The new gravity-defying Jet Suit by UK-based jetpack manufacturer Gravity Industries will be 3D printed with thermoplastic polymer polypropylene and assembled in just days, thanks to a partnership with 3D printing specialist Ricoh 3D. Since 2017, Gravity has been focused on making human flight possible by pioneering aeronautical innovation and building the world’s first propulsion suit. After the success of its original Jet Suit, Gravity is reimagining its design and is working with the Ricoh 3D team once again on its next vision, the Gravity eSuit. This upcoming electric version of the Jet Suit will be revealed at the July 2021 Goodwood Festival of Speed in West Success, UK, where visitors will surely be wowed, just like they were in 2019 after seeing its flagship version soaring through the skies.
Usually compared to Iron Man’s “super energy-powered” battle suit, Gravity Industries’ Jet Suit was truly inspired by the fictional character’s unique flight system. The company’s Founder and Chief Test Pilot, Richard Browning, established the company to challenge perceived boundaries in human aviation. Although his journey began as an oil trader and Royal Marines Reservist, with a strong connection to flight and a long family tradition in the aviation space, Browning’s dream was to reimagine an entirely new form of human flight.
Browning’s Jet Suit relies on two mini fuel-powered jet engines on each arm, and one larger jet carried on the back to propel both pilot and gear off the ground. When fully fueled, it weighs about 30 kilos and can travel at speeds of up to 136 km per hour. The suits can be commissioned for roughly $40,000 or tested in a safe, controlled environment at Gravity’s Flight Facility at the Goodwood Estate, located just 90 minutes outside London.
The sleek suit has already been tested by special forces worldwide, including the Netherlands Marine Corps and the Royal Marines in the UK. For example, the elite commandos can use them to board an in-motion military ship for rescue missions or as a quick option to board a ship taken over by pirates. In fact, the last four years have already seen Gravity take its Jet Suit from an idea on a page to over 115 public events in 33 countries, search and rescue trials, commercial flight training, and even racing on British motor show Top Gear.
Browning’s team had already been working on leveraging 3D printing with Ricoh 3D for its pioneering Jet Suit and is now developing components for the launch of Gravity’s upcoming eSuit. Gravity wanted to build Jet Suits that blended mind, body, and machine, which ultimately required a material that mimicked organic matter and would enable a flight experience that was both comfortable and safe. Ricoh’s flagship material, polypropylene, ticked every box. Characterized by its strength, chemical resistance, lightweight, and flexibility, the 3D printed polypropylene is a unique product that enables manufacturers to prototype in the end-use material, providing Gravity with much-needed design freedom.
According to Browning, the design freedom of 3D printing reduces the suit’s part count significantly by consolidating several assemblies into one, with far fewer components to glue and bolt than would be necessary with other manufacturing methods. Polypropylene also makes it possible to create multifunctional components, with lots of internal flow parts which move air through the Suit to keep it cool.
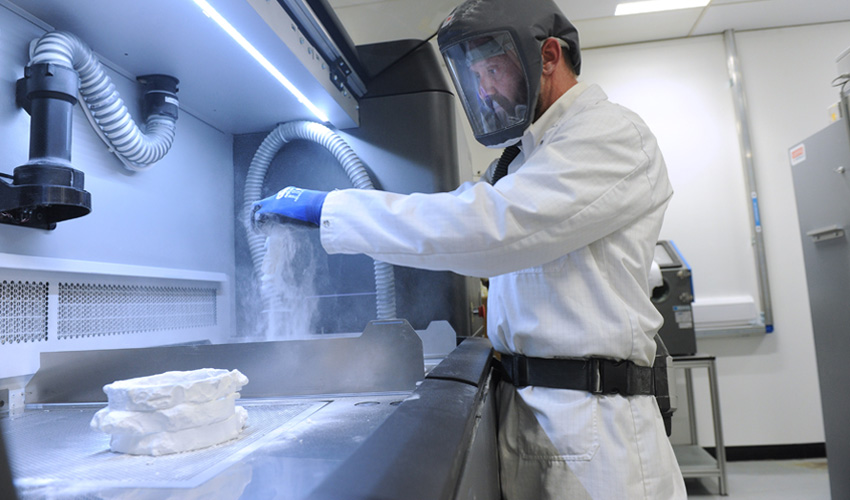
Ricoh provides industry 3D printing and additive manufacturing services across Europe. Image courtesy of Ricoh.
