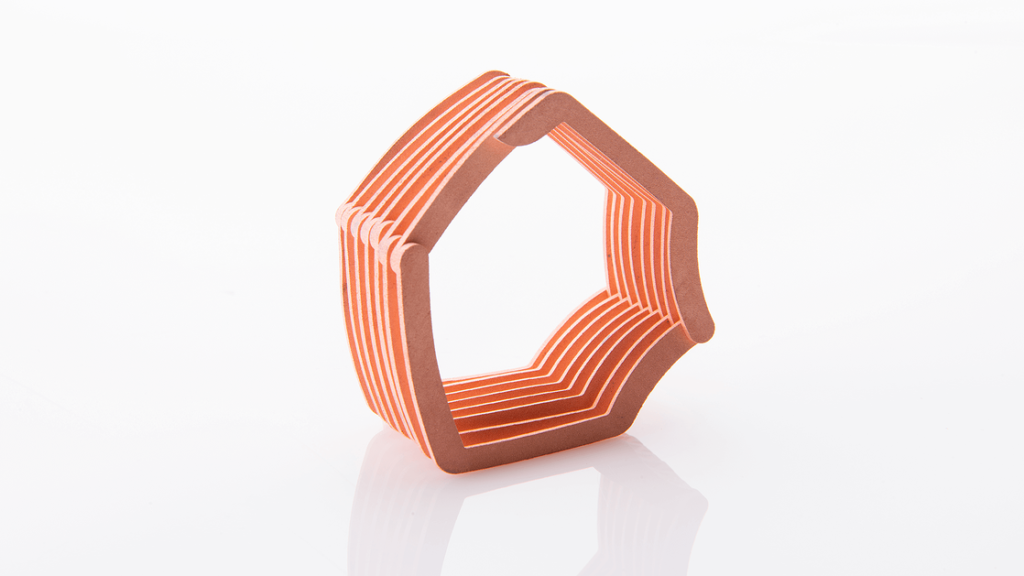
The demonstrator part 3D printed for Maxxwell Motors with ExOne’s binder jetting technology. Image courtesy of ExOne.
So far, the two companies have proven the feasibility of the concept by 3D printing a copper component, which is the first step in further developing the technology. Paritee said, “When we 3D print it, a lot of the challenges just go away, and we can actually improve the performance of the motor itself. At Maxxwell, we’re taking the most sustainable, and additive manufacturing, point of view as possible to truly improve efficiency, reduce waste and optimize performance.”
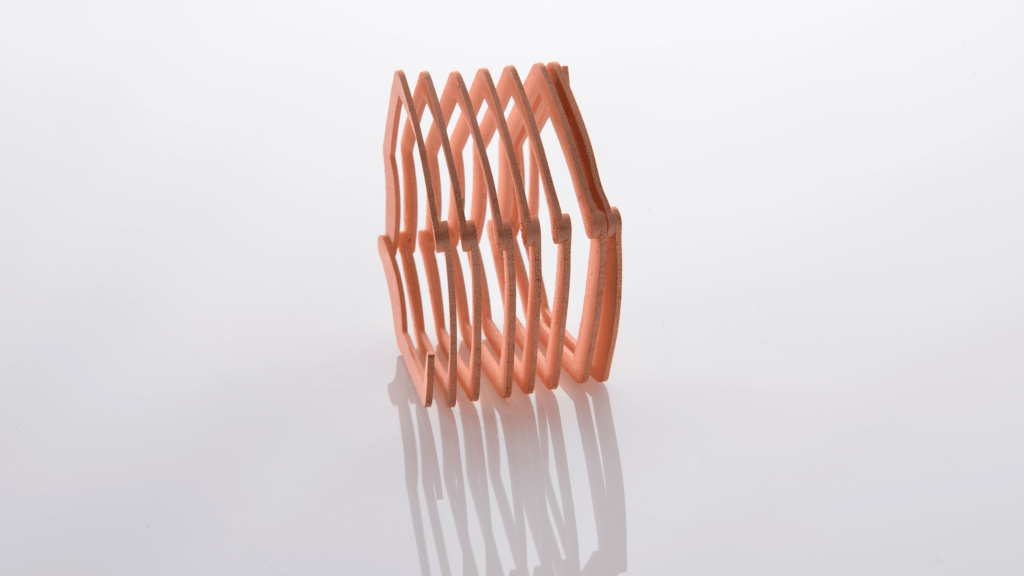
From another angle, a part proving out the concept of 3D printing copper parts for electric motors. Image courtesy of ExOne.
Copper is a thriving segment in additive manufacturing (AM). SmarTech Analysis anticipates more than 1.4 million kg of copper powder for 3D printing to ship by 2029, according to its Copper Additive Manufacturing 2020–Market Database and Outlook report. As of now, the dominating technology in this sector is powder bed fusion (PBF), with companies often modifying existing PBF machines to work with the highly reflective material. Because of copper’s reflectivity, greater energy levels are required or copper alloys are used to absorb more heat.
Bound metal printing, however, will be shaking up this niche, due to the fact that no lasers or electron beams are used. So far, companies like Markforged and Desktop Metal have demonstrated the ability to 3D print with pure copper using their bound metal extrusion systems. Now, with ExOne, there is greater potential for true mass production of copper parts, as metal binder jetting offers a higher throughput method for 3D printing with copper.
As the partnership progresses, Maxxwell aims to use binder jetting to 3D print complete winding assemblies as single, monolithic units. This would do away with the separate processes of coil wrapping, bending, tooling, and then welding the pieces together. Having just completed the development of aluminum 3D printing for Ford, ExOne may now be poised to apply its expertise to specific applications and materials until binder jetting becomes a permanent part of mass production for these firms.
Subscribe to Our Email Newsletter
Stay up-to-date on all the latest news from the 3D printing industry and receive information and offers from third party vendors.
Print Services
Upload your 3D Models and get them printed quickly and efficiently.
You May Also Like
Consolidation in AM: How 2025 Is Shaping the Industry’s New Normal
The first half of 2025 has been marked by a clear shift in the additive manufacturing (AM) industry. Companies are no longer just focused on developing new tech by themselves....
Etsy Design Rule Change Reduces Selection of 3D Printed Goods
Online marketplace Etsy has implemented a rule change requiring all 3D printed goods on the site to be original designs. The update to the site’s Creativity Standards states, ¨Items produced using...
U.S. Congress Calls Out 3D Printing in Proposal for Commercial Reserve Manufacturing Network
Last week, the U.S. House of Representatives’ Appropriations Committee moved the FY 2026 defense bill forward to the House floor. Included in the legislation is a $131 million proposal for...
Transforming From Tourist to Native: Duro CEO Michael Corr Explains Why the Company Rebuilt its PLM Software on AI
In these early innings of the AI boom, many market analysts have expressed concern that AI spend has gotten too far ahead of the technology’s proven ability to deliver significant...