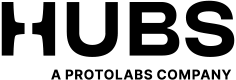
What’s the Best Way to Make Your Part?
CNC machining is a common subtractive manufacturing technology. Unlike 3D printing, the process typically begins with a solid block of material (blank) and removes material to achieve the required final shape, using a variety of sharp rotating tools or cutters.
CNC is one of the most popular manufacturing methods for both small one-off jobs and medium to high volume production. It offers excellent repeatability, high accuracy, and a wide range of materials and surface finishes.
Additive Manufacturing (AM) or 3D Printing processes build parts by adding material one layer at a time. AM processes require no special tooling or fixtures, so initial setup costs are kept to a minimum.
In this article, we present the key technology considerations to help you choose the right technology for your application. We focus on functional parts and prototypes made from metals or plastics. The 3D printing processes that are most suitable for this purpose are SLS or FDM for plastics and SLM/DMLS or Binder Jetting for metals.
Selecting the right technology
When choosing between CNC machining services and Additive Manufacturing (AM), there are a few simple guidelines that can be applied to the decision-making process.
As a rule of thumb, all parts that can be manufactured with limited effort through a subtractive process should generally be CNC machined. It usually only makes sense to use 3D printing in the following cases:
- When traditional methods are not able to produce the part, for example, for highly complex, topology-optimized geometries.
- When a fast turn-around time is critical, 3D printed parts can be delivered within 24h.
- When low-cost is essential, for small volumes, 3D printing is generally cheaper than CNC.
- When there is a small number of identical parts required (less than 10).
- When materials are required that cannot be easily machined, like metal superalloys or flexible TPU.
- CNC offers greater dimensional accuracy and produces parts with better mechanical properties in all 3 dimensions, but this usually comes at a greater cost, especially when volumes are small.
If higher part quantities are needed (hundreds or more), then neither CNC nor AM may be a cost-competitive option. Traditional forming technologies, such as investment casting or injection molding, are generally the most economic option due to mechanisms of economies of scale (see figure).
The total number of required parts is a key design consideration when selecting a manufacturing technology:
Case study: prototyping a plastic enclosure
While designing a new electronic appliance, fabricating prototypes for the enclosure is key for finalizing the product before mass manufacture. To accelerate the development time, fast lead time and low cost are the main objectives.
Electronic enclosures often have snap fits, living hinges, or other interlocking joints and fasteners. All these features can be either CNC machined or 3D printed with FDM or SLS.
CNC and SLS can be used to create prototypes of high accuracy and aesthetic appeal, but desktop FDM has a much shorter lead time and lower cost. Since mechanical performance is not the main objective of this project, the benefits of CNC prototyping and SLS are usually not worth the extra cost and time.
Rules of thumb
Selecting the right technology for your application is crucial and can be boiled down to the following rules of thumb:
- CNC machining is best suited for medium to high quantities (less than 250-500 parts) and relatively simple geometries.
- 3D printing is generally best for low quantities (or one-off prototypes) and complex geometries.
- When considering metals, CNC can be price competitive even for low quantities, but geometry limitations still apply.
- When quantities are high (more than 250 – 500 parts), other forming technologies are more suitable.

*Model complexity and number of parts are key considerations for selecting the right manufacturing process
Subscribe to Our Email Newsletter
Stay up-to-date on all the latest news from the 3D printing industry and receive information and offers from third party vendors.
Print Services
Upload your 3D Models and get them printed quickly and efficiently.
You May Also Like
3D Printing News Briefs, July 2, 2025: Copper Alloys, Defense Manufacturing, & More
We’re starting off with metals in today’s 3D Printing News Briefs, as Farsoon has unveiled a large-scale AM solution for copper alloys, and Meltio used its wire-laser metal solution to...
3DPOD 260: John Hart on VulcanForms, MIT, Desktop Metal and More
John Hart is a Professor at MIT; he´s also the director of the Laboratory for Manufacturing and Productivity as well as the director of the Center for Advanced Production Technologies....
3D Printing News Briefs, June 28, 2025: Defense Accelerator, Surgical Models, & More
In this weekend’s 3D Printing News Briefs, 3YOURMIND was selected to join an EU Defense Accelerator, and PTC has announced model-based definition (MBD) capabilities within Onshape. Finally, a study out...
EOS in India: AM’s Rising Star
EOS is doubling down on India. With a growing base of aerospace startups, new government policies, and a massive engineering workforce, India is quickly becoming one of the most important...