“Our partnership with Ricoh 3D has shown that anything is possible when you blend together entrepreneurship and technological innovation. Humans are extremely robust, and that’s down to the forgiving nature of our bodies – we bend and flex, reducing the impact when we fall. That’s what polypropylene mimics. I’ve always had a passion for unusual challenges and venturing into the unknown, so it’s incredible to see the dream ignite into life. We’ve built up an amazing global footprint since 2017, and Ricoh has enabled us to transform an ‘impossible’ idea into something viable for production.”
3D printed polypropylene is 90% recyclable, lightweight and flexible while still incredibly durable, making it ideal for “taking to the skies,” indicated Mark Dickin, head of Ricoh’s European 3D printing operation. The company’s innovative team helped develop and support advanced manufacturing techniques to custom build the core Jet Suit structure in just 24 hours, a process that previously involved more than two weeks of custom building the core out of aluminum riveting and bolting it together manually. With 3D printing, assembly time has moved from two weeks to two days.

Founder and Chief Test Pilot Richard Browning in the Gravity Industries lab conducting several tests on the series 4 Jet Suit. Image courtesy of Gravity Industries.
By harnessing the unique properties of polypropylene and pushing the boundaries of 3D printing, Dickin says that Ricoh and Gravity are showcasing the disruptive possibilities of the technology: “The Jet Suit is testament to the tenacity of engineering.” The engineer also stated that through their continuing partnership, they are looking to develop components for the launch of Gravity’s forthcoming eSuit.
For Gravity’s Chief Designer, Sam Rogers, the joy of 3D printing is being able to incrementally tweak the design between iterations without commissioning all new moldings and without any of the repetitive, time-consuming delays of starting from scratch. Without the need to produce hundreds of prototypes, the process was much simpler, enabling the Ricoh team to focus on overcoming the “impossible” and creating a suit that “perfectly augments” the human body.
“Thanks to polypropylene and its organic nature, people see a human who is flying when someone is in the Jet Suit. They aren’t strapped into a device or seated in a vehicle, they appear to be genuinely flying and it’s that distinction that makes all the difference,” said Rogers.
Like with the original suit, bringing Gravity’s ambitious novel electric version to life means leverage cutting-edge additive technology. Using Ricoh 3D polypropylene and its capabilities to print large parts, the partners create lightweight and durable components for unique Jet Suits and significantly reduce part count by consolidating several assemblies into one. This fascinating collaboration is making human flight possible very fast.
Subscribe to Our Email Newsletter
Stay up-to-date on all the latest news from the 3D printing industry and receive information and offers from third party vendors.
Print Services
Upload your 3D Models and get them printed quickly and efficiently.
You May Also Like
Making 3D Printing Personal: How Faraz Faruqi Is Rethinking Digital Design at MIT CSAIL
What if your 3D printer could think more like an intelligent assistant, able to reason through a design idea, ask questions, and deliver something that works exactly the way the...
Reinventing Reindustrialization: Why NAVWAR Project Manager Spencer Koroly Invented a Made-in-America 3D Printer
It has become virtually impossible to regularly follow additive manufacturing (AM) industry news and not stumble across the term “defense industrial base” (DIB), a concept encompassing all the many diverse...
Heating Up: 3D Systems’ Scott Green Discusses 3D Printing’s Potential in the Data Center Industry
The relentless rise of NVIDIA, the steadily increasing pledges of major private and public investments in national infrastructure projects around the world, and the general cultural obsession with AI have...
Formlabs Teams Up with DMG MORI in Japan
In late June, Nick Graham, Chief Revenue Officer at Formlabs, announced on LinkedIn that the company had partnered with DMG MORI, one of the world’s leading machine tool companies, to